High Volume PCB Assembly Services
- Over 50 Million Units Successfully Assembled
- ISO 9001 Certified
- 10,000+ Completed Projects Worldwide
- 1,500 Reviews on Google


Need high-volume PCB assembly Manufacturing Services?
Need high-volume PCB assembly services? As a leading PCBA manufacturer, we at OurPCB are ready to assist you.
OurPCB is a group of experienced professionals offering state-of-the-art PCB assembly services. With lots of happy customers all around the world, especially in the USA, you can trust OurPCB to deliver exceptional quality and service.”
To get started, request an online pcb quote today!
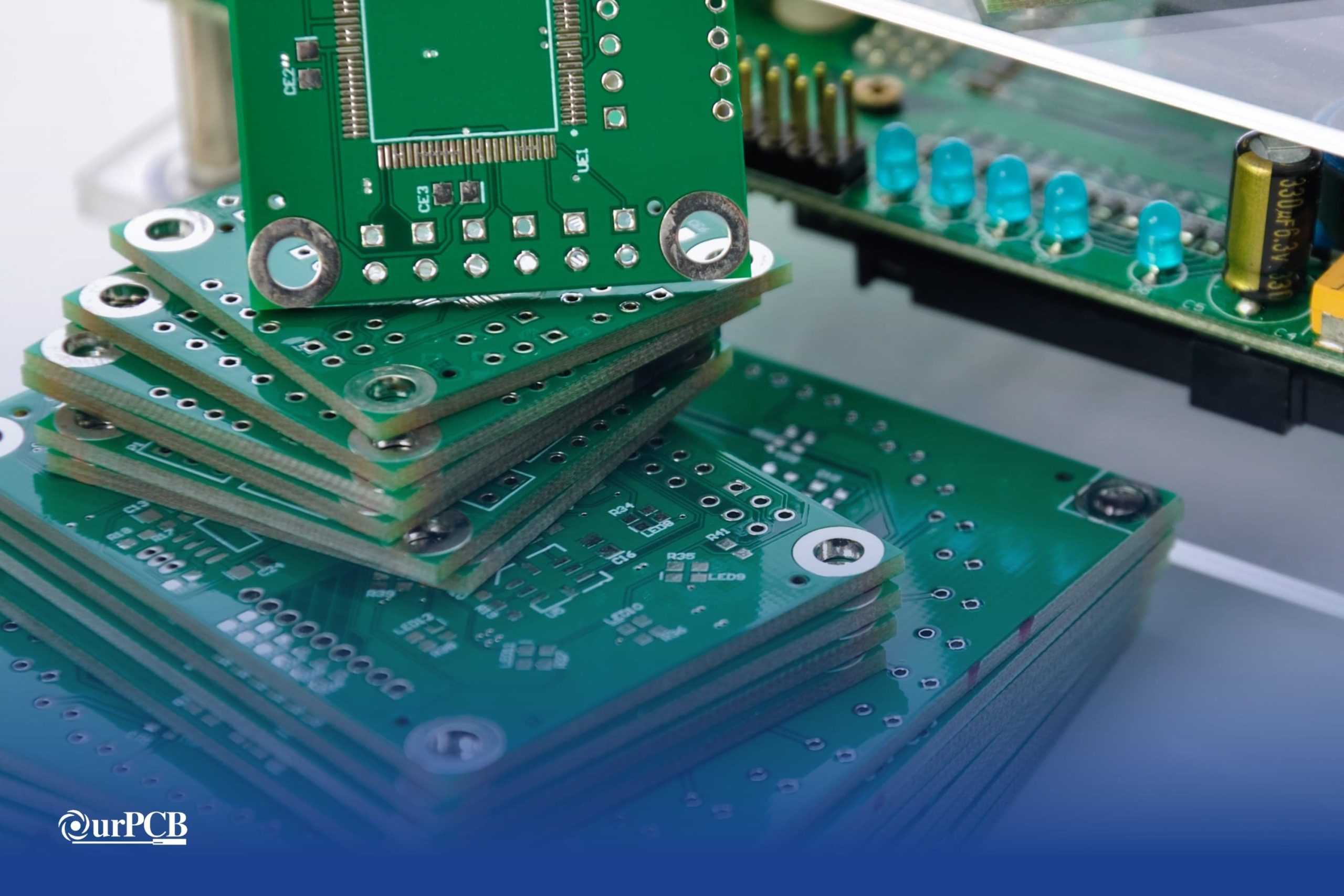
What is High Volume PCB Assembly?
High volume PCB assembly (HVPCBA) involves producing printed circuit boards in batches, starting from a minimum of 1000 to hundreds of thousands per run.
It’s a cost-effective way to capitalize on time that would otherwise be spent on prototyping, which is common with low-volume assembly. It provides bulk PCBs in short turnaround times to meet market demands.
High Volume PCB Assembly Technologies
Surface Mount Technology (SMT)
Single or double-side surface mount technology is highly efficient. Our assemblers use precision machines to mount components on the PCB’s surface.
The machines are primed for efficiency and accuracy to ensure they achieve miniaturization and maximum space usage. Automation ensures every PCB in the assembly line maintains the same standard of uniformity.
Through-Hole Technology
We use through-hole technology for PCBs in power-intensive applications. In this method, we insert electronic components into pre-drilled holes on the circuit board and solder them securely.
THT is suitable for producing PCBs that can withstand impact or tough conditions.
Mixed Single/Double Side Assembly
We use a combination of SMT and THT when we need to include power-intensive components on PCBs that undergo extreme electrical current.
Once we use SMT to place smaller components, we use THT to manually place bigger components that can handle mechanical stress.
High Volume PCB Assembly Equipment
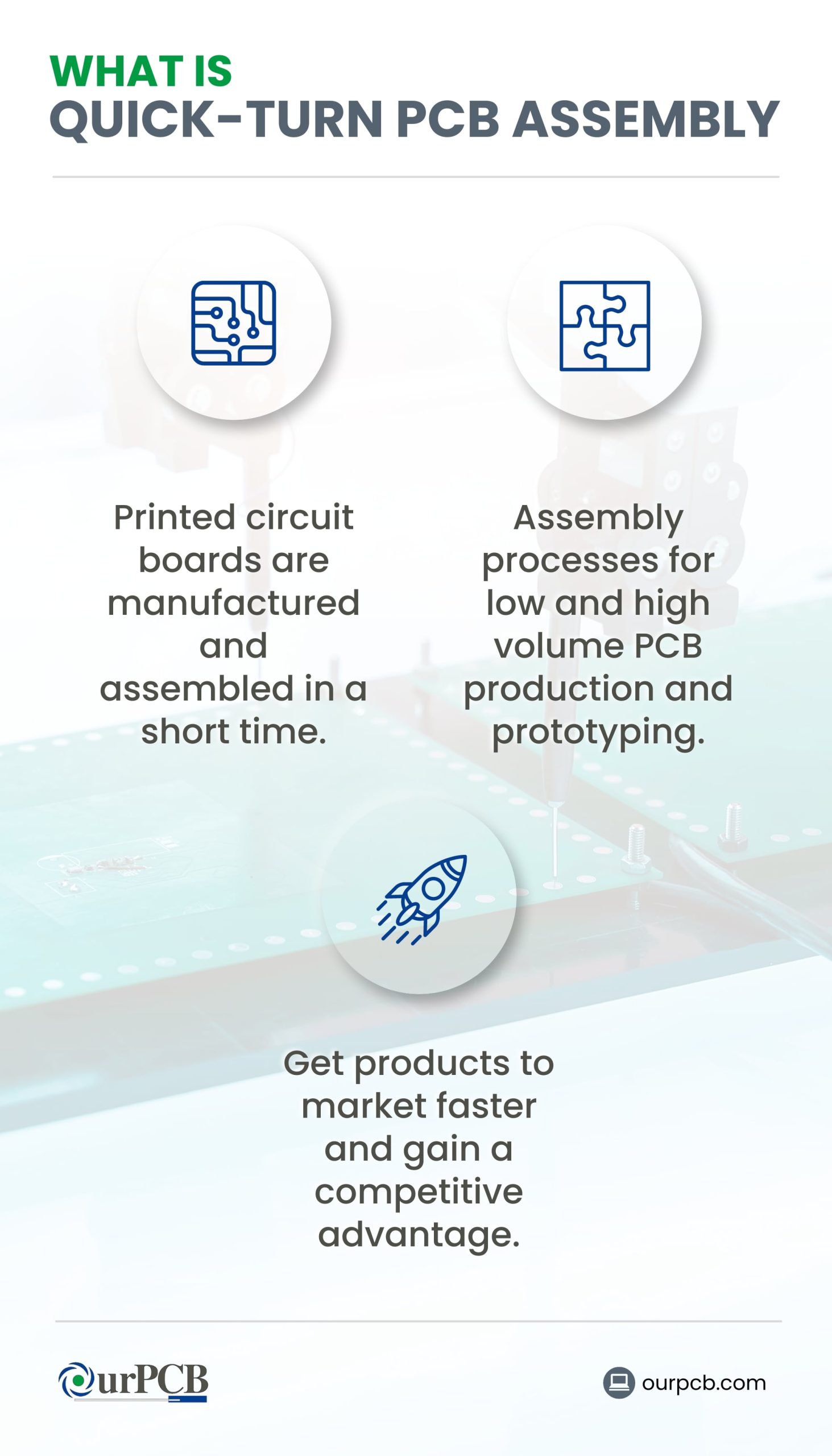
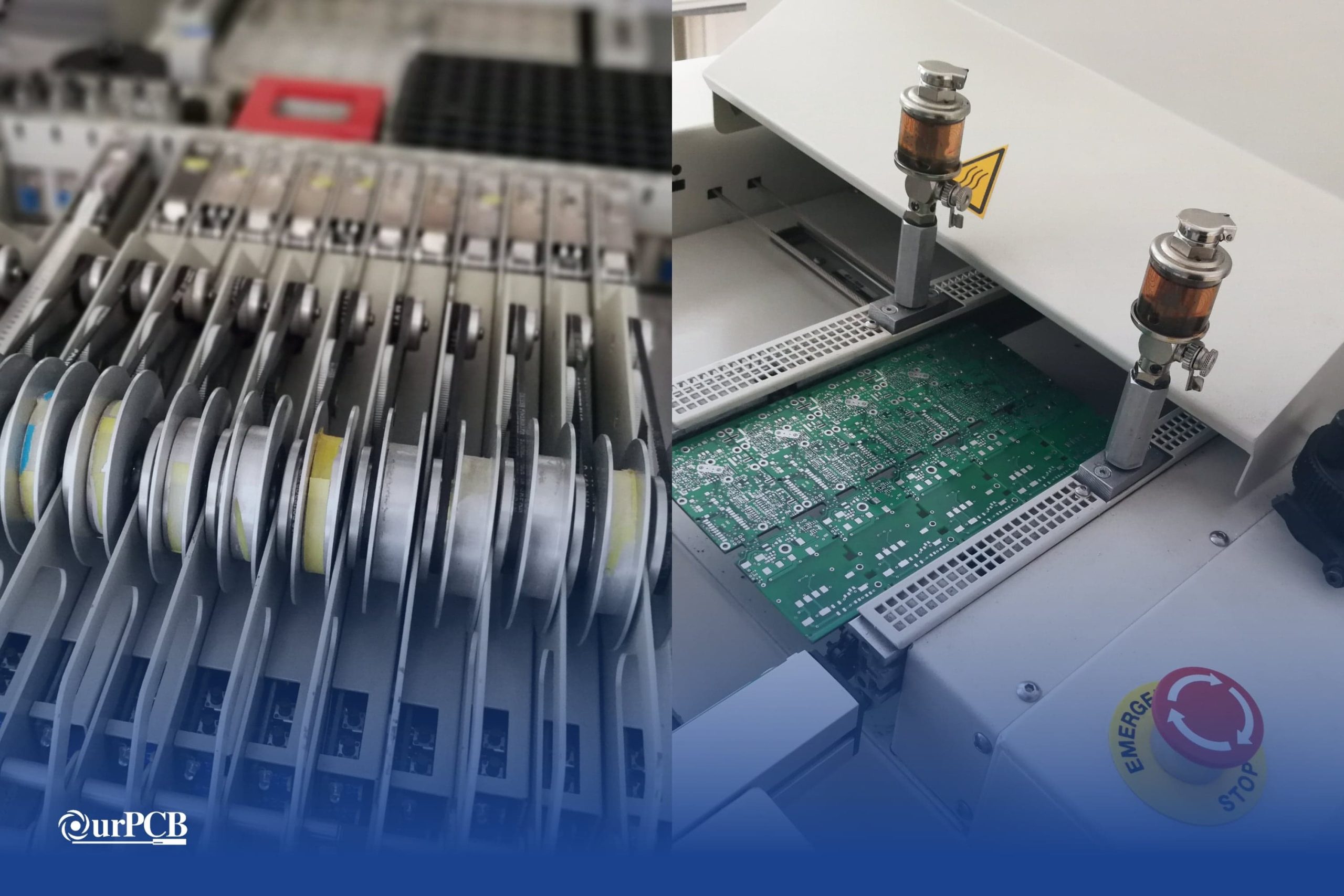
Pick and Place (P&P) Machines
We combine automation and pinpoint component placement when using pick-and-place machines to place surface components on the PCB.
P&P machines use vacuum nozzles to pick components up from trays and place them on PCB pads. These machines can make thousands of successful placements per hour. The end result is efficient boards, finished with accurate component placement.
Reflow Ovens
The key function of reflow ovens is to melt solder paste for soldering surface components to the PCBs. Without reflow ovens, you risk having inconsistent and weak solder joints.
Assemblies use three types of reflow ovens, for specific functions.
- Convention reflow ovens are a great bet for zero-lead soldering. They use chamber-generated hot air on the PCB. These are the most ideal choice for high volume assembly, since they complement pick-and-place machinery.
- Vapor phase reflow ovens ensure uniform heating using heat transfer and a medium such as fluorinated fluid. They have the advantage of being oxygen-free and minus the risk of overheating the assembly.
- Infrared (IR) reflow ovens use ceramic infrared heaters located at the top and the bottom of conveyors to radiate heat onto PCBs.
You need a professional team to handle your high-volume PCB assembly needs. Our global network is ready to exceed your expectations for top-quality PCBs.
Reach out now through any of our 24/7 available phone numbers or through email. Or, visit us today at any of our four physical locations and get a FREE QUOTE!
What’s the Difference between SMT vs. THT?
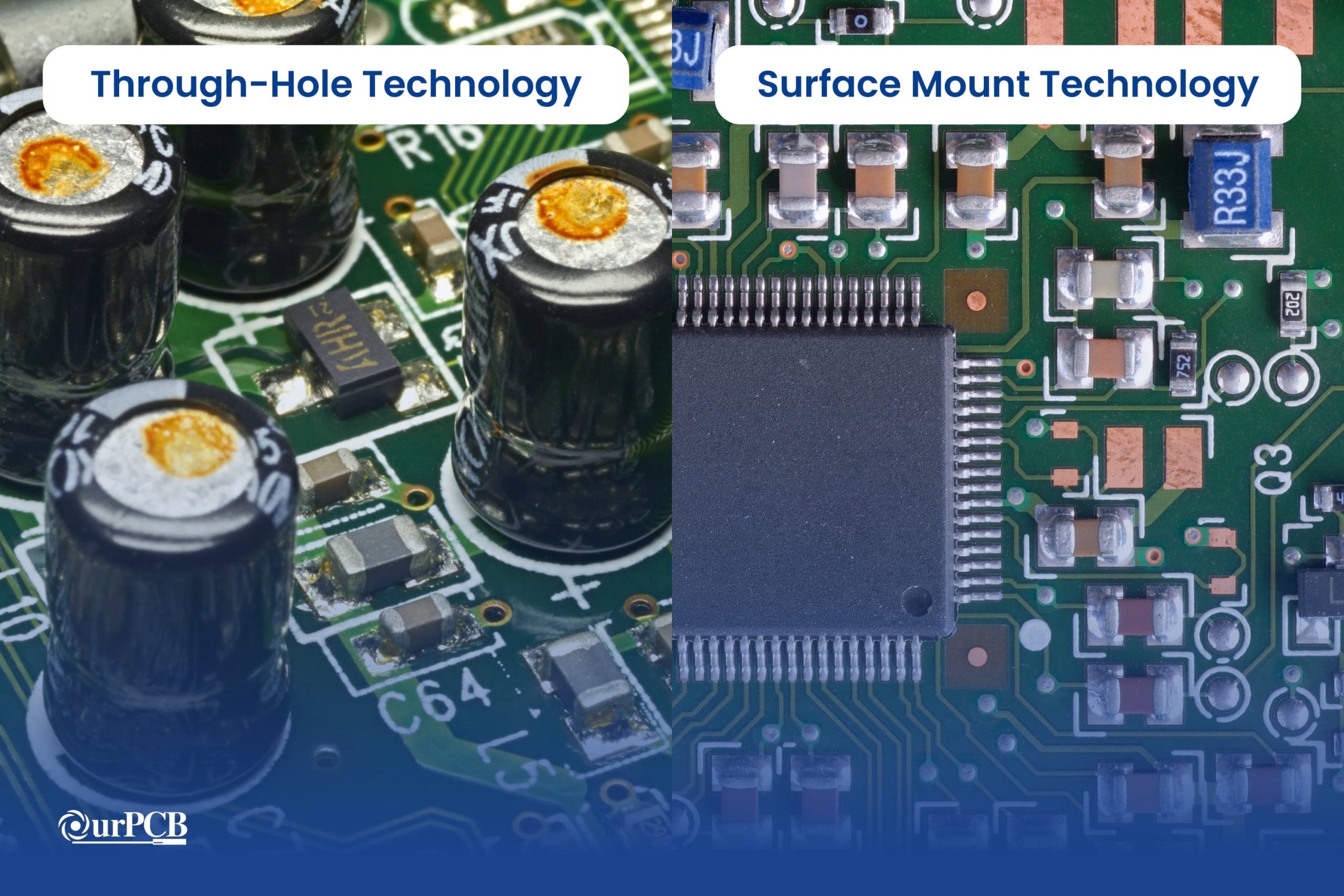
Through-hole technology focuses on providing structural firmness in high-impact applications. Manufacturers place THT components through pre-drilled holes and solder the back of the board.
Surface mount technology focuses more on maximum board space usage and precision. Therefore, manufacturers only solder SMT components directly on the PCB.
Cost-wise, SMT technology seems expensive in the initial stages. However, it’s a wise cost-saving strategy in high-volume PCB assembly. It costs less per unit since the SMT process is automated.
SMT Components | THT Components |
---|---|
Typically smaller and better for miniaturization | Often larger |
Use maximum space and make dense PCBs | Need lead space and hole spacing (during design and assembly) |
Easily repairable if faulty | Packing density make them harder to repair |
Include ICs and diodes (sometimes resistors) | Include capacitors and connectors |
Why Choose SMT for High-Volume PCB Assembly?
Surface Mount Technology is the go-to solution for high-volume assembly if you have limited timeframes, need precision, and work with smaller devices. Here’s why:
- SMT is primarily automated. It uses machines (reflow ovens, P&P machines and solder paste) for assembly and soldering. You reduce time between design and production to deliver the final boards.
- It’s possible to mass-produce smaller PCBs using surface mount technology. Once the designs are confirmed and a test-run is approved, SMT can produce thousands of small units in a short time.
- SMT doesn’t require pre-drilling. Direct-to-board component placement is faster and more accurate for high-volume production.
- SMT allows you to use both sides of the board. The final outcome is a double-sided board that’s useful in multiple applications.
- Due to the high demand for consumer electronics, SMT is optimal for complex circuit boards common in precision-specific applications like motherboards.
Still, we can combine THT and SMT in some cases.
Case 1: You Need Small and Large Components
You may need to produce consumer electronics with THT and SMT components. For example, electronics with microcontrollers and power connectors need mixed technology. Microcontrollers are placed using SMT, while the connectors are soldered using THT.
Case 2: Components Handle High Voltages
THT is typically reserved for high current/high voltage components. Industrial systems, power supply boards, and controllers in motor/aviation often undergo heavy current impact. As such, assembling PCBs with these specifics will require a combination of THT and SMT.
Case 3: Customized Designs
New designs or specialized repairs might call for both SMT and THT technology. Using both allows you to mesh different components. Repair using SMT and THT yields excellent results when you include newer components on the older design. That way, the previously damaged device is backward-compatible and has current upgraded features.
Case 4: Balancing Heat Dissipation and Structural Integrity
Imagine you’re producing PCBs for automotive engine controls. It’s a high-temperature environment with lots of small bits and pieces. THT and SMT allow you to include small components and components with excellent thermal management.
Case 5: When you Have External Connectors
Any device with connectors such as USB ports and switches needs mechanical and structural stability. However, these devices also have smaller components. THT ensures the external components are placed for durability, while SMT makes sure the small inner components are accurately placed.
The HVPCB Assembly Process
High volume PCB assembly is a 5-step process. Each step is automated to maintain uniformity in all the units on the production line.
Solder Paste Stencil Printing
The manufacturer places a thin metal foil over the board. The laser-cut stencil foil has apertures that align with the PCB’s solder pads. Solder paste passes through the stencil, fills the aperture, and sticks to the PCB.
As a first step, solder paste stencil printing must be precise for attaching components. Assemblers must also ensure they use only the right amount of solder paste in the designated spots. That way, they’ll find it easier to establish working connections during soldering.
Pick and Place
Once the locations are set in step one, P&P machines collect components from trays. The high-speed machines place the components on the PCBs. The solder paste in the above step keeps the components on the board.
Reflow Soldering
The manufacturer places the PCBs in a conduction reflow oven set to a specific temperature (100°C to 300°C) or (212°F to 572°F). Temperature control ensures the solder paste reflows and makes firm solder joints.
Once heated to the right temperature, the PCBs are set aside to cool and solidify the joints. Correct reflow soldering with accurate temperature control ensures the board has total electrical conductivity and stable component placement.
Inspection and Quality Control
Inspection is in three stages. This thorough inspection prevents the delivery of faulty boards and possible extra repair costs.
The first inspection is automated optical inspection (AOI), in which cameras scan the board for defects such as missing, misaligned, or misplaced components.
Afterward, solder paste inspection checks the quality of solder paste deposition, noting if there are any voids. The final inspection, X-ray inspection, looks for any hidden defects that might not be visible on the surface.
Functional Testing
The developed and visually tested pcb board prototype goes through operational testing. The manufacturer checks the board for signal transmission, power, and communication pathway efficiency using the design and technical development guidelines as a reference.
It’s certified as complete and functional for the end-user once it passes the functional test.
Benefits of High Volume PCB Assembly
Long-Term Cost Efficiency
Unlike small-scale production, high volume PCB assembly cuts down on prototype development, testing, and approval time. Once the initial design is approved, mass production is fast. Also, it’s easier to get favorable costs per unit when purchasing components in bulk.
Faster Turnaround
High volume PCB assembly is automated, from stencil printing to functional testing. Since it uses high-speed precision machines, you can get a minimum of 1000 units in a short time.
Consistency & Quality
All the automated machines and processes are inspected for precision and accuracy. This ensures that the final boards come out uniformly and with no errors. The assembled boards also go through multiple testing stages to make sure end users get error-free PCBs.
Scalability
High volume PCB assembly can boost your production from small scale to global production.
You can easily ramp up production from 1000 units to 100000+ units to meet market demands.
Alternatively, you can reduce production with ease, to accommodate decreased demand. It’s an efficient model for a business looking to grow organically.
What Industries Use High Volume PCB Assembly?
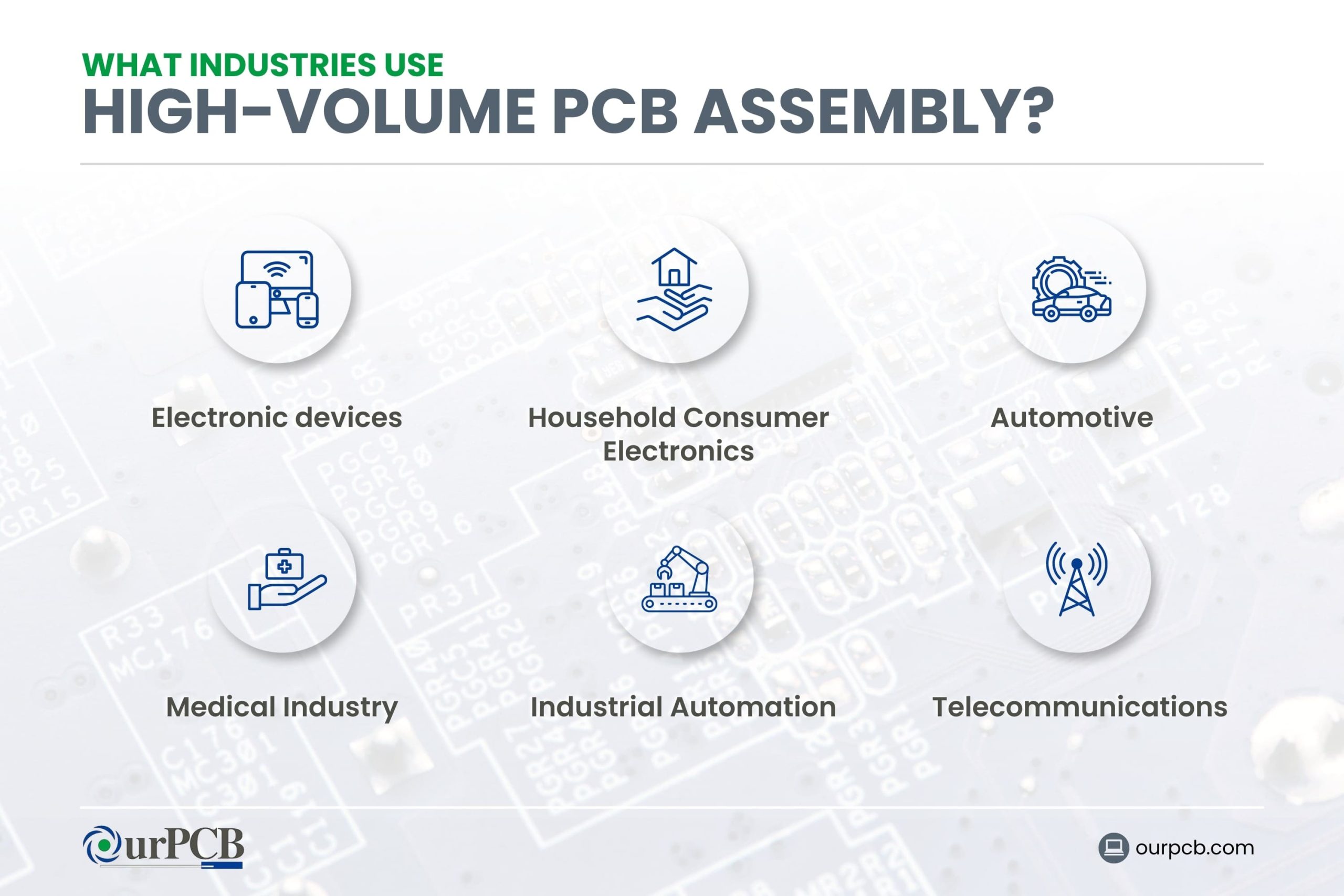

High volume PCB assembly is part of virtually every core sector.
- Household consumer electronics: Thousands of companies producing household consumer electronics for billions of households rely on HVPCBA. Microwaves, TVs, sound systems, and more all rely on precision to function properly.
- Electronic devices: There’s a constant massive demand for smartphones, personal computers, and associated gadgets. High-volume automated PCB assembly helps achieve the balance between mass demand and accurate production.
- Automotive: Interior support systems in automobiles, including engine control panels, infotainment systems, safety systems, and electrical control systems, require high-volume PCB assembly.
- Medical industry: Medical equipment is highly sensitive. Think of diagnostic, surgery, and monitoring machines. These systems all use PCBs that are products of precision high volume assembly.
- Industrial automation: Commercial/large-scale industries rely on automation to achieve maximum productivity. Factories that run on robotics, sensors, and control systems need a constant supply of reliable high-volume PCBs that can withstand strenuous conditions.
- Telecommunications: Telecommunication devices require multiple complex PCBs to run. You need high volume assembly to match the demand. Routers, network switches, cell towers, and wearable mobile devices all depend on these PCBs to run.
Why Choose OurPCB as Your High Volume PCB Assembly Partner?
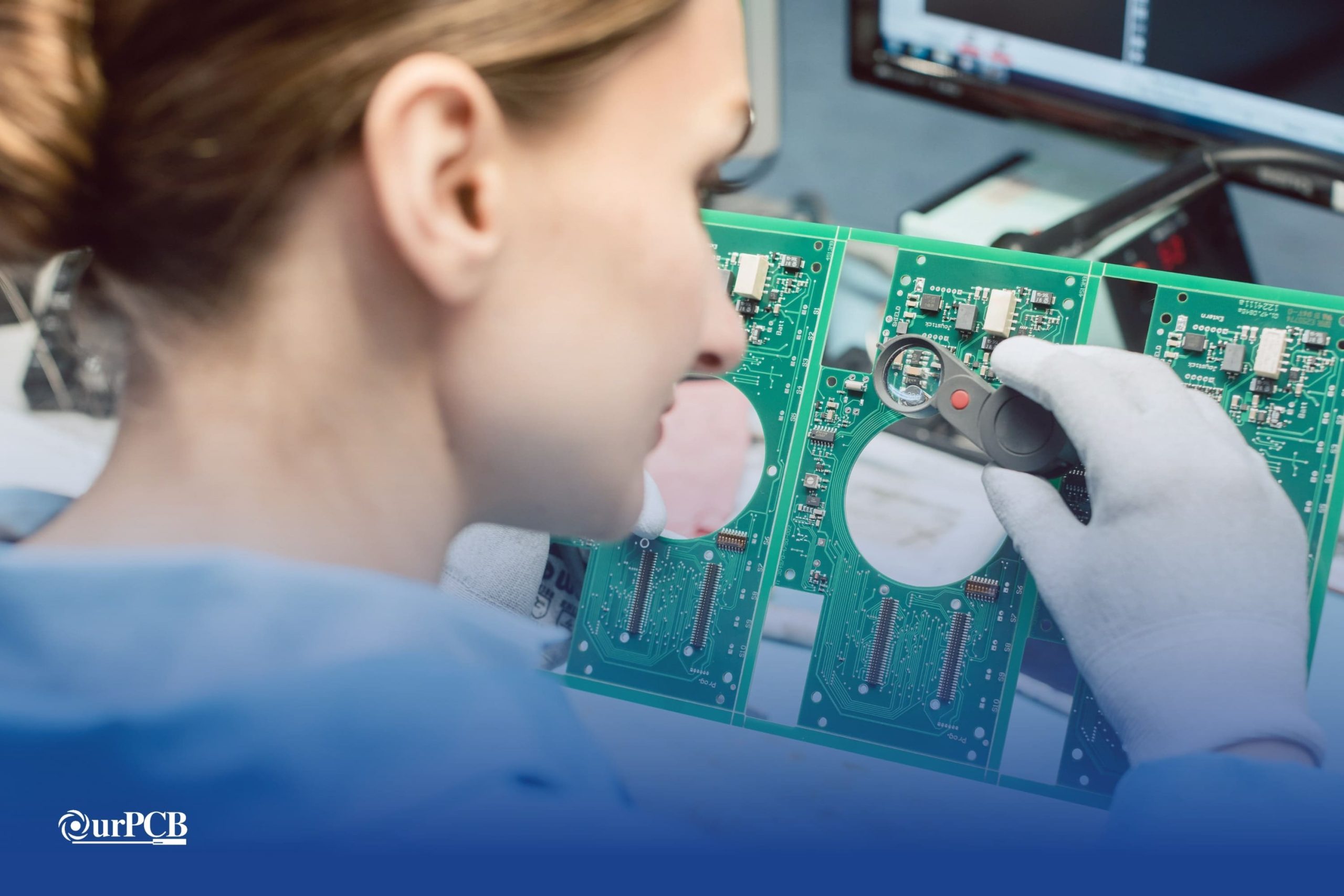
Selecting a skilled and experienced HVPCBA provider is critical to your project’s success. Here’s why we’re the obvious choice.
Experience and Capabilities
We have a 15-year track record and a good rapport with over 2,000 global customers. Whether rigid PCBs, flex PCBs, or column grid arrays (CGAs), we can cover large-scale production to your design specifications suited for any industry. Our experience allows us to deliver error-free PCBs even when faced with production hitches.
Quality Control
You can trust us to run your PCB production from start to finish. Not only do we use top-of-the-range equipment (7YAMAHA SMT lines) in our factories, but we also meet ISO 9001-2015 certification.
We rely on a network of trusted partners to source components according to your preference. Furthermore, we have a line-up of industry-standard visual and beyond-surface-level testing machinery to ensure you get error-free PCBs.
Scalability
We understand your need to grow and expand. Borrowing from the experiences we’ve had with other partners, we can customize assembly plans that suit your production demands.
We grow with you, maintaining tight time schedules and meeting delivery deadlines. As you expand operations, we can increase production accordingly. The best part is you don’t have to worry about diminishing quality as production goes up.
Clear and Prompt Communication
We maintain an active communication line, in case you want to make changes during the assembly process. We’ll assign you a qualified project manager who understands your demands to take your feedback and give you timely updates.
Get Started with High Volume PCB Assembly
OurPCB is a leading provider of quality high volume PCB assembly services. Our experienced team and advanced capabilities ensure reliable and cost-effective solutions for your large-scale PCB production needs.
Get in touch and begin your production today. Visit our physical sites, email, or call us to schedule a consultation with our production experts and get a FREE quote today.
Services Related to High Volume PCB Assembly
- PCB Assembly Services: Comprehensive solutions for assembling printed circuit boards.
- Quick Turn PCB Assembly: Fast and efficient PCB assembly to meet tight deadlines.
- High Volume PCB Assembly: Scalable solutions for large-scale PCB production.
- Flexible PCB Manufacturing: Specialized in manufacturing flexible PCBs for diverse applications.
- Low Volume PCB Assembly: Cost-effective solutions for small batch PCB assembly.
- Turnkey PCB Assembly: End-to-end services covering all aspects of PCB production.
- PCB Design Services: Expert design services to bring your PCB concepts to life.
- Rigid-Flex PCB Manufacturing: Manufacturing robust and versatile rigid-flex PCBs.
- PCB Prototype: Rapid prototyping services to test and refine your PCB designs.
- Rogers PCB: High-frequency PCBs ideal for RF and microwave applications.
- Aluminum PCB: PCBs with excellent heat dissipation properties, perfect for high-power devices.
- Metal Core PCB: Thermal PCBs with metal bases for effective heat management.
- High Tg PCB: High glass transition temperature PCBs for improved thermal performance.
- High Frequency PCB: Designed for high-speed and high-frequency applications, ensuring superior signal integrity.
- Heavy Copper PCB: Built with thicker copper layers for high current and enhanced thermal management.
- HDI PCB: High Density Interconnect PCBs offering advanced circuitry in a compact design for complex applications.
- Custom Cable Assembly: We offer a wide range of customized cable services, hybrid cables, and wire harnesses.
- Turnkey PCB Assembly: Our comprehensive solutions cover everything from design to production and testing, ensuring quality and efficiency while saving you time and cost
Conclusion
Electronic devices make life more convenient. However, they need accuracy to work properly and last a long time. With the constant global demand for electronics, there’s an equal demand for accurate, error-free PCBs. High volume PCB assembly is able to meet those demands.
Reach out to us and get a free quote or place your order. We’ll keep in touch with you from the design stage to delivery.
Back to top: High Volume PCB Assembly
- Author Name: Callum Everhart
Item: High Volume PCB Assembly
Review Body: The high volume PCB assembly service provided by OurPCB is top-notch. They deliver high-quality boards quickly and efficiently. - Author Name: Araminta Harlow
Item: High Volume PCB Assembly
Review Body: OurPCB's high volume assembly services are reliable and meet all our requirements for quality and precision. - Author Name: Quillen Ashcroft
Item: High Volume PCB Assembly
Review Body: Exceptional service! OurPCB's high volume PCB assembly exceeded our expectations in terms of speed and quality. - Author Name: Thalia Fairchild
Item: High Volume PCB Assembly
Review Body: We are very satisfied with the high volume PCB assembly from OurPCB. The boards were delivered on time and functioned perfectly.
- 1Order and Procurement
- 2PCB Manufacturing and Preparation
- 3Assembly and Soldering
- 4Inspection and Quality Control
- 5Finalization and Shipping
- Bare PCB in 8 working hours
- PCBA with components in 2 working days
- Bare PCB manufacturing
- Components sourcing
- PCB assembling
- Wire harness manufacturing
- Casing /Housing manufacturing
- Programming/Testing
Adrian Leitch


Andrew Durrant


Andrew Peeler


Andrew Wood


Ben Thomas


Darren Larosa


Debra Beukes


Eastern Europe Archives


frankyc


Fred Van


Greg MacDonald


John Powell


Jonathan Pippard


Jordan Thurgood


Justin Regan


Mark A


Mark Pagura


Maryanne Hassell


Matthew O'Neill


mitch clark


Oli


Peter Lambert


Sasha Marks


Slavko Mali


SPI MX


Steve Visser


Steven Munari


Steven Vatev


Tane Pendragon


Tasmiah Khan


Trevor Gardner


Free Consultation
High Volume PCB Assembly FAQs
What are the Benefits of High-Volume PCB Assembly vs Lower Volume Methods?
HVPCBA is more cost effective than low volume production, especially as a long-term option. You’ll get a finished consignment of PCBs in a short turnaround time, keeping things streamlined.
High volume assembly is less prone to errors during production since the margins of error are reduced during design and prototyping. Automated assembly and inspection in HVPCBA also guarantees you uniform PCBs.
How is the Quality of High-Volume PCB Assemblies Ensured?
The first step to quality assurance in high-volume PCB assembly is choosing a manufacturer that meets ISO certifications. Also, the automated machines must be optimized for maximum precision. That way, there’s less chance of low quality right from the design and prototype phase.
Assembly materials and components must come from trusted suppliers. Once the PCBs pass manufacturing, further quality standards are enforced using various visual testing methods, such as automated optical inspection (AOI), in-circuit testing (ICT), and X-ray testing.
The final test, functional testing, is a rubber stamp on the operational integrity of the manufactured board.
What’s the Difference Between PCB and HDI PCB?
Unlike standard PCBs, <a href=”https://www.ourpcb.com/blog/high-density-interconnect/”>Higher Density interconnect (HDI) PCBs</a> can have more electrical connections on the board. That makes HDI PCBs preferable for automation and high volume PCB assembly.
Also, HDI PCBs have a lower stray capacitance and impedance, meaning they have better signal transmission than standard PCBs. These electrical conductivity differences might be because PCBs use through holes, whereas HDI PCBs use buried vias.
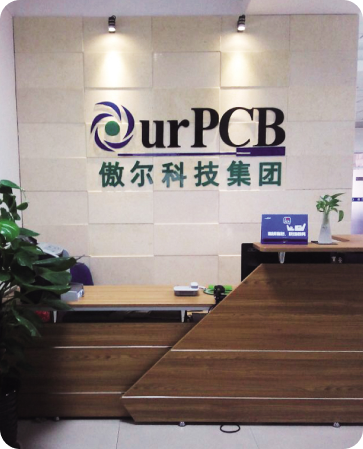
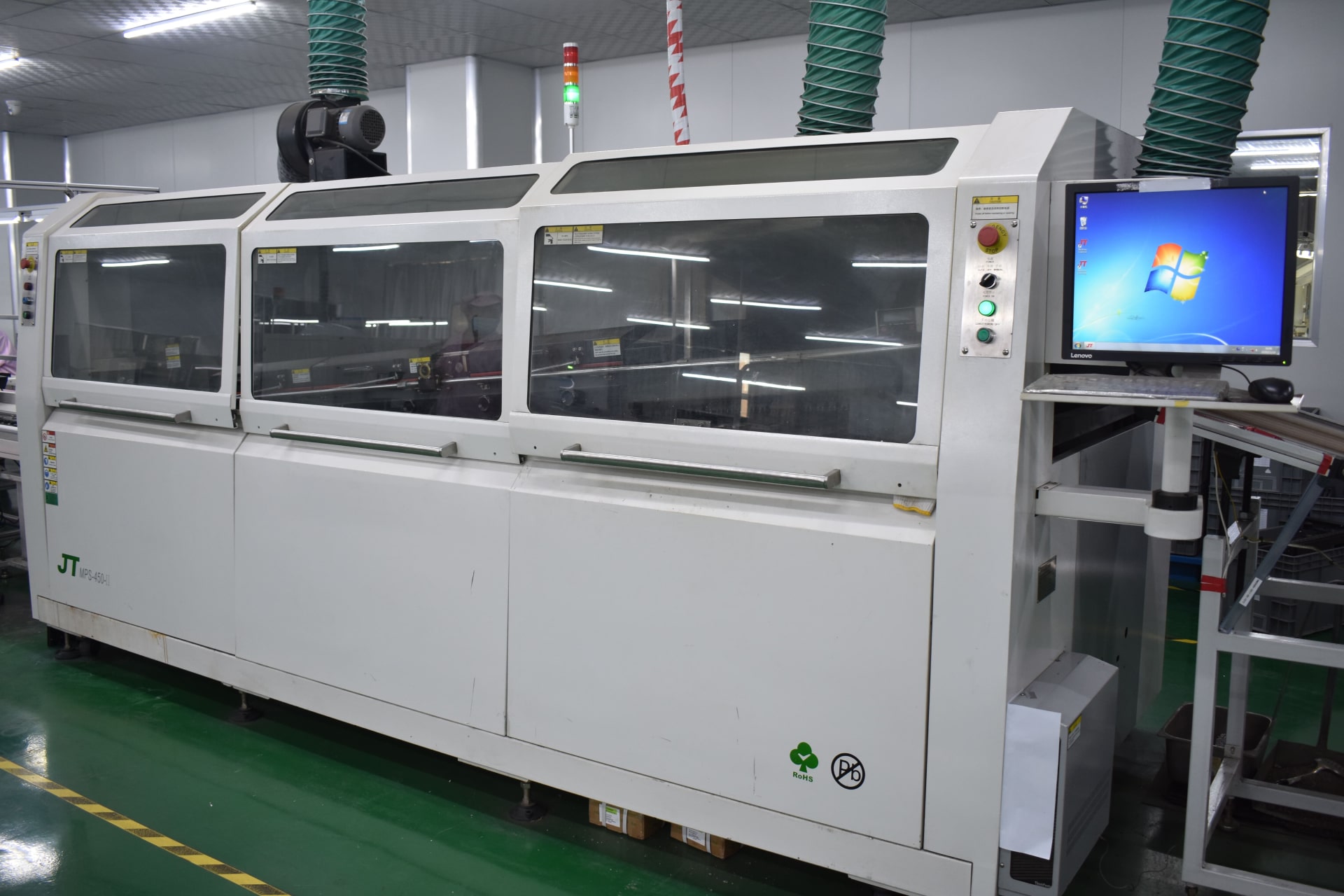

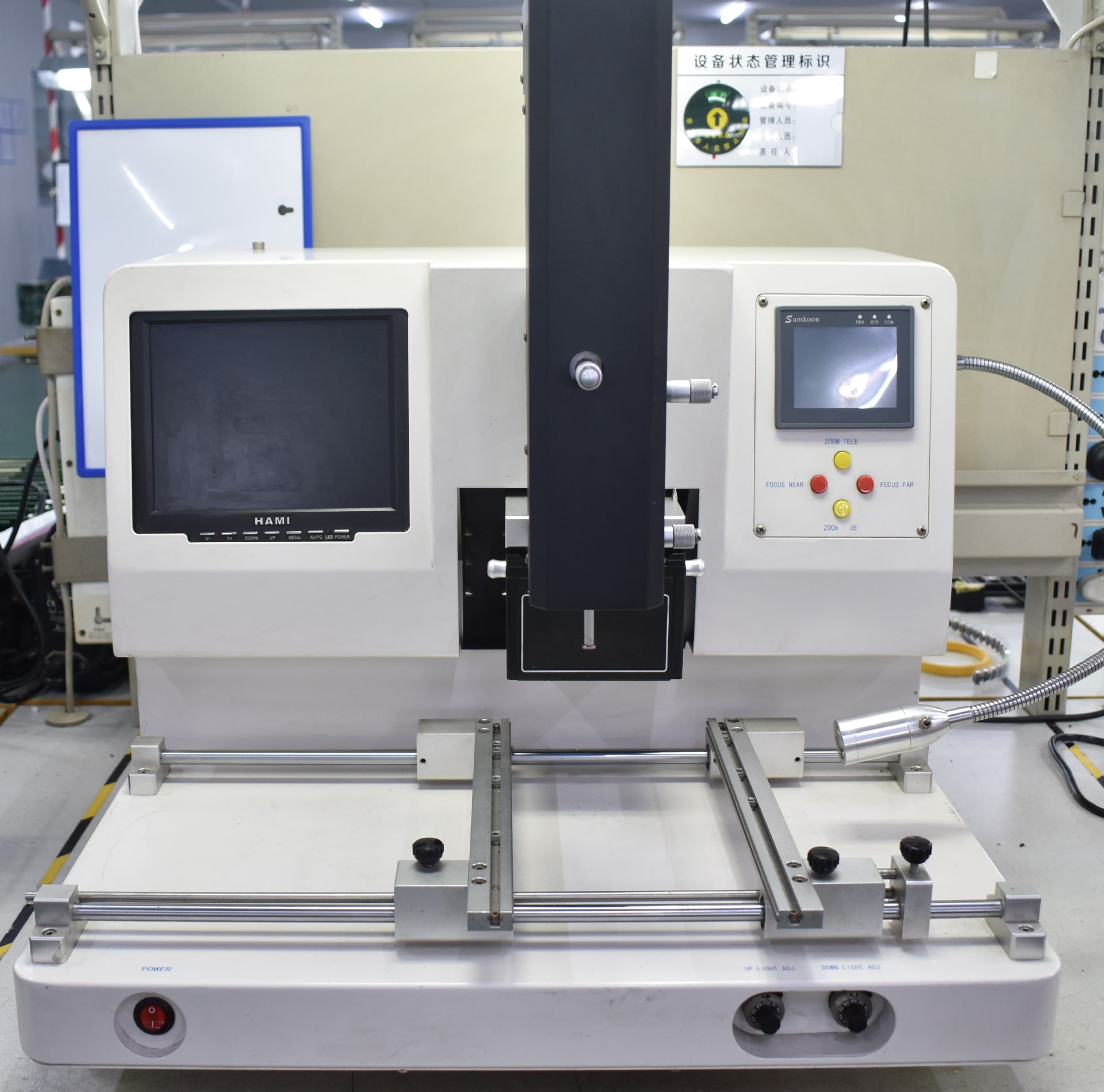
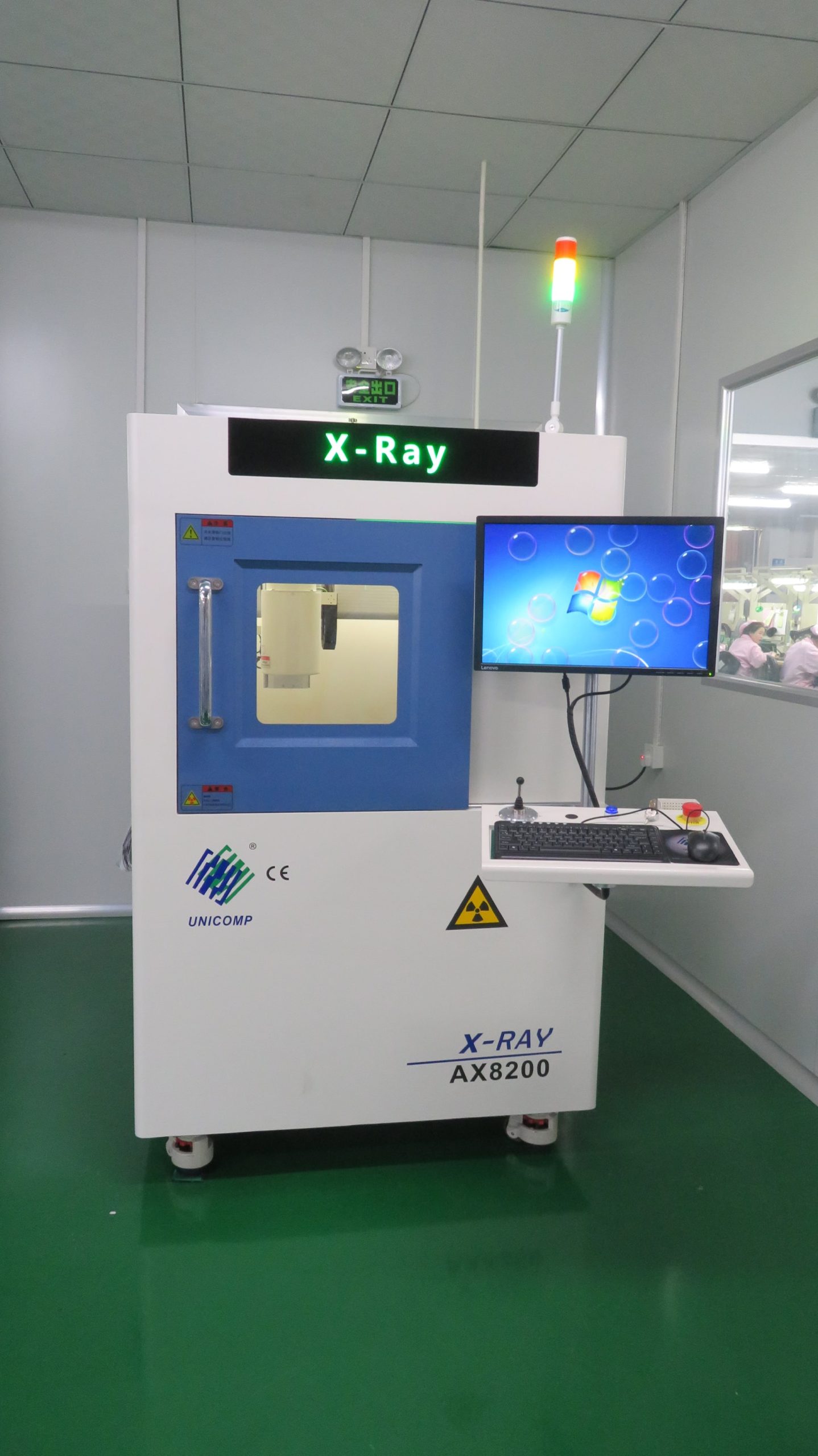
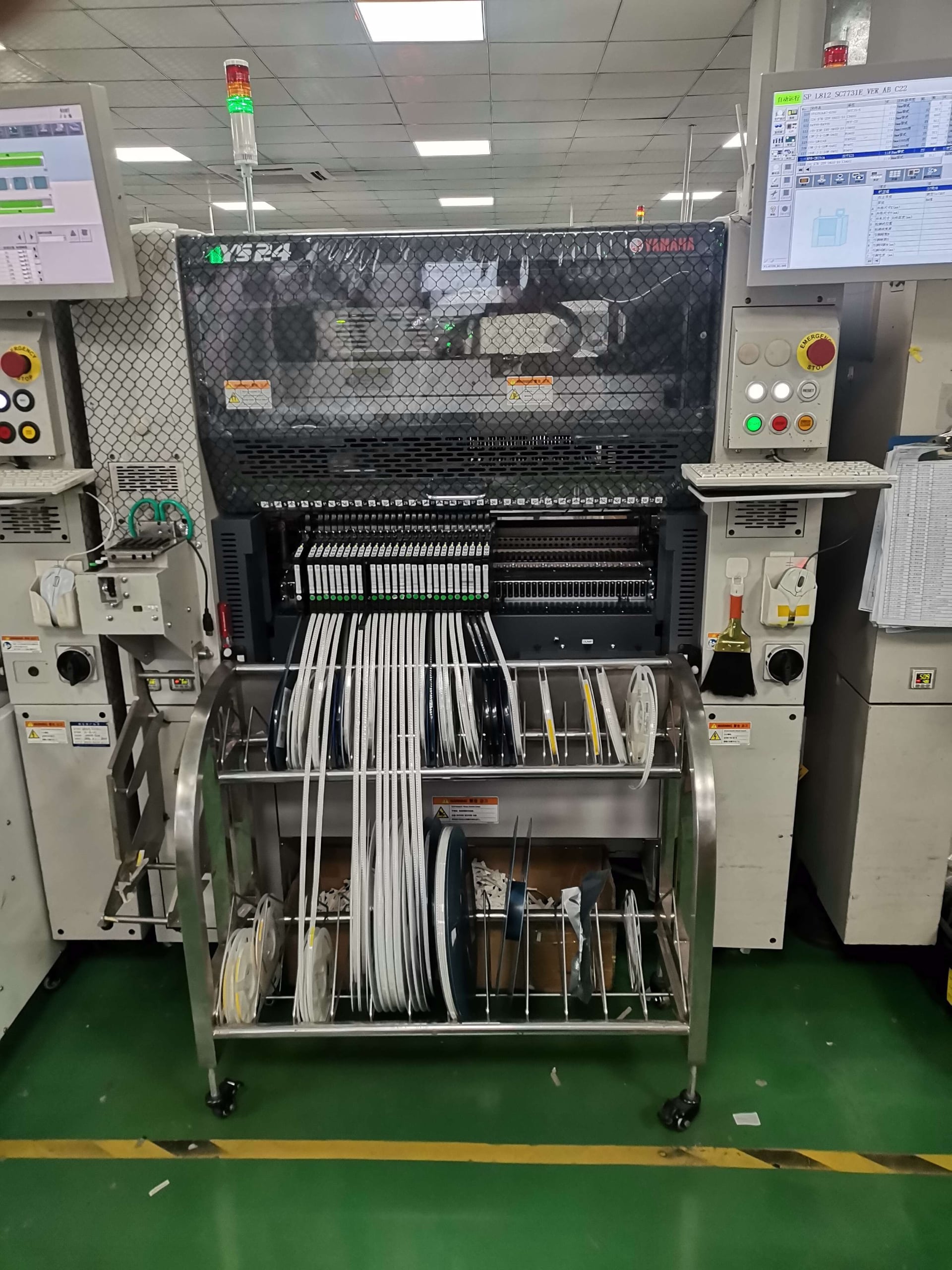
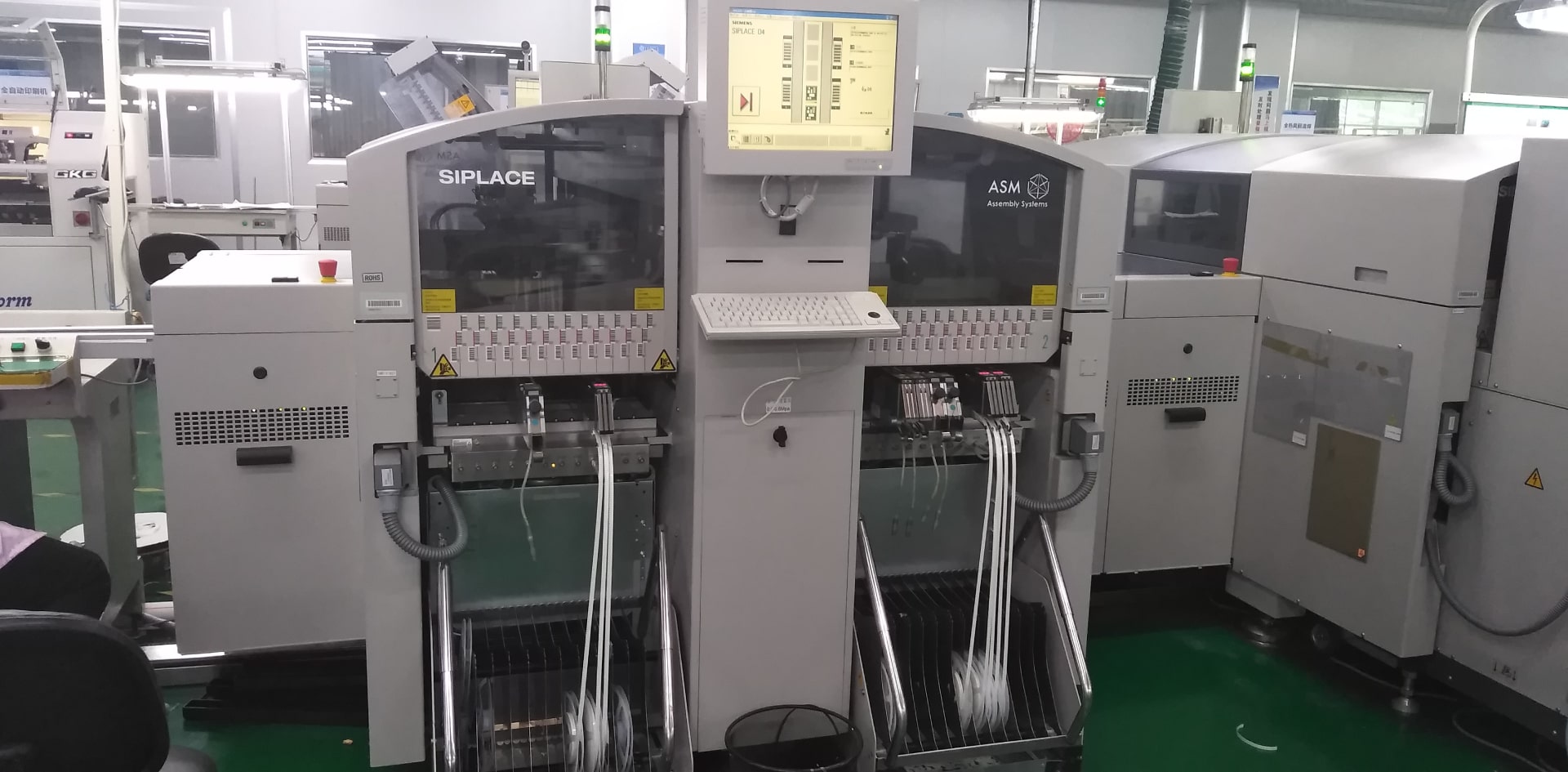
Take a Factory Tour!
OurPCB Shijiazhuang opened in 2007. Today, this factory spans over 6,000 meters in total, is equipped with 5 SIEMENS SMT lines, and has 200 employees. 90% of the business at our factory in Shijiazhuang is for advanced PCB assembly.
We went on to build our second factory in Shenzhen in 2017. This factory is about half the size of Shijiazhuang, but it boasts 7 YAMAHA SMT lines, X-ray, and AOI. It’s dedicated to standard assembly service and employs 110 people.
In 2014, we opened OurPCB in Melbourne, Australia, to provide services to our English-speaking customers across the world.

