- PCB Manufacturer
- PCB Assembly Service
- Quick Turn
Quick Turn PCB Assembly Services
OurPCB delivers fast, high-quality PCB fabrication and assembly in 24 hours to 7 days, depending on design guidelines, board layers, order quantity, and surface finish. As a trusted PCBA manufacturer, we serve clients worldwide, especially in the USA, ensuring speed, precision, and reliability.





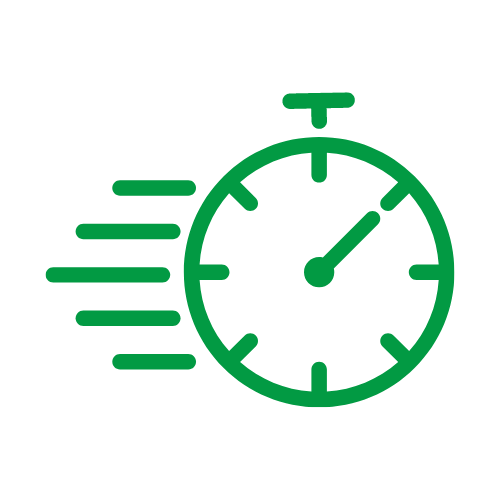





Below is the Estimated Turnaround Time for Standard PCB Orders
PCB Type | Layers | Quantity | Size | Estimated Turnaround |
---|---|---|---|---|
Single or Double Layer PCB | 1 | High | Medium | 1 – 2 days |
Single Layer PCB | 1 | High | Medium | 1 – 2 days |
Single or Double Layer PCB | 1 | High | Small | 1 – 2 days |
Flexible PCB | 2 | High | Very small, flexible | 1 – 2 days |
Single or Multi-Layer PCB | 2 | High | Large | 1 – 2 days |
Flexible PCB | 2 | High | Small, flexible | 3 – 4 days |
Double or Multi-Layer PCB | 2 | Moderate | Small | 1 – 2 days |
Flexible PCB | 2 | Low | Very small, flexible | 1 – 2 days |
Double or Multi-Layer PCB | 2 | Moderate | Small to medium | 1 – 2 days |
Multi-Layer PCB | 4 | High | Medium to large | 4 – 5 days |
Multi-Layer PCB | 4 | High | Small to medium | 4 – 5 days |
Multi-Layer or HDI PCB | 4 | Moderate | Small to medium | 3 – 4 days |
Multi-Layer PCB | 4 | Moderate | Medium | 3 – 4 days |
Multi-Layer PCB | 4 | Moderate | Small | 3 – 4 days |
Multi-Layer PCB | 6 | High | Small | 5 – 6 days |
Multi-Layer PCB | 6 | Moderate | Medium to large | 4 – 5 days |
Flexible or Rigid-Flex PCB | 6 | Moderate | Small to medium | 4 – 5 days |
Multi-Layer PCB | 6 | Moderate | Medium | 4 – 5 days |
Multi-Layer PCB | 6 | Moderate | Medium to large | 5 – 6 days |
Multi-Layer PCB | 8 | Low to moderate | Large | 6 – 7 days |
The estimated turnaround times provided in this table are for reference only and may vary based on design complexity, order quantity, and production capacity. For the most accurate and up-to-date lead times, please consult us directly.
PCB Manufacturing Process







What is the Quick Turn PCB Assembly Process?
The quick-turn PCB assembly process is a streamlined manufacturing workflow that starts with design and ends with the final product’s delivery.
The key aspect of quick turn PCB assembly is time. We cover both the fabrication and assembly processes in circuit board production, so you only need to handle the design process.
Here’s a breakdown of the key steps:
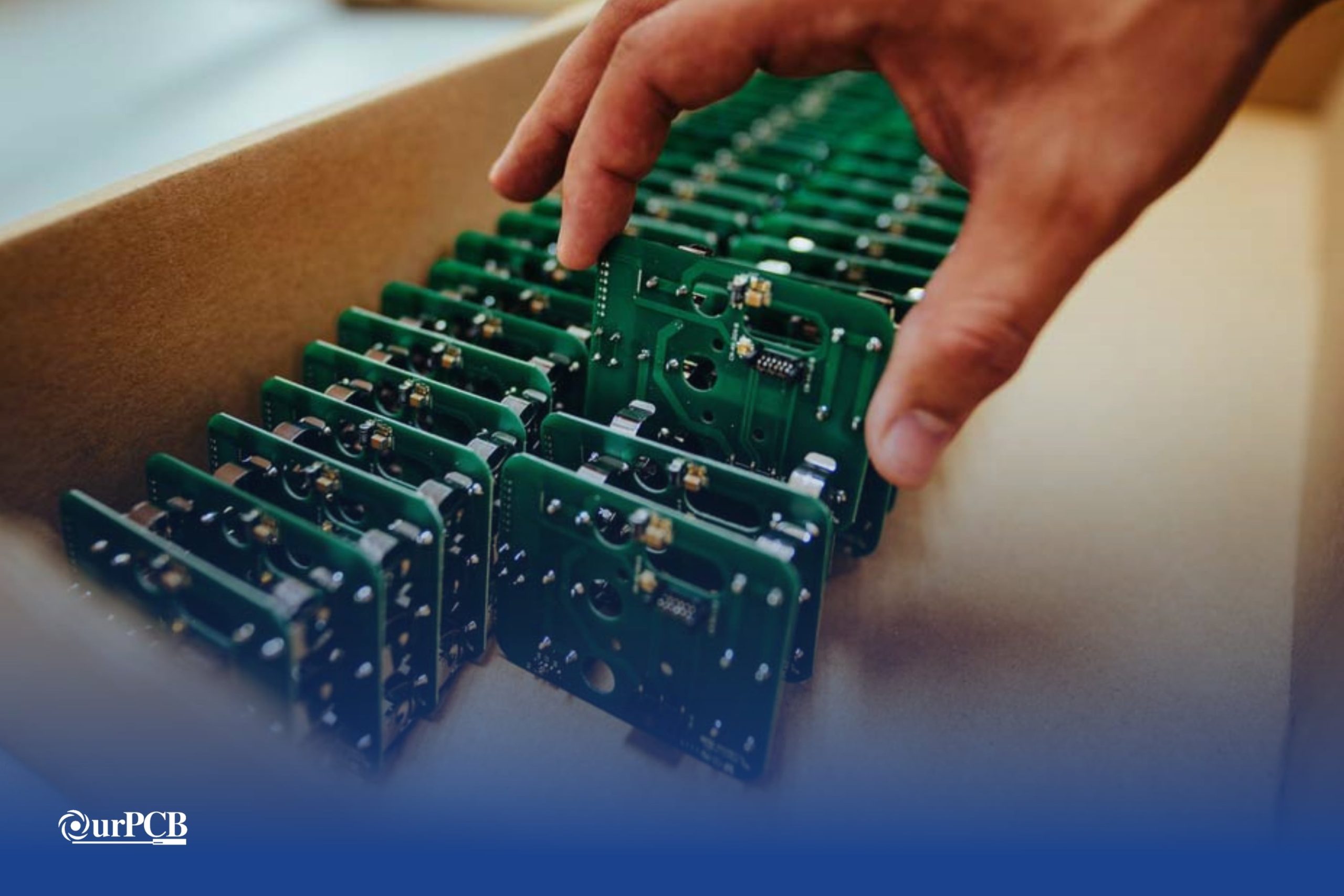




- OurPCB Technician analyzes a PCB design before approving it for production
- The process begins with PCB layout design, including defining electrical parameters, stack design, and component placement.
- Once finalized, essential design files (Gerber, Centroid, BOM, Pick-and-Place, NC Drill) are submitted for manufacturing.
- DFM (Design for Manufacturing) & DFA (Design for Assembly) checks ensure manufacturability by reviewing footprint design, component placement, solder mask clearances, and panelization.
- These checks help minimize defects, saving time and cost.

- Components are sourced using the BOM and secured from in-house inventory or reliable suppliers (Avnet, Arrow, Future Electronics).
- Customers can supply their own components or have them shipped directly to the assembly plant.

- Fabrication Steps: Printing PCB layout, etching, stack creation, hole drilling/plating, solder masking, silkscreen printing, and surface finishing.
- Rapid Prototyping Methods:
- Using simplified design rules.
- Prioritizing functional validation.
- Using simulated components.
- Running parallel prototype revisions.
- Multilayer boards require multiple etching/lamination cycles and additional inspection/testing for quality control.

- SMT Process:
- Solder paste applied via stencil.
- Components placed using pick-and-place machines.
- Reflow oven fuses components (210–250°C for lead-free solder).
- Inspection & testing (AOI, X-ray, Flying Probe, Bed of Nails).
- Through-Hole Assembly:
- Automated insertion mount machines insert components.
- Wave soldering ensures solid connections.
- Final testing & functional checks follow, ensuring assembly accuracy before shipment.

Testing Methods Include:
- In-Circuit Testing (ICT): Automated testing via spring-loaded pins.
- Flying Probe Testing: Precision mobile probes check connectivity.
- Burn-in Testing: Extreme stress tests for reliability.
- Functional Testing: Simulates real-world operational conditions.
- Other tests include aging, fatigue, and environmental stress testing.

- Prototype boards are securely packaged in antistatic bags with ziplock or vacuum sealing and desiccant packets for moisture control.
- Customers can choose between expedited or standard shipping based on urgency and cost preferences.
What are the Benefits of Quick Turn PCB Assembly?
The primary benefit of quick-turn PCB assembly is the accelerated time to market for your products. But it has some secondary benefits:
DFM is crucial before quick-turn PCB assembly, ensuring the design aligns with the manufacturer’s capabilities. This includes using cost-effective materials and reducing errors that may be expensive to fix later. DFA further lowers costs by optimizing the layout, reducing parts, and simplifying assembly.
Quick-turn PCB assembly accelerates product development by allowing multiple iterations to refine the design. This process enables quick feature enhancements, keeping your product ahead of the competition while reducing time to market.
Since the process mirrors prototyping, defects in design or manufacturing are detected early and resolved within the production timeline. Early identification prevents costly revisions and ensures a smooth, efficient assembly process.



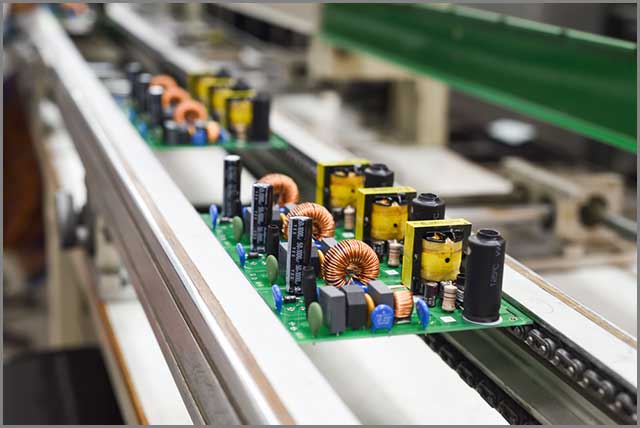



PCB Assembly Services

We handle everything from parts sourcing to final assembly, providing a hassle-free experience that ensures top-quality boards every time.

Whether you need a few prototypes or large-volume batches, our flexible assembly services adapt to your project’s scope and timeline.

Stay environmentally responsible with our compliant assembly processes, offering RoHS and lead-free options for safe, reliable builds.

No matter the complexity, we can assemble boards of all configurations—single-layer, multi-layer, or a mix—to match your exact specifications.

From one-off prototypes to bulk orders, we accommodate projects of all sizes without compromising on quality or turnaround time.

Join our growing community of satisfied clients who rely on our dependable assembly expertise and dedicated customer support.
Millions of business and innovators use OurPCB
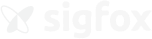
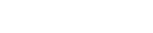
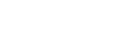


PCB Board Process
Order Received
- Component Procurement
- Preparation
- PCB Manufacture
- Make Process Flow
Soldering
- Solder Printing/Wave Soldering
- SMT/Plugging
- Inspection (repair if necessary)
- AOI (repair if necessary)
- Transfer
Parts Assembly
- Manual Assembly
- Cleaning
- Wire Screw
- Inspection
- Repair If Necessary
Finalization
- Final Confirmation
- Packing
- Shiping
Technical Capabilities
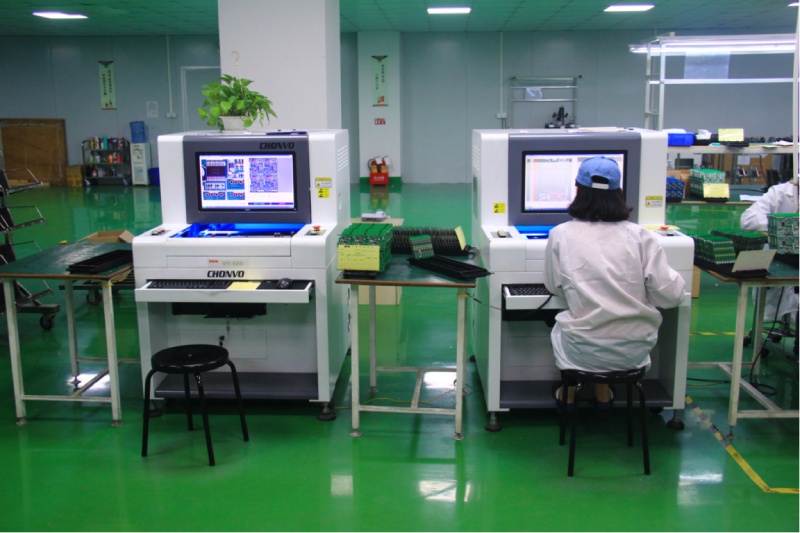



Capabilities & Services
- One-stop PCBA Services (PCB Manufacturing + Components Sourcing + Assembly)
- SMT Assembly + THT Assembly
- BGA Rework
- 60,000 Chips/Hour
- Down to 01005/0210 Size
- Accuracy<±40μm
- Min. QFN Pin Width/Space: 0.15mm/0.25mm
- Min. BGA Diameter/Space: 0.2mm/0.35mm
- Rigid, Flex, HDI, & High-speed Power Boards
- Up to 50 Layers
- 60GHz High Frequencies
- Min. Trace Width/Spacing: 2.5mil/2.5mil
- AOI, X-ray, ICT & FCT Testing
- Controlled Impedance
- ISO 9001, ISO 13485, ISO 14001, IATF 16949, IPC-A-610, UL Certified
- Automotive, Medical, & Military-grade PCBA Manufacturing


Mon-Fri: 24 hours,
Sat: 9am-6pm, GMT+8

Reach us at
[email protected]
24 hours online

+86-199-30589219
Mon-Fri: 24 hours,
Sat: 9am-6pm, GMT+8
FAQ's
What are the Quick Turn PCB Assembly Capabilities?
Our quick-turn PCB assembly capabilities include delivering rigid, flexible, and rigid-flex circuit boards in this short timeline. We can make these bendable boards compact and resistant to heat and vibrations as well.
Our team of expert technicians and engineers can also build quick-turn miniature circuit boards for the modern compact devices used in IoT and communications equipment.
Regardless of the size or rigidity, these boards will have a high tensile strength to maximize durability and enhanced heat dissipation to keep the components at their optimal performance range. Some of the techniques we can use to improve heat dissipation include installing heat sinks and enhancing airflow above and below the PCBA.
How to Choose a Quick Turn PCB Assembly Partner
When choosing a quick-turn PCB assembly partner, we recommend checking these five factors:
- Professionalism: Look for a professional partner who will deliver reliable, tested and certified boards in the shortest time possible.
- High Operational Capacity: Choose a partner with a high operational capacity who can deliver low, medium, or high quantity orders within the 7-day limit. This partner should demonstrate flexibility to adjust the manufacturing and assembly processes to meet your demands.
- Manufacturing/Assembly Equipment: Quick manufacturing and assembly ultimately relies on the installed equipment. Our production facilities have the latest Siemens and Yamaha SMT lines, as well as other equipment for manufacturing and testing the complete boards.
- Keeping up to Date: Your quick-turn PCB assembly partner should have more than manufacturing and assembly equipment. Technology changes rapidly, so your partner should have the latest equipment to be able to build you the most advanced PCBs possible.
- Design Assistance: Producing quick-turn PCBs requires regular engagement and assistance during the design phase to ensure the layout that goes to manufacturing is error-free. Your partner should assist you in this process to streamline the DFM, DFA, and even DRC.
What are the Challenges and Limitations of Quick Turn PCB Assembly?
Quick-turn PCB assembly isn’t without its challenges and limitations. Although the DFM and DFA processes help to cut costs, the expedited manufacturing, assembly, and shipping processes will increase the overall production costs.
Component availability can also be challenging due to the quick nature of this process. Consignments and partial assembly options can eliminate this issue, especially for the unique, hard-to-find parts.
Lastly, although the process includes quality control measures, they might not be as stringent as the ones implemented in regular PCB production. Fab houses have to do the tests quickly to deliver within the stipulated timelines, which can affect quality.
Why Choose OurPCB?
OurPCB is the leading electronics manufacturer in China that specializes in PCB manufacturing, assembly, quick turn PCB assembly, and electronics design. We have an extensive list of clients including Intel, Sigfox, Great Wall, and Bewatec – testaments to our abilities as a professional PCB fab house you can rely on for customized, efficient services. We’re also ISO:9001 certified, so high-quality products are guaranteed.