PCB production involves using a variety of materials to suit different applications. Teflon is one of fabrication PCB's most popular substrates and laminate materials. This guide will explore why we value Teflon PCB so much. We will discuss the properties, advantages, and how we manufacture them. For pricing details, request an online PCB quote today.
Contents
- What is Teflon PCB?
- PCB Materials
- Properties and Advantages of Teflon PCBs
- Teflon PCB Manufacturing: Things You Must Know About
- 1. Preparing the Surface
- 2. Copper Cladding
- 3. Application of the Solder Mask
- 4. Drilling
- 5. Storage
- 6. Lamination
- Steps in The Production of Teflon PCB Prototype
- Applications of Teflon PCB
- Summary
What is Teflon PCB?
High-Frequency Rogers PCB
Source: Wikimedia Commons
As the name suggests, Teflon PCBs use Polytetrafluoroethylene(PTFE) as their base material. Furthermore, sometimes we may coat other PCB materials in PTFE to enhance it. People value Teflon for its flexibility and no-stick surface. Additionally, it has an inert molecular structure that makes it entirely non-reactive.
Furthermore, Teflon facilitates the construction of PCBs with improved capacities and heightened connections. It has a glass transition (Tg) as high as 280 °C. This factor is why we use it to build high-frequency printed circuit boards. Nevertheless, what other materials do we fabricate PCBs with, and how do they compare to Teflon/PTFE PCBs?
PCB Materials
PCB with various components
Besides Teflon, the most popular types of PCB substrate and laminate materials include:
- Glass-Reinforced Epoxy Laminate Material (FR-4, FR-5): PCB substrates and laminates are the most popular material. It has a Tg point of 135˚C. However, high glass transition versions are also available. These can be used in high-temperature situations with Tg points between 150 and 210˚C.
- Composite Epoxy Material (CEM-1, CEM-2, CEM-3): These materials comprise a mixture of a threaded glass fabric surface and a paper core that manufacturers combine with an epoxy resin. CE materials are particularly suitable for high-temperature uses. The Tg point for each subtype is as follows:
- CEM-1: 122˚C
- CEM-2: 125˚C
- CEM-3: 125˚C
- RF-35 (Organic-ceramic laminate material): Low-cost materials with incredible low loss factors and minimal water absorption rates. Additionally, they have extraordinary peel strength and incredible surface smoothness. They are a composite material that consists of reinforced glass based on threaded glass cloth. Additionally, they feature ceramic filling and glass fiber with a Teflon coating. Furthermore, they have a Tg of 315˚C, making them highly suitable for high-temperature applications.
- Polyamide: Much like Teflon, Polyimide materials are high-frequency PCB materials. We mainly use them to construct flexible PCBs. They have an excellent tolerance against high temperatures. They tend to have a Tg of above 300°C, making them more durable than Teflon or FR-4. Thus, this makes them highly suitable for microwave and high-frequency situations. However, they are costly to implement.
Other PCB materials include G-10 (high-pressure fiberglass laminate) and other metals and polyamides such as alumina and Kapton. However, the most common materials for rigid and rigid-flex boards are Teflon and FR-4.
Special Offer: Get $100 off your order!
Email [email protected] to get started!
Properties and Advantages of Teflon PCBs
The man standing behind an idealized version of AI in the form of a digital PCB
The main advantages of using Teflon for PCB fabrication include:
- Low coefficient of friction: Because Teflon has a non-stick and smooth surface, it has a low coefficient of friction.
- Low coefficient of thermal expansion: It has a Tg between 160 and 280˚C (sometimes more). As such, this fact is why we utilize Teflon in cookware. Furthermore, they're highly suitable for high-precision electronic devices that expand a lot of heat due to power consumption.
- Excellent chemical resistance: Teflon PCBs have extraordinary tolerance against chemicals. Thus, they are not easily eroded by moisture, grease, and other chemicals, which gives them incredible corrosion resistance.
- Low dissipation factor: Teflon's common dissipation factor makes it resistant to leaks and makes it exceptionally suitable for high-frequency and microwave applications. Additionally, this attribute gives them excellent weather resistance.
- Exceptional dielectric properties: Again, because of its low dissipation, Teflon has reduced dielectric loss. This attribute helps it keep a dielectric constant over high-frequency applications.
- High thermal stability: We can use Teflon in high-temperature applications to keep consistent form and property, despite these temperatures.
- Exceptional flame resistance: We use Teflon in commercial cooking applications because of its extraordinary resistance to fire and high temperatures. It's also incredibly conductive.
Additionally, PTFE PCBs have incredible mechanical rigidity. They are also durable; capable of withstanding sunlight and oxidation (rust) caused by moisture.
Teflon PCB Manufacturing: Things You Must Know About
Adding components to a PCB
To ensure the quality of the final PTFE PCB, manufacturers must pay careful attention to the fabrication process. We cannot handle PTFE the same way we take other materials such as FR-4. There are what you should know about Teflon PCB manufacturing:
1. Preparing the Surface
In this phase, the manufacturer must utilize sodium etchings. This process will enhance the bondability of the Teflon material. We perform this by soaking the material in a solution that consists mainly of sodium. Once this process is complete, we rinse the Teflon material using alcohol and H2O solution.
Additionally, they can use a process called plasma arc gasification. It prepares the surface for marking, metallization, and eventual layer shaping.
2. Copper Cladding
Copper plating is a nearly universal phase in PCB fabrication. This step involves preparing the copper surface, drilling the PTFE, and plating the through-holes. The manufacturer must use copper with high-tensile strength to prevent barrel cracks and lift pads.
3. Application of the Solder Mask
PCB Manufacturers must implement the solder mask in less than 12 hours after the etching process. The PCB manufacturer may ensure no residual moisture by baking the Teflon material in an oven before applying the solder mask.
4. Drilling
The manufacturer must use a drill with a high chip load to ensure that all fibers are removed and there is no Teflon tailing. This step ensures that the drilled holes are clean and precise.
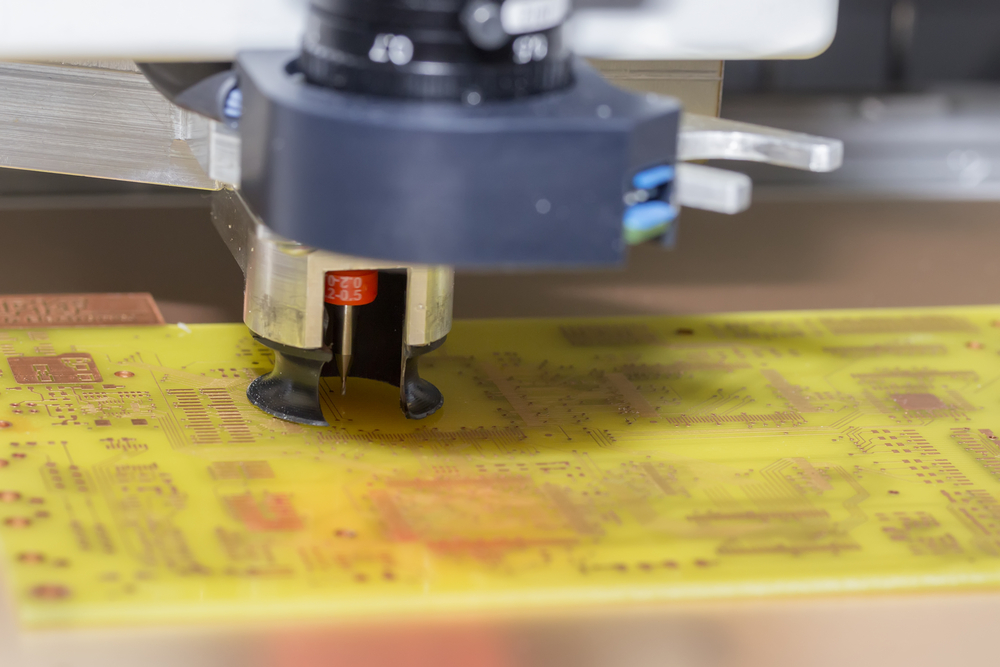
Preparing a printed circuit board
5. Storage
Teflon laminates are often soft and susceptible to tears and other damage. Thus, it would help if you handled them with the utmost care.
6. Lamination
We can perform the lamination of Teflon PCB materials at temperatures of up to 370 °C and pressures of 450-500 pounds per square inch (PSI). Moreover, we can perform lamination at these temperatures without using prepregs or bonding films.
However, some PCB manufacturers may use prepregs and bonding films with shallow melting points. Of course, this helps us reduce the temperature of the lamination process to 215 or 120 °C.
Furthermore, there are hybrid Teflon PCBs
that use a combination of Teflon and FR4. Nevertheless, these require oxide pretreatment before the final lamination process.
Steps in The Production of Teflon PCB Prototype
Printed Circuit board being treated
When we build the Teflon PCB prototype, we need to follow these proceeding steps:
- Design: The design of the PCB is carried out by stencil and PCB (CAD) design software. We need to understand the general layout of the prototype. It will eventually become the final Teflon PCB.
- Select the base material: Selecting the suitable material is one of the first fundamentals in PCB prototyping. The prototyping material does not have to be Teflon. Plastic is currently the most popular material for PCB prototyping flexible circuit boards.
- Design testing involves testing the design through simulation or constructing an initial prototype board. We use this step to verify that the connections and positioning of the final Teflon PCB components are correct.
- Troubleshooting and bug-zapping: This step involves addressing errors within the board's design, whether misplaced components or faulty connections. This step seeks to rectify bugs and ensure the final Teflon PCB is entirely error-free.
- Prototyping: This step involves constructing the prototype board.
- Testing the functionality: We then test the functionality of the prototype board to once again ensure that there are no bugs or errors. Once we're satisfied with the prototype board, we can manufacture the final PTFE PCB.
PCB testing
Applications of Teflon PCB
A high tech image of a PCB with a chip
Teflon PCBs have high density and durability. As such, we can use them in a wide range of applications such as:
- Medical devices
- Industrial Applications
- Power amplifiers
- Wi-Fi routers and antennas
- Mobile devices
- Printers
- Modern television sets and computer monitors
- Industrial technology and devices
- Radar systems
- Wireless base stations
Summary
In the above guide, we explored Teflon printed circuit boards. We expanded on how to prototype them and what we should consider during the fabrication process. Furthermore, we compared Teflon to other substrate and laminate materials. We hope that you've found this guide to be helpful. As always, thank you for reading.
Back to top: Teflon PCB
Special Offer: Get $100 off your order!
Email [email protected] to get started!