Sheet Metal Fabrication Services
✅ Versatile Applications: Used in industries like automotive, aerospace, and construction for various components.
✅ Precision Cutting: Techniques like laser cutting ensure high accuracy and clean edges.
✅ Custom Shapes: Capable of creating complex designs tailored to specific project requirements.
✅ Material Variety: Works with metals such as aluminum, steel, and copper, offering diverse options.
✅ Cost-Effective Production: Efficient processes reduce waste and lower manufacturing costs.
✅ Strength and Durability: Produces robust components suitable for demanding environments.
✅ Rapid Prototyping: Enables quick development of prototypes for testing and validation.





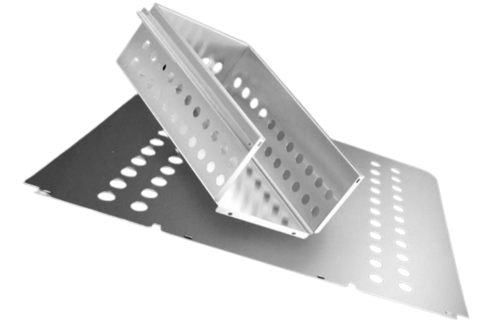





Looking for Sheet Metal Fabrication Services for Your Manufacturing Needs?
Are you searching for a world-class sheet metal fabrication service provider? OurPCB specializes in delivering high-precision sheet metal fabrication with a focus on quality, efficiency, and customer satisfaction. As a premier sheet metal fabrication partner trusted by industry leaders across the United States, we deliver precision-engineered solutions that drive innovation and efficiency in American manufacturing.
Get in touch with us today for a customized quote or consultation. We look forward to working with you!
How Much Do Sheet Metal Fabrication Services Cost?
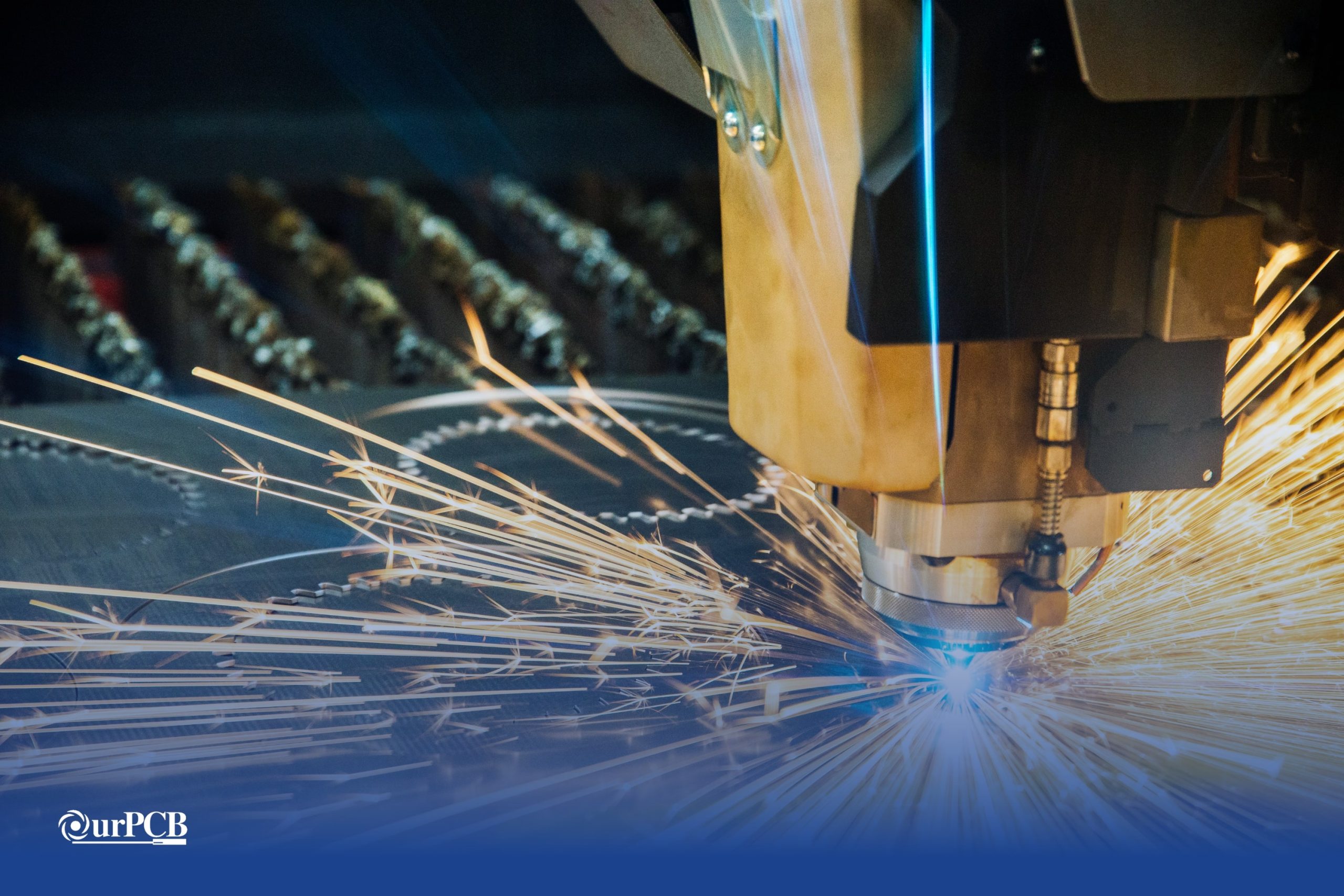



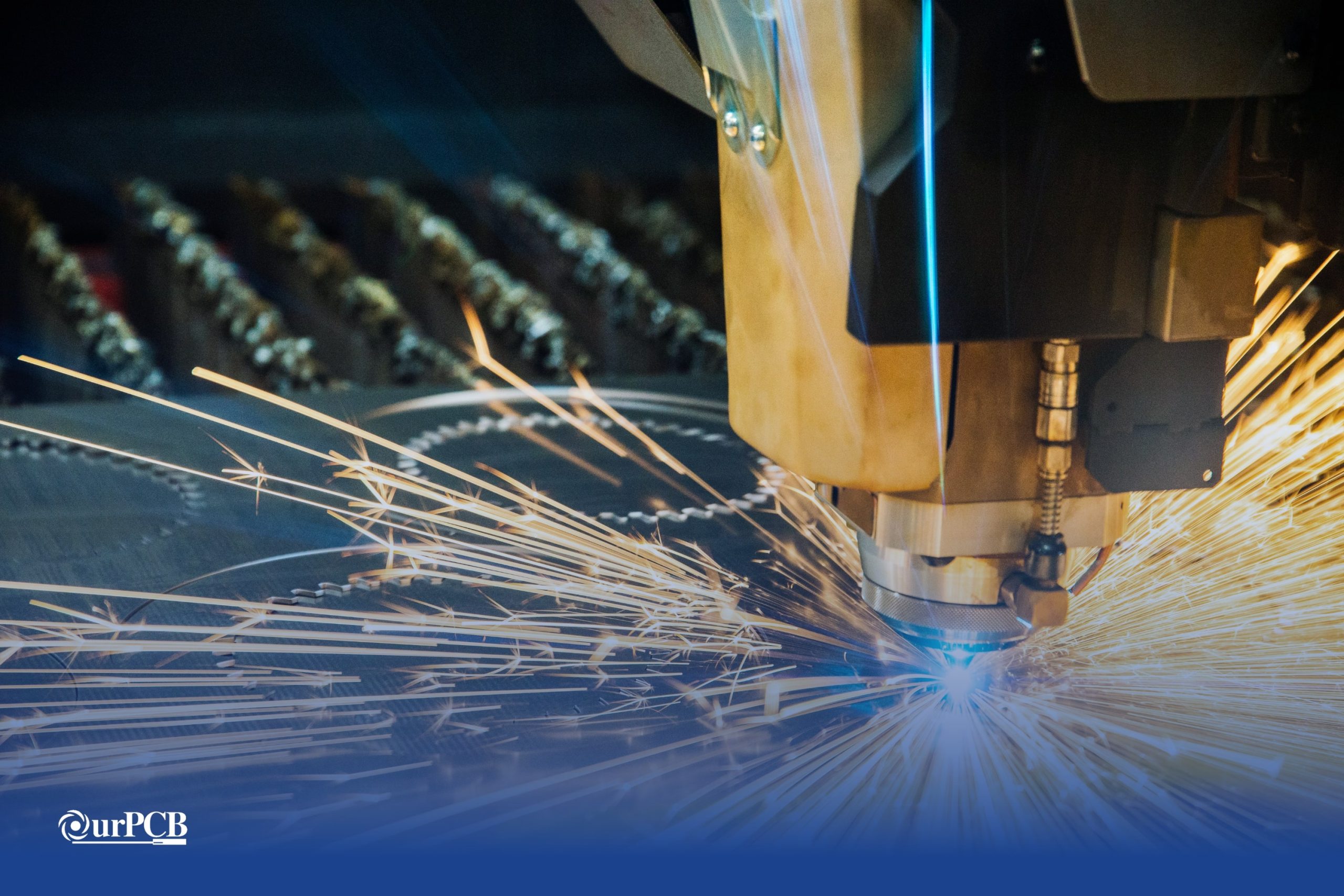



The cost of sheet metal fabrication can vary widely, but generally falls within the range of $25 to $150 per hour for labor. However, the total cost will depend on several factors, such as the complexity of the design, the type and thickness of the metal used, the quantity of parts needed, the required finishing processes, and the turnaround time. Simple projects may cost a few hundred dollars, while more complex, large-scale fabrications can run into thousands of dollars.
Note: For exact prices, contact OurPCB directly. Our team will look at your project needs and give you a clear quote. Costs change based on what you need and current market prices. We offer fair pricing for all sheet metal fabrication projects. Get in touch with us today to discuss your needs.
How the Sheet Metal Fabrication Process Works
The typical sheet metal fabrication process includes these sub-processes:
The design is typically done using CAD software or by hand while considering product dimensions, tolerances, and sheet metal material
Sheets are generally cut using lasers, but other processes use plasma or water jets.
Also known as CNC folding, this process can be completed using automated panel bending or manual press brake machines.
This step deforms the sheet to the required shape without cutting.
Welding joins all the fabricated metal parts to form the final product.
Finishing involves preparing the metal sheets for maximum durability, such as by adding an extra layer of durability (powder coating, polishing, electroplating, etc.).
Assembling the final product involves adding the required products before packaging and delivery.



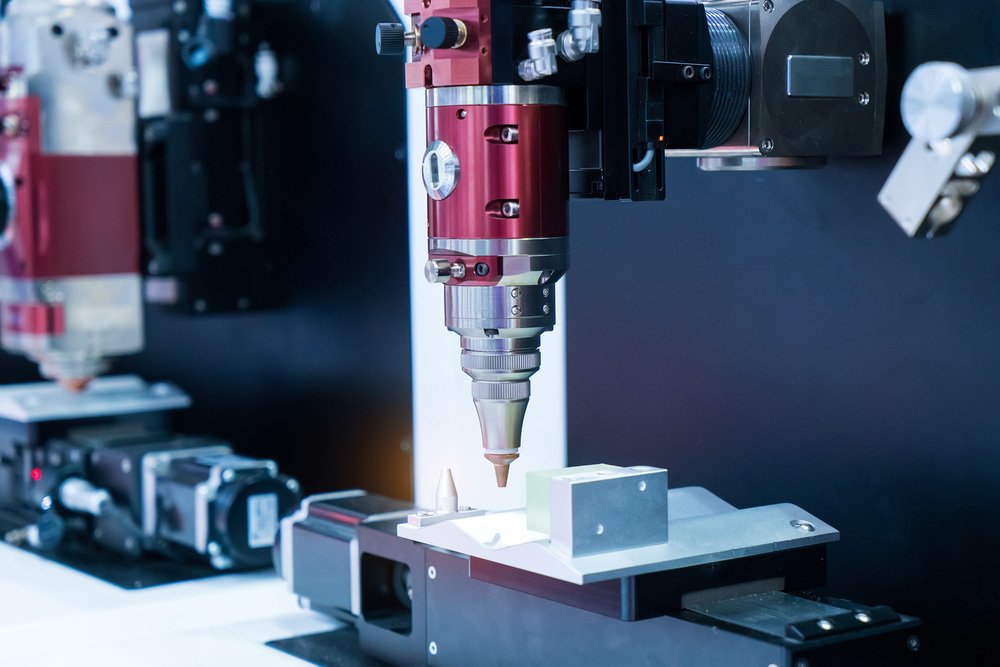



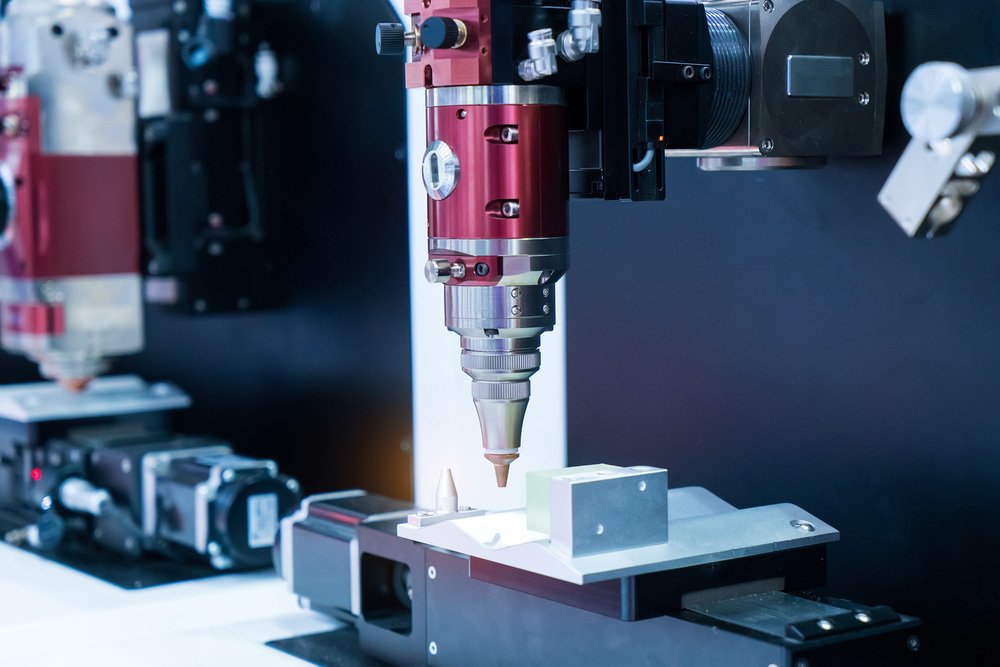
- 15+ Years of Experience
Our team has extensive experience creating both standard and custom wiring harnesses.
- Competitive Pricing
Well-priced and payable via PayPal, bank transfer, Western Union, or Moneygram.
Major Types of Sheet Metal
Sheet metal comes in various types including aluminum, carbon steel, copper, stainless steel, and titanium, each offering different properties like strength-to-weight ratios, conductivity, and corrosion resistance that make them suitable for specific applications ranging from automotive parts to kitchen equipment.
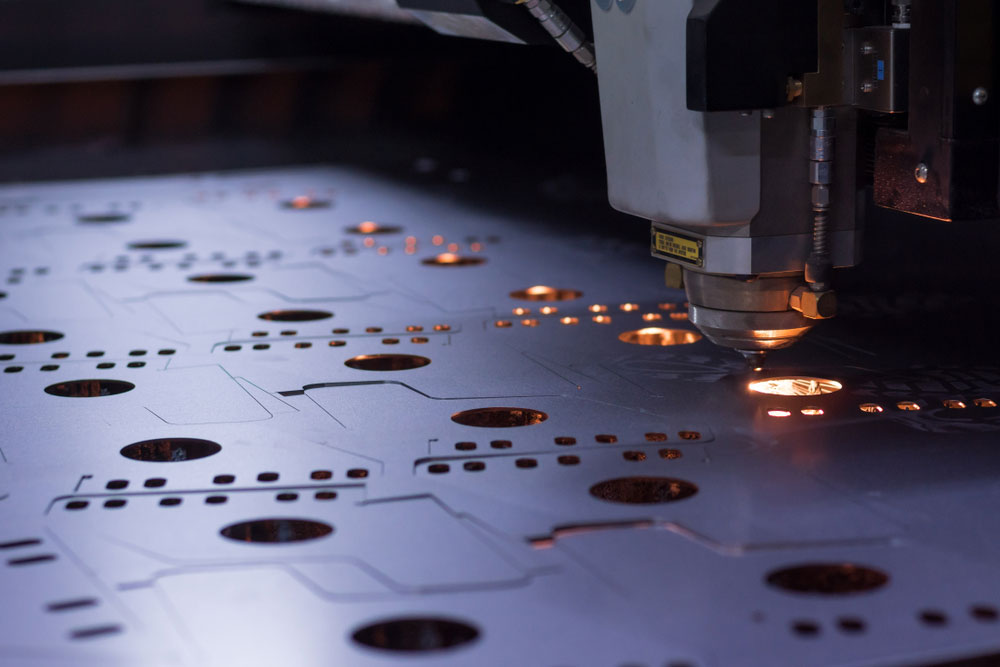



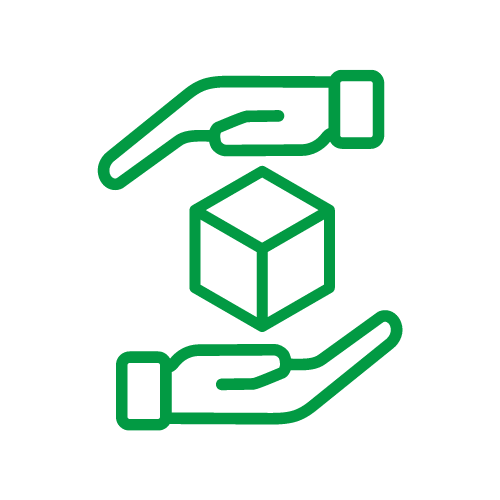
Only ROHS-compliant materials
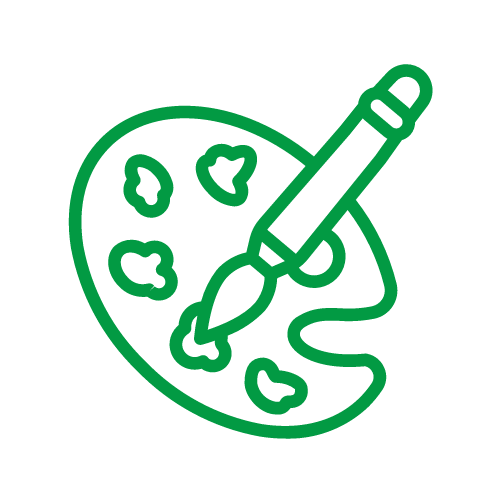
Orange or OEM color
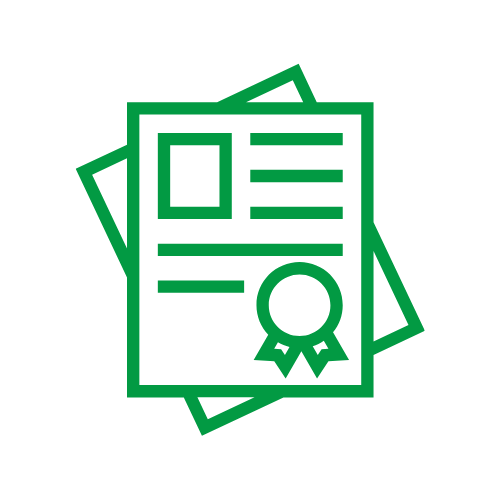
TUV, ISO9001, T/S16949, ROHS-approved
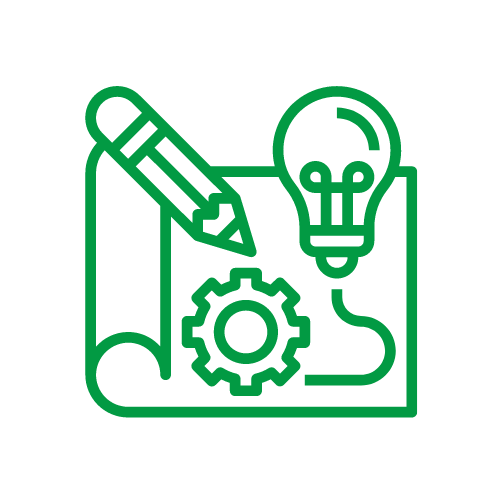
Prototypes can be provided for assessment
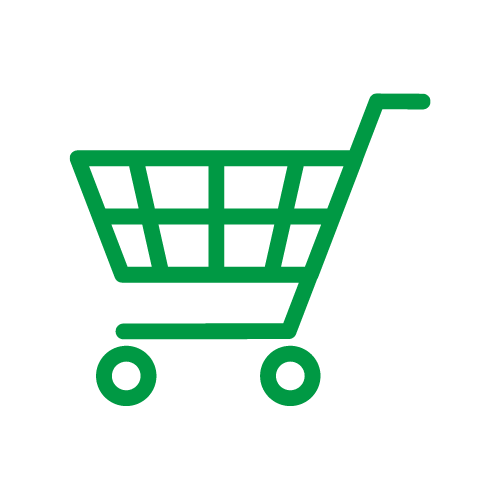
Small quantities accepted
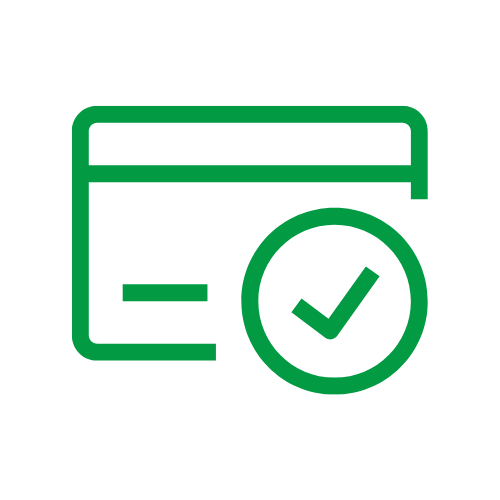
100% TT or PayPal for convenience
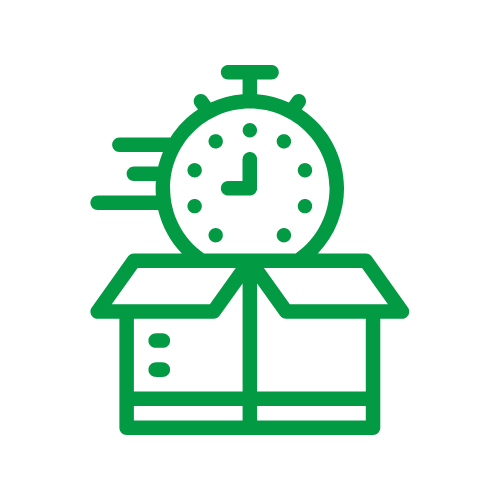
As fast as possible based on production capacity
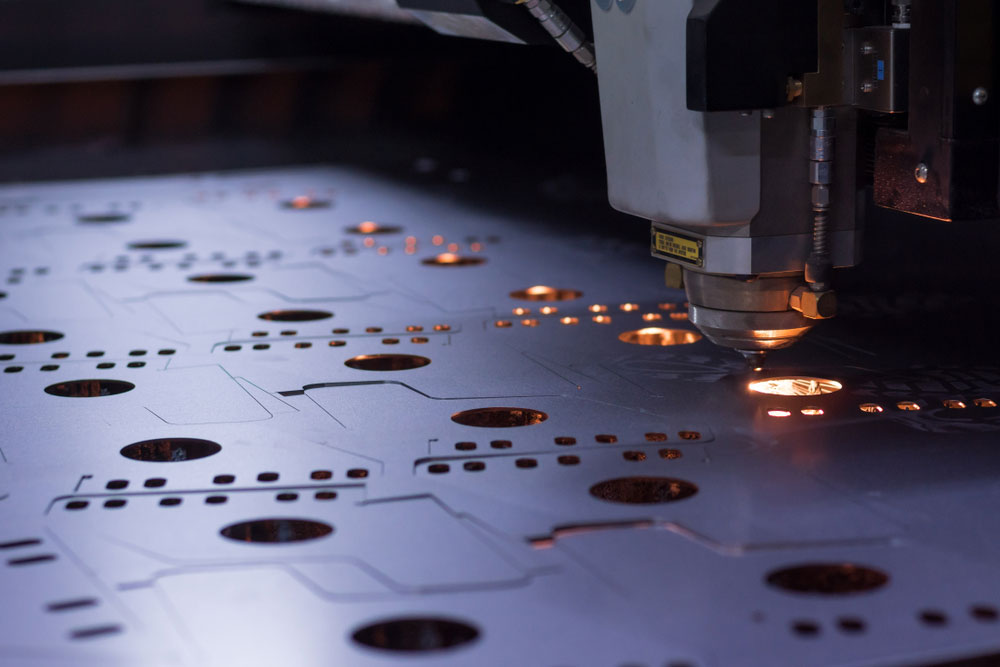



- Aluminum: This metal offers a good strength-to-weight ratio, making it suitable for automotive and aerospace or aviation parts fabrication. It is also highly conductive, so cooking vessels and electrical devices use this metal.
- Carbon Steel: Steel alloyed with carbon results in a strong and hardened metal when they are treated with heat.
- Aluminized Steel: With aluminum’s superb corrosion resistance properties and carbon steel’s high strength, these metal sheets are ideal for cooking appliances and other products operating at high temperatures.
- Copper: Although costlier than aluminum, copper is more thermally and electrically conductive. Its sheets can be used to make roofs, sinks, and doors.
- Galvanized Steel: This metal comprises steel-coated zinc to improve corrosion resistance and is more common in water pipes.
- High-Strength Steel: With steel metal sheets as the base, high strength steel is alloyed with several elements, such as manganese, carbon, and copper to enhance its hardness.
- Stainless Steel: Stainless steel is commonly used to make kitchen equipment because it is easily manufactured. Moreover, stainless steel is corrosion, heat, and fire-resistant, and has a high strength-to-weight ratio.
- Titanium: Titanium is also corrosion resistant and has a high-to-weight ratio, making it prevalent in medical and aviation components.
Our Sheet Metal Fabrication Capabilities

Processing Accuracy: ±0.05mm/100mm
Materials: The thickness varies with different materials, typically carbon steel plate ≤12mm, stainless steel plate ≤10mm, and non-metallic materials ≤20mm.

Processing Accuracy: ±0.05mm/100mm
Materials: Aluminum and steel.

Processing Accuracy: ±0.02mm/100mm
Materials: Cold-rolled sheet (SPCC), hot-rolled sheet (SHCC), galvanized sheet (SECC, SGCC), copper (CU), aluminum sheet (6061, 5052, 1010, 1060, 6063, hard aluminum, etc.)
Millions of business and innovators use OurPCB
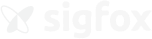
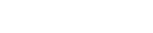
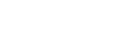


Applications of Sheet Metal Fabrication
Body panels (doors, hoods, fenders, roofs), structural components (chassis parts, frame elements), interior components (dashboard structures, seat frames), exhaust systems (mufflers, catalytic converter housings)
Fuselage panels, wing and tail assemblies, interior cabin components, fuel tanks, hydraulic systems
Roofing materials (metal roofs, gutters, downspouts), HVAC systems (ductwork, vents), structural elements (steel framing, support beams), decorative elements (facades, panels, architectural details)
Computer and server enclosures, smartphone and tablet casings, home appliances (refrigerators, washing machines), industrial equipment housings
Solar panel frames, wind turbine components, oil and gas equipment (tanks, pipes, valves), power generation equipment housings
Medical device casings, hospital furniture (beds, cabinets, trolleys), surgical instruments, laboratory equipment housings
Food processing equipment, commercial kitchen appliances, beverage cans, storage tanks, silos
Cell tower components, antenna housings, equipment racks, satellite dishes
Railway car bodies, shipbuilding components (hull plates, structural elements), bus and truck body panels
Metal cabinets, office furniture (desks, filing cabinets), decorative metal furniture, retail display fixtures
Billboard structures, illuminated signs, directional signage, trade show displays
Armored vehicle components, weapon systems housings, military equipment containers, naval vessel components
Cookware, tools, lighting fixtures, outdoor equipment (grills, fire pits)
Machine guards, conveyor systems, industrial robots, packaging machinery
Sheet Metal Fabrication: Advantages and Disadvantages
Advantages
- Enables lightweight parts manufacturing
- Can process a wide variety of metal materials with different properties
- Multiple processing techniques
- Provides high efficiency and accuracy in fabrication, especially when using laser cutters
- Outputs are sturdy and durable (thin sheet metal can be engineered to be structurally strong)
- Can be used for a wide range of projects that require small, medium, or large metal sheet pieces
- Cost-effective sheet metal component manufacturing process
- Sheet metal is highly recyclable, making the process eco-friendly
Disadvantages
- Expensive tooling materials and equipment, especially if custom-made
- Each fabrication technique has its limits
- Tight bending is only limited to thin metal sheets
- The fabricated products can be boxy and appear rudimentary
- Metal needs processing after fabrication, which can increase overall costs
Why Choose Us as Your Sheet Metal Fabrication Service Provider?
Our one-stop prototype and product processing services employ advanced CNC machining, 3D printing, silicone molding, rapid molding, injection molding, sheet metal processing, along with numerous surface treatment technologies. We combine numerous processes to ensure precise and accurate results.
As your best sheet metal fabrication service provider, our professional team guarantees quick quotations and real-time tracking of order status.
OurPCB has a robust quality control system and has received several certifications, including ISO 9001, ISO 14001, IATF 16949, and ISO 27001. We aim to be your go-to Sheet Metal Fabrication company by providing excellent service, affordable prices, and exceptional products.


Mon-Fri: 24 hours,
Sat: 9am-6pm, GMT+8

Reach us at
[email protected]
24 hours online

+86-199-30589219
Mon-Fri: 24 hours,
Sat: 9am-6pm, GMT+8
FAQ's
What is Sheet Metal Fabrication?
Sheet metal fabrication is a manufacturing process that uses flat metal sheets to make different products. This process is compatible with various metal materials, such as aluminum, copper, brass, and zinc, and you can fabricate the flat sheet by forming, bending, cutting, folding, punching, stretching, and assembling. In addition, this technique is often used in the production of parts for PCB assembly manufacturers, as it allows for precise and customizable components that meet specific electronic needs.
How does OurPCB address environmental sustainability in sheet metal fabrication?
We use energy-efficient machinery, renewable energy, and waste recycling programs to minimize environmental impact. We also maintain ISO 14001 certification and implement eco-friendly alternatives in our processes.
What are your typical lead times for sheet metal fabrication projects?
Lead times range from 24 hours for simple components to several weeks for complex projects. The timeline depends on design, material, and process complexity. We provide estimated lead times during the quotation process and offer expedited services when needed.