- PCB Manufacturer
- PCB Assembly Service
- Injection Molding Service
Injection Molding Service - Printed Circuit Board Assembly Services
- Custom Prototyping: Rapid turnaround for custom plastic prototypes.
- Cost-Effective Production: Economical for high-volume production of identical plastic parts.
- Material Variety: Supports diverse materials, including thermoplastics and elastomers.
- Quality Assurance: Offers inspection and certification for compliance with industry standards.
- Diverse Applications: Serves multiple industries, including medical, automotive, and consumer products.


What is Injection Molding?
Injection molding is a manufacturing process that mass-produces thousands of identical plastic components. It involves injecting the molten material (usually thermoplastic and thermosetting polymers) into a mold fitted into the machine.
These molds are precision-machined to match the shape of the final product. They also have cooling lines that reduce the solidification time by circulating water or oil from an external temperature controller after material injection.
Besides plastics, the process can make metal (die-casting), glass, confections, and elastomer parts, which can also be utilized by PCB manufacturing companies for creating various electronic components.
Looking for Injection Molding Services for Your Manufacturing Needs?
Are you searching for a world-class injection molding service provider? OurPCB specializes in delivering high-precision injection molding with a focus on quality, efficiency, and customer satisfaction. As a premier injection molding partner trusted by industry leaders across the United States, we deliver precision-engineered solutions that drive innovation and cost-effectiveness in American manufacturing.
With a focus on client satisfaction, premium products, and competitive pricing, we are committed to meeting all your injection molding needs. Contact us today for an accurate quote or consultation—we look forward to working with you on your next project.
- PCB Assembly Services: Comprehensive solutions for assembling printed circuit boards.
- Quick Turn PCB Assembly: Fast and efficient PCB assembly to meet tight deadlines.
- High Volume PCB Assembly: Scalable solutions for large-scale PCB production.
- Flexible PCB Manufacturer: Specialized in manufacturing flexible PCBs for diverse applications.
- Low Volume PCB Assembly: Cost-effective solutions for small batch PCB assembly.
- Turnkey PCB Assembly: End-to-end services covering all aspects of PCB production.
- PCB Design Services: Expert design services to bring your PCB concepts to life.
- Rigid-Flex PCB Manufacturer: Manufacturing robust and versatile rigid-flex PCBs.
- PCB Prototype: Rapid prototyping services to test and refine your PCB designs.
- Rogers PCB: High-frequency PCBs ideal for RF and microwave applications.
- Aluminum PCB: PCBs with excellent heat dissipation properties, perfect for high-power devices.
- Metal Core PCB: Thermal PCBs with metal bases for effective heat management.
- High Tg PCB: High glass transition temperature PCBs for improved thermal performance.
- High Frequency PCB: Designed for high-speed and high-frequency applications, ensuring superior signal integrity.
- Heavy Copper PCB: Built with thicker copper layers for high current and enhanced thermal management.
- HDI PCB: High Density Interconnect PCBs offering advanced circuitry in a compact design for complex applications.
- PCB Assembly Services: Comprehensive solutions for assembling printed circuit boards.
- Quick Turn PCB Assembly: Fast and efficient PCB assembly to meet tight deadlines.
- High Volume PCB Assembly: Scalable solutions for large-scale PCB production.
- Flexible PCB Manufacturer: Specialized in manufacturing flexible PCBs for diverse applications.
- Low Volume PCB Assembly: Cost-effective solutions for small batch PCB assembly.
- Turnkey PCB Assembly: End-to-end services covering all aspects of PCB production.
- PCB Design Services: Expert design services to bring your PCB concepts to life.
- Rigid-Flex PCB Manufacturer: Manufacturing robust and versatile rigid-flex PCBs.
- PCB Prototype: Rapid prototyping services to test and refine your PCB designs.
- Rogers PCB: High-frequency PCBs ideal for RF and microwave applications.
- Aluminum PCB: PCBs with excellent heat dissipation properties, perfect for high-power devices.
- Metal Core PCB: Thermal PCBs with metal bases for effective heat management.
- High Tg PCB: High glass transition temperature PCBs for improved thermal performance.
- High Frequency PCB: Designed for high-speed and high-frequency applications, ensuring superior signal integrity.
- Heavy Copper PCB: Built with thicker copper layers for high current and enhanced thermal management.
- HDI PCB: High Density Interconnect PCBs offering advanced circuitry in a compact design for complex applications.
- PCB Assembly Services: Comprehensive solutions for assembling printed circuit boards.
- Quick Turn PCB Assembly: Fast and efficient PCB assembly to meet tight deadlines.
- High Volume PCB Assembly: Scalable solutions for large-scale PCB production.
- Flexible PCB Manufacturer: Specialized in manufacturing flexible PCBs for diverse applications.
- Low Volume PCB Assembly: Cost-effective solutions for small batch PCB assembly.
- Turnkey PCB Assembly: End-to-end services covering all aspects of PCB production.
- PCB Design Services: Expert design services to bring your PCB concepts to life.
- Rigid-Flex PCB Manufacturer: Manufacturing robust and versatile rigid-flex PCBs.
- PCB Prototype: Rapid prototyping services to test and refine your PCB designs.
- Rogers PCB: High-frequency PCBs ideal for RF and microwave applications.
- Aluminum PCB: PCBs with excellent heat dissipation properties, perfect for high-power devices.
- Metal Core PCB: Thermal PCBs with metal bases for effective heat management.
- High Tg PCB: High glass transition temperature PCBs for improved thermal performance.
- High Frequency PCB: Designed for high-speed and high-frequency applications, ensuring superior signal integrity.
- Heavy Copper PCB: Built with thicker copper layers for high current and enhanced thermal management.
- HDI PCB: High Density Interconnect PCBs offering advanced circuitry in a compact design for complex applications.
- PCB Assembly Services: Comprehensive solutions for assembling printed circuit boards.
- Quick Turn PCB Assembly: Fast and efficient PCB assembly to meet tight deadlines.
- High Volume PCB Assembly: Scalable solutions for large-scale PCB production.
- Flexible PCB Manufacturer: Specialized in manufacturing flexible PCBs for diverse applications.
- Low Volume PCB Assembly: Cost-effective solutions for small batch PCB assembly.
- Turnkey PCB Assembly: End-to-end services covering all aspects of PCB production.
- PCB Design Services: Expert design services to bring your PCB concepts to life.
- Rigid-Flex PCB Manufacturer: Manufacturing robust and versatile rigid-flex PCBs.
- PCB Prototype: Rapid prototyping services to test and refine your PCB designs.
- Rogers PCB: High-frequency PCBs ideal for RF and microwave applications.
- Aluminum PCB: PCBs with excellent heat dissipation properties, perfect for high-power devices.
- Metal Core PCB: Thermal PCBs with metal bases for effective heat management.
- High Tg PCB: High glass transition temperature PCBs for improved thermal performance.
- High Frequency PCB: Designed for high-speed and high-frequency applications, ensuring superior signal integrity.
- Heavy Copper PCB: Built with thicker copper layers for high current and enhanced thermal management.
- HDI PCB: High Density Interconnect PCBs offering advanced circuitry in a compact design for complex applications.
How Much Do Injection Molding Services Cost?
The cost of injection molding services typically depends on several key factors: the complexity and size of the part, the material used, the production volume, and the mold (tool) cost. Mold costs can range from $1,000 for simple designs to over $100,000 for complex, multi-cavity molds. Material costs vary widely, from $1-$3 per pound for common plastics to $30+ per pound for specialized engineering plastics. Machine time and labor also contribute to the overall cost.
For high-volume production, the per-unit cost decreases significantly as the mold cost is spread over more parts. While initial tooling costs can be high, injection molding becomes more cost-effective for large production runs, often resulting in lower per-unit costs compared to other manufacturing methods.
Note* For exact prices, contact OurPCB directly. Our team will look at your project needs and give you a clear quote. Costs change based on what you need and current market prices. We offer fair pricing for all injection molding projects. Get in touch with us today to discuss your needs.
How Injection Molding Works?
Let’s break down the process step by step for a comprehensive understanding.
1. Material Preparation
The first step in injection molding involves preparing the raw material:
- Plastic pellets (also called resin) are loaded into a hopper.
- These pellets can be made from various types of polymers, such as polypropylene, polyethylene, or polystyrene.
- Additives like colorants or reinforcing agents may be mixed with the pellets.
2. Melting the Plastic
Once the material is loaded, it needs to be melted:
- The pellets are fed into a heated barrel.
- Inside the barrel is a large screw that rotates.
- As the screw rotates, it moves the pellets forward.
- The combination of heat from the barrel and friction from the screw melts the plastic.
3. Injection
After the plastic is fully melted, it’s ready for injection:
- The molten plastic is forced into a mold cavity under high pressure.
- This injection is typically done very quickly, often in less than a second.
- The pressure can range from 10,000 to 30,000 psi, depending on the part being made.
4. Dwelling
Once the mold is filled, there’s a brief pause called the dwelling phase:
- Additional pressure is maintained to ensure all mold cavities are filled.
- This helps compensate for material shrinkage as it begins to cool.
5. Cooling
The cooling phase is crucial for part quality:
- The molten plastic begins to cool and solidify as soon as it touches the mold.
- Cooling channels in the mold circulate water or another coolant to speed up this process.
- The cooling time depends on factors like part thickness and material properties.
6. Mold Opening and Ejection
After the part has cooled sufficiently:
- The mold opens.
- Ejector pins push the finished part out of the mold.
- In some cases, robots or human operators remove the part.
7. Resetting
The final step prepares the machine for the next cycle:
- The mold closes.
- The screw retracts, allowing more plastic pellets to fall in front of it.
- The process then repeats from step 2.
Design Guidelines for Injection Molding
Successful injection molding starts with proper design. Key considerations include maintaining uniform wall thickness (typically 2-4 mm), incorporating draft angles (1-3 degrees) for easy part removal, using rounded corners to improve flow, and avoiding sharp edges. Design parts with clear parting lines, minimize undercuts, and use ribs instead of thick walls for strength. Proper gate location and careful consideration of bosses and gussets are also crucial. At OurPCB, we can help optimize your design for manufacturability and cost-effectiveness.
Finishing Options for Injection Molded Parts
After molding, various finishing techniques can enhance your parts’ appearance and functionality. Options include surface texturing for improved grip or aesthetics, painting or plating for color and protection, polishing for smooth surfaces, and vapor smoothing for improved appearance. Additional processes like ultrasonic welding, pad printing, hot stamping, and laser marking can add features or branding. The choice of finishing depends on your part’s intended use, material properties, production volume, and industry requirements. OurPCB offers guidance on selecting the best finishing options to meet your specific needs and quality standards.
Our Injection Molding Capabilities
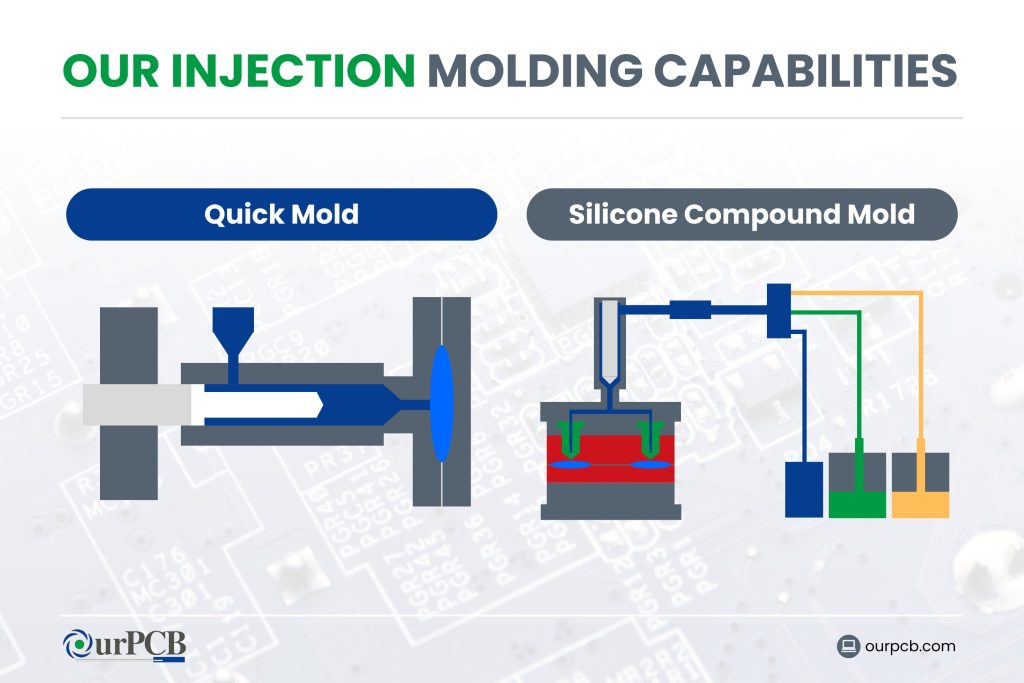
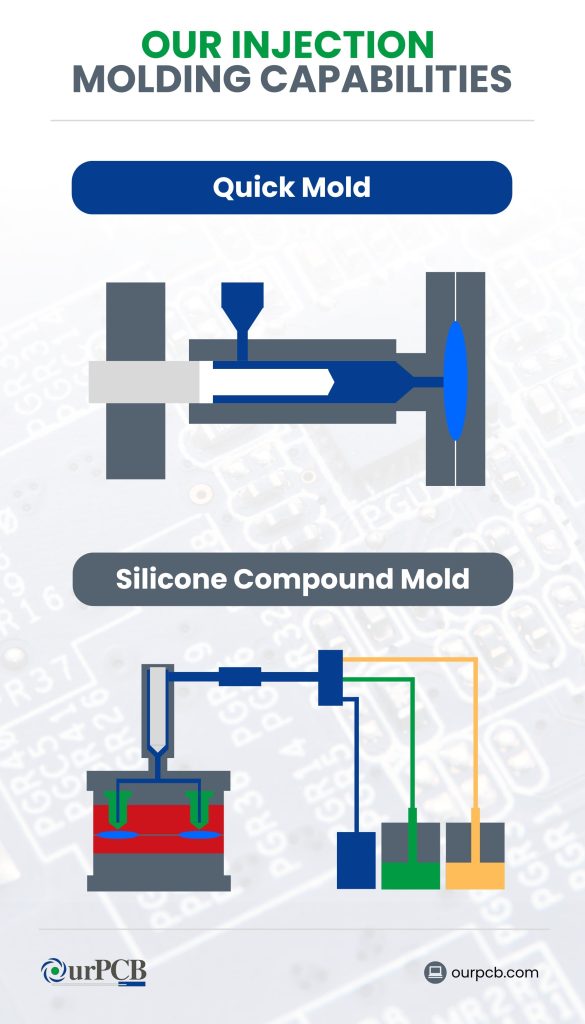
Quick Mold
Rapid Mold Process: We employ CNC rough machining, EDM (electrical discharge machining), mold fitting, mold debugging, mold assembly, mold installation, and injection molding to produce the mold and product swiftly.
Next, the process involves removing injection molding residuals, retrieving the finished products, and trimming residuals. We’ll finish off the process with a manual quality inspection as well as a 3D inspection. The mold and product can be completed in 10 days.
Processing Accuracy: ±0.1 mm/100 mm
Injection Molding Tonnage: 80 to 3000 tons
- PCB Assembly Services: Comprehensive solutions for assembling printed circuit boards.
- Quick Turn PCB Assembly: Fast and efficient PCB assembly to meet tight deadlines.
- High Volume PCB Assembly: Scalable solutions for large-scale PCB production.
- Flexible PCB Manufacturer: Specialized in manufacturing flexible PCBs for diverse applications.
- Low Volume PCB Assembly: Cost-effective solutions for small batch PCB assembly.
- Turnkey PCB Assembly: End-to-end services covering all aspects of PCB production.
- PCB Design Services: Expert design services to bring your PCB concepts to life.
- Rigid-Flex PCB Manufacturer: Manufacturing robust and versatile rigid-flex PCBs.
- PCB Prototype: Rapid prototyping services to test and refine your PCB designs.
- Rogers PCB: High-frequency PCBs ideal for RF and microwave applications.
- Aluminum PCB: PCBs with excellent heat dissipation properties, perfect for high-power devices.
- Metal Core PCB: Thermal PCBs with metal bases for effective heat management.
- High Tg PCB: High glass transition temperature PCBs for improved thermal performance.
- High Frequency PCB: Designed for high-speed and high-frequency applications, ensuring superior signal integrity.
- Heavy Copper PCB: Built with thicker copper layers for high current and enhanced thermal management.
- HDI PCB: High Density Interconnect PCBs offering advanced circuitry in a compact design for complex applications.
- Custom Cable Assembly: We offer a wide range of customized cable services, hybrid cables, and wire harnesses.
Materials:
✔️ PET (Transparent)
✔️ POM
✔️ PC (Transparent, Opaque, Medical Grade, Flame Retardant)
✔️ PC+GF
✔️ PBT
✔️ PBT+GF
✔️ PA6
✔️ PA6+GF
✔️ PA66
✔️ PA66+GF
✔️ PPA
✔️ PPA+GF
✔️ PPS
✔️ PMMA
✔️ PPSU
✔️ SAN
✔️ ABS (Transparent, Flame Retardant)
✔️ ABS+UV resistant
✔️ ABS+GF
✔️ PC+ABS (Standard, Medical Grade, Flame Retardant, High Gloss)
✔️ PP (transparent, opaque)
✔️ PP+GF
✔️ PE (Transparent, Opaque, +PE Modified)
✔️ GPPS (Transparent)
✔️ HIPS (Natural Color, Modified)
✔️ ABA (Transparent)
✔️ TPU (Transparent, Opaque, Various Hardness)
✔️ TPE (Transparent, Opaque, Various Hardness)
Silicone Compound Mold (Vacuum Compound Mold and Low-Pressure Injection Mold)
Silicone Molding Process: This process starts with fixing the mold support, mixing silicone rubber, and silicone injection molding. Then, we’ll move on to vacuum treatment, initial demolding, and mold closure.
Next, we’ll inject the material, which is followed by demolding and removing burrs. Finally, we’ll conduct a manual inspection and 3D inspection. We can produce 200 pieces in 5 days.
Processing Accuracy: ±0.2 mm /100 mm
Injection Molding Tonnage: Minimum 0.5 mm, optimal 1.5 mm to 5 mm
Materials:
✔️ ABS (DPI8150, PX5118, PX200, PX600)
✔️ ABS8150 High-Temperature Resistant up to 70° C
✔️ PX223HT High-Temperature Resistant up to 150° C
✔️ Soft Rubber 8400 Customizable Colors
✔️ Soft Rubber T387 Transparent
✔️ Flame Retardant 8263
✔️ Transparent Material: PC520 with Blue Color
✔️ Transparent Material: PMMA5210
✔️ Semi-Transparent Silicone 905 (35–40° C)
✔️ Semi-Transparent Silicone 918
✔️ Fully Transparent Silicone T-4 (38–42° C)
✔️ Chinese Fully Transparent Silicone
✔️ PP-Like Material PP5690
Advantages and Disadvantages of Injection Molding
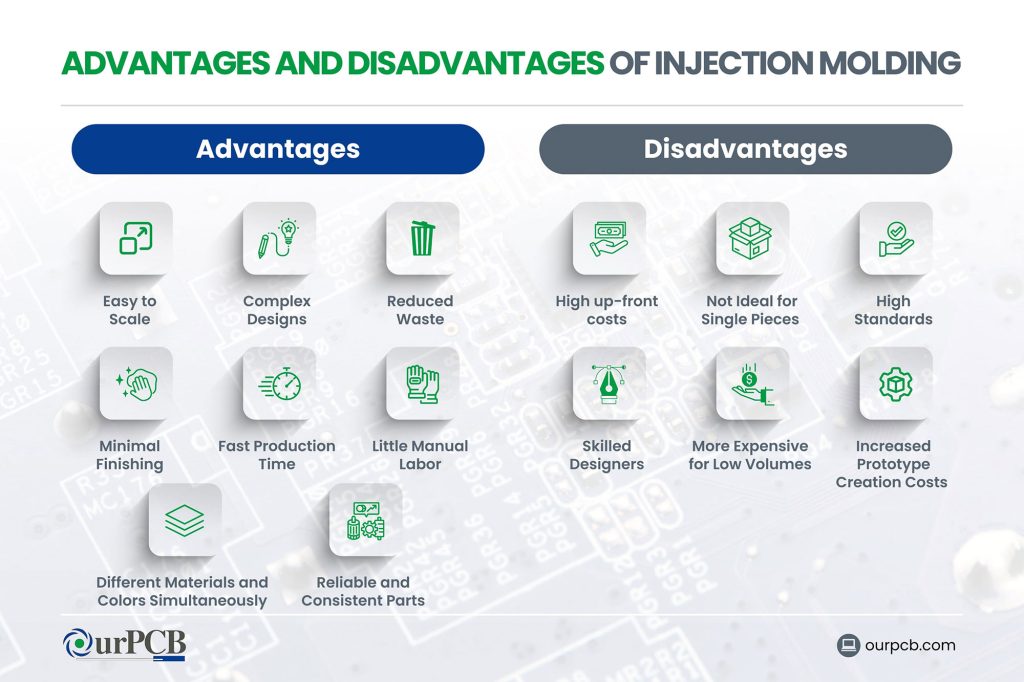
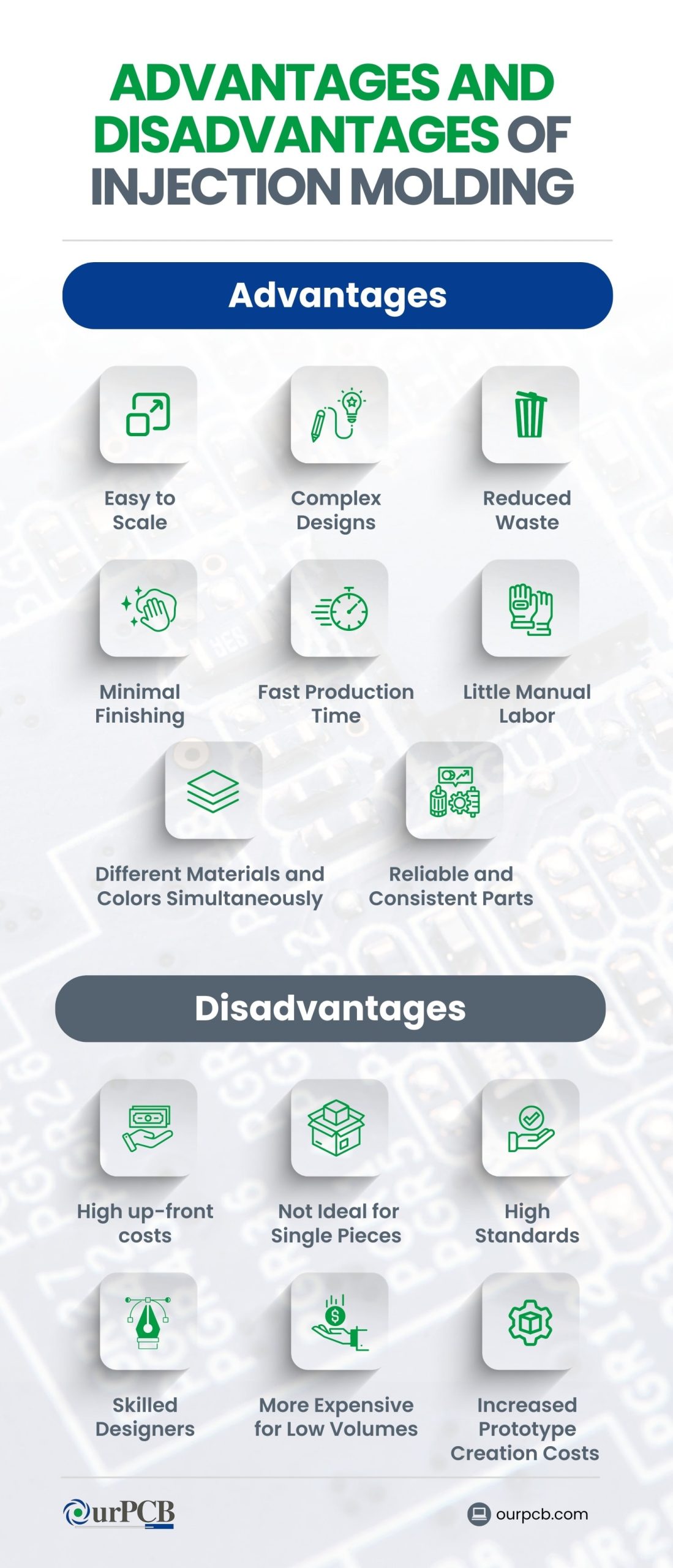
Advantages
- Easy to scale production to fabricate multiple parts, with the cost of production lowering the more you scale
- Can be used to mold products with different materials simultaneously, as well as plastics in multiple colors
- Easy to design and manufacture intricate designs with complex geometrical shapes
- Reduces material wastage, making it more eco-friendly
- Produced parts need minimal finishing after mold ejection to create the final product or appearance
- Produces identical parts that lead to part reliability and consistency during high-volume production
- Fast production times
- Requires relatively little manual labor, which lowers production costs
Disadvantages
- High up-front costs of the injection molding machines
- Expensive to produce parts in low volumes
- Not ideal for molding large parts as single pieces
- Requires high standards and skilled designers to create prototypes and refine them to get the final mold
- Prototype creation can be time-consuming and costly
Applications of Injection Molding
- Plastic car parts (e.g., bumpers, dashboards, grills)
- Consumer plastics (e.g., bottle caps, smartphone cases, toys, pocket combs, storage containers, etc.)
- Medical devices (e.g., syringes, dishes, trays, valves)
- Electronic components (e.g., enclosures, connectors, protective sleeves, etc.)
- Plastic furniture parts (e.g., chairs, small tables, seat covers, cushions)
- Wire spools
Why Choose Us as Your Injection Molding Service Provider?
As your top injection molding service supplier, our skilled staff provides timely online pcb quote and real-time order status tracking.
We combine numerous processes to provide one-stop prototype and product processing services, including advanced CNC machining, 3D printing, silicone molding, rapid and injection molding, sheet metal processing, and multiple surface treatment technologies.
We are ISO 9001, ISO 14001, IATF 16949, and ISO 27001 certified, and we have a well-established quality control system.
With superior client satisfaction, high-quality goods, and affordable rates, we aspire to be the best choice for all of your injection molding service requirements.
Contact us today to receive an accurate quote or consultation. We look forward to working with you on your next project.
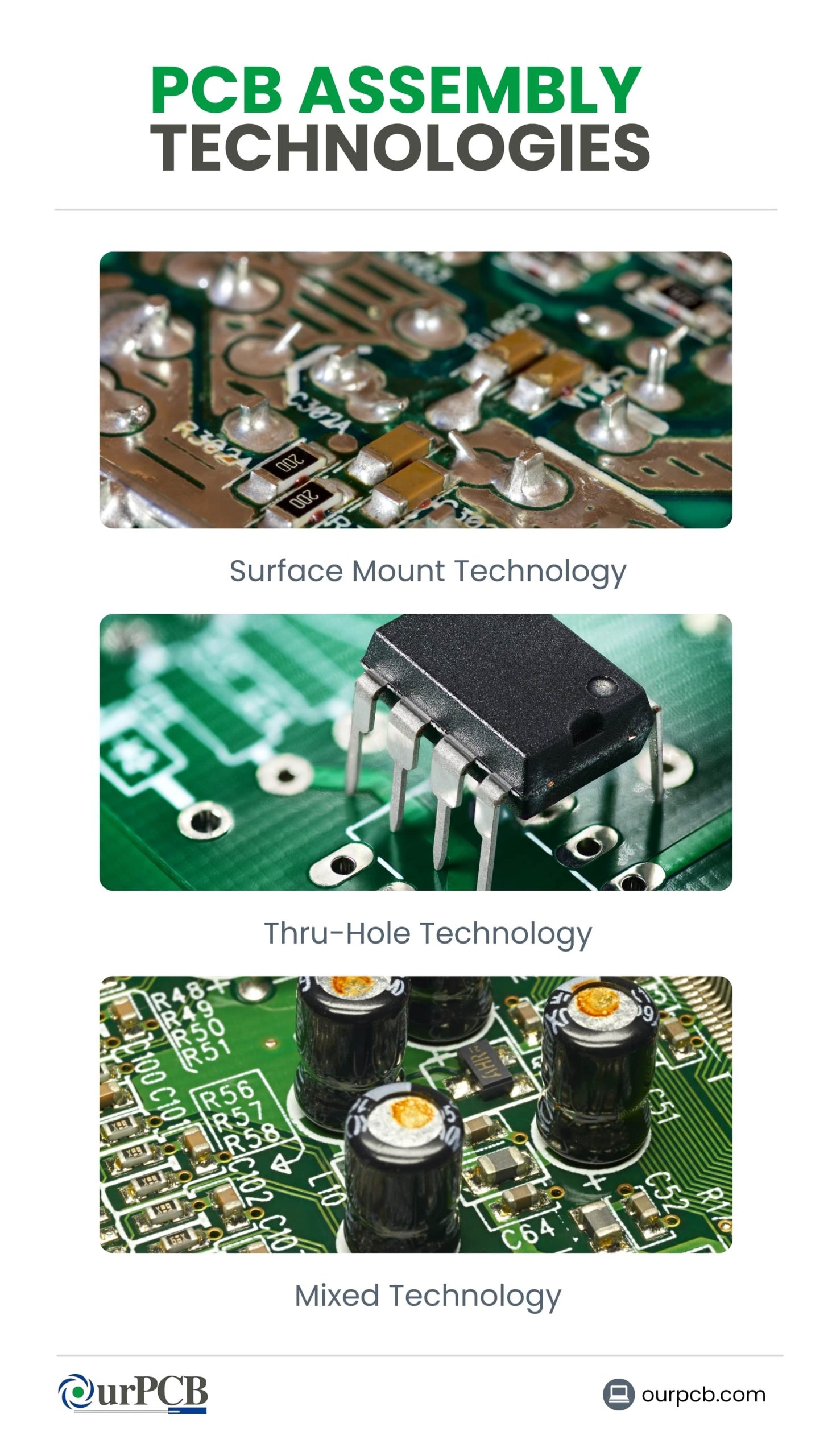
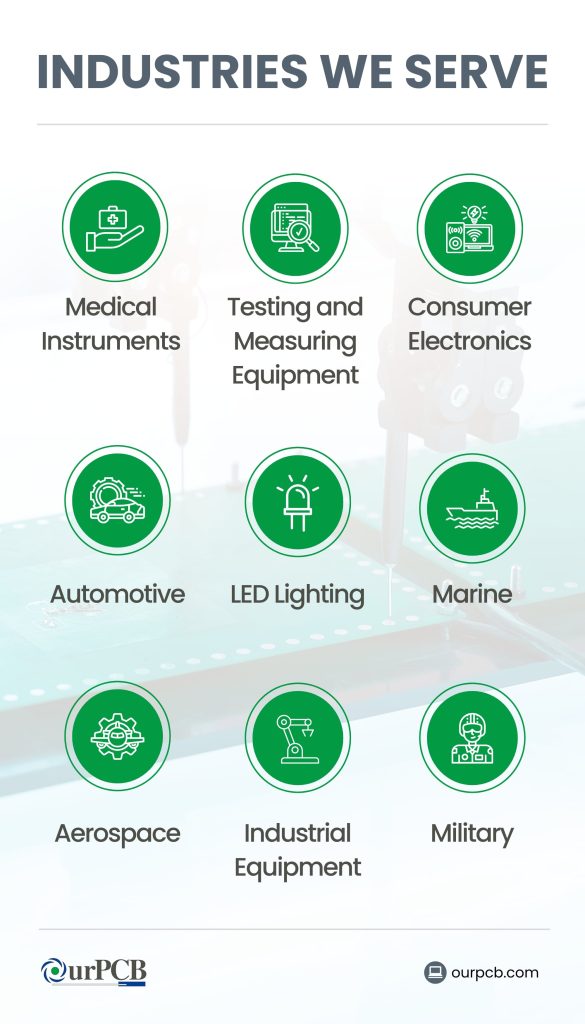
Back to top: Injection Molding Service
- 1Order and Procurement
- 2PCB Manufacturing and Preparation
- 3Assembly and Soldering
- 4Inspection and Quality Control
- 5Finalization and Shipping
- Bare PCB in 8 working hours
- PCBA with components in 2 working days
- Bare PCB manufacturing
- Components sourcing
- PCB assembling
- Wire harness manufacturing
- Casing /Housing manufacturing
- Programming/Testing
Free Consultation
Adrian Leitch


Andrew Durrant


Andrew Peeler


Andrew Wood


Ben Thomas


Darren Larosa


Debra Beukes


Eastern Europe Archives


frankyc


Fred Van


Greg MacDonald


John Powell


Jonathan Pippard


Jordan Thurgood


Justin Regan


Mark A


Mark Pagura


Maryanne Hassell


Matthew O'Neill


mitch clark


Oli


Peter Lambert


Sasha Marks


Slavko Mali


SPI MX


Steve Visser


Steven Munari


Steven Vatev


Tane Pendragon


Tasmiah Khan


Trevor Gardner


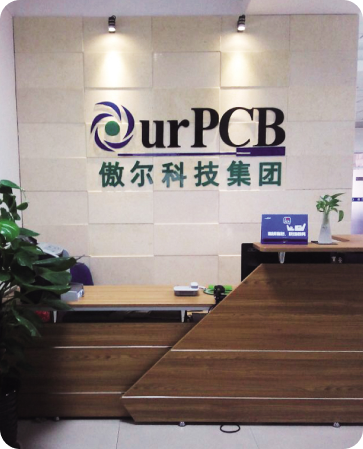
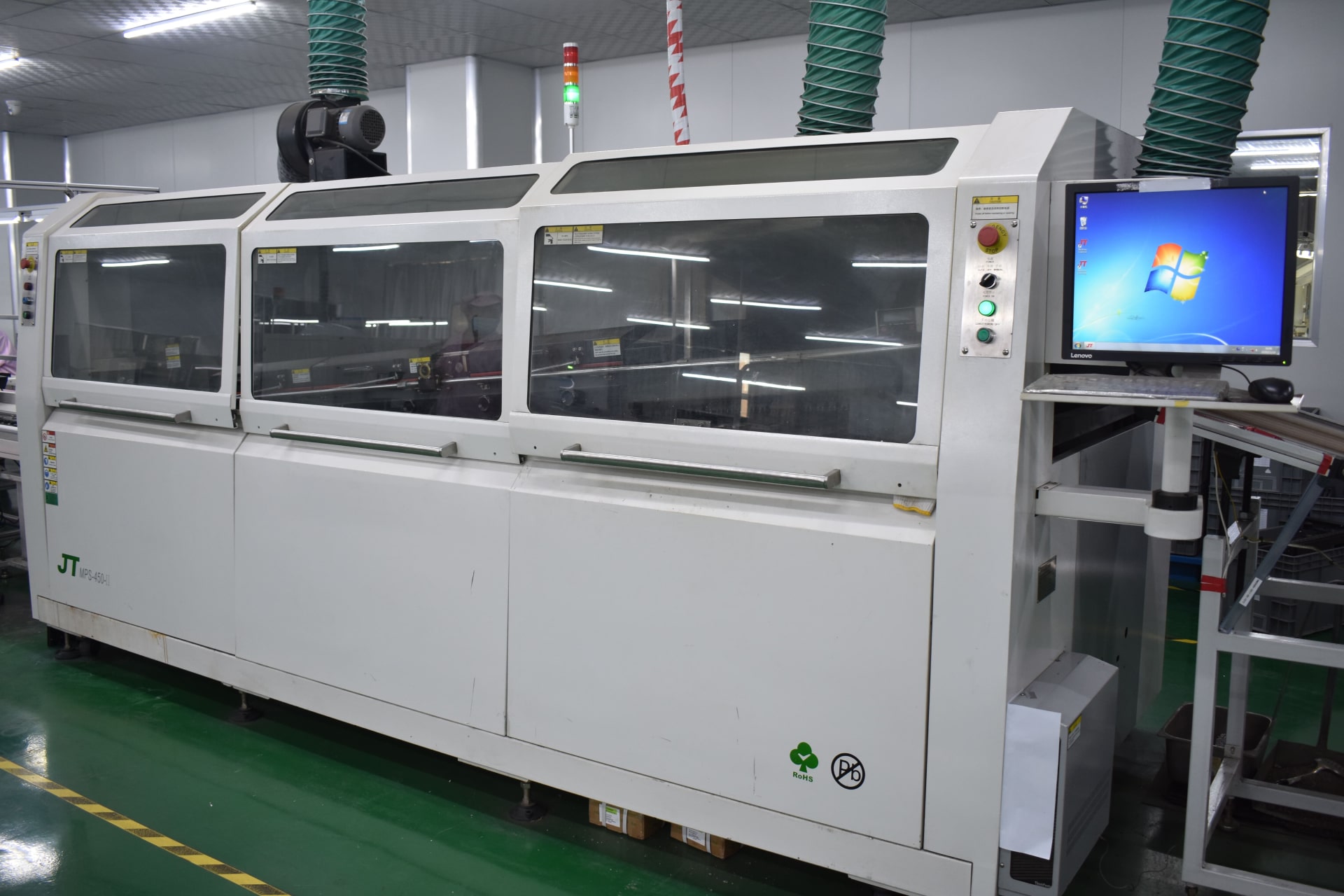

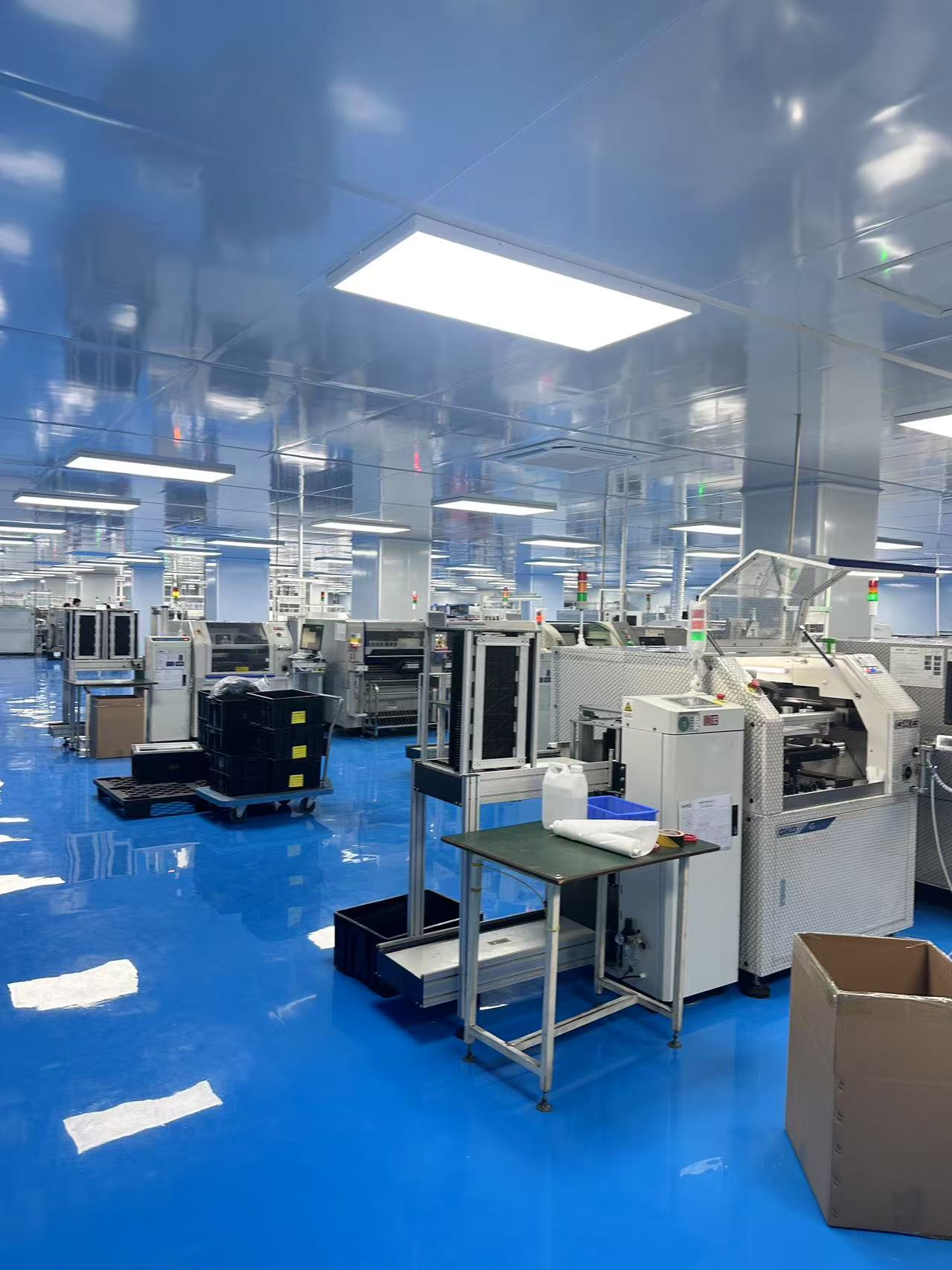
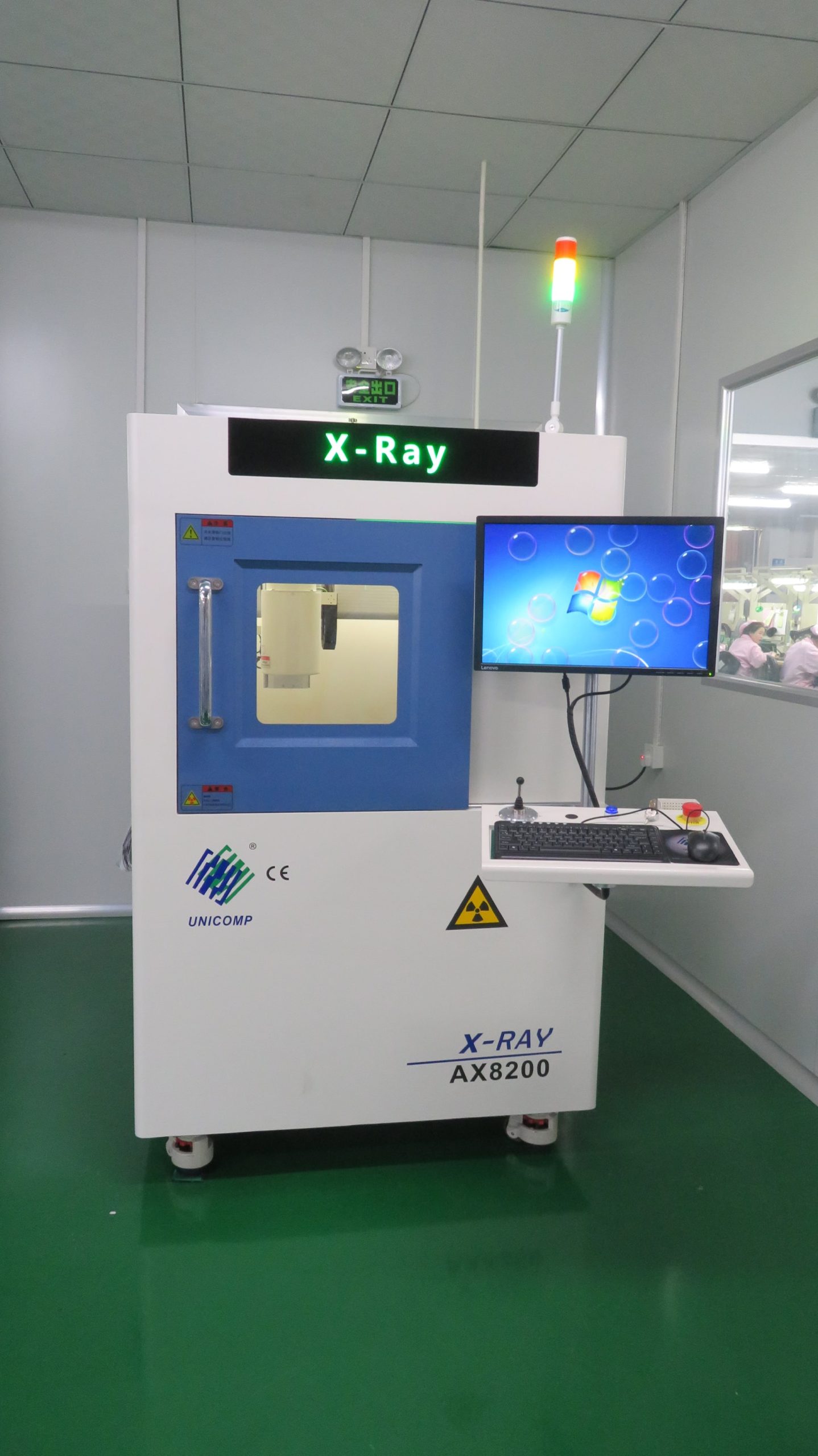
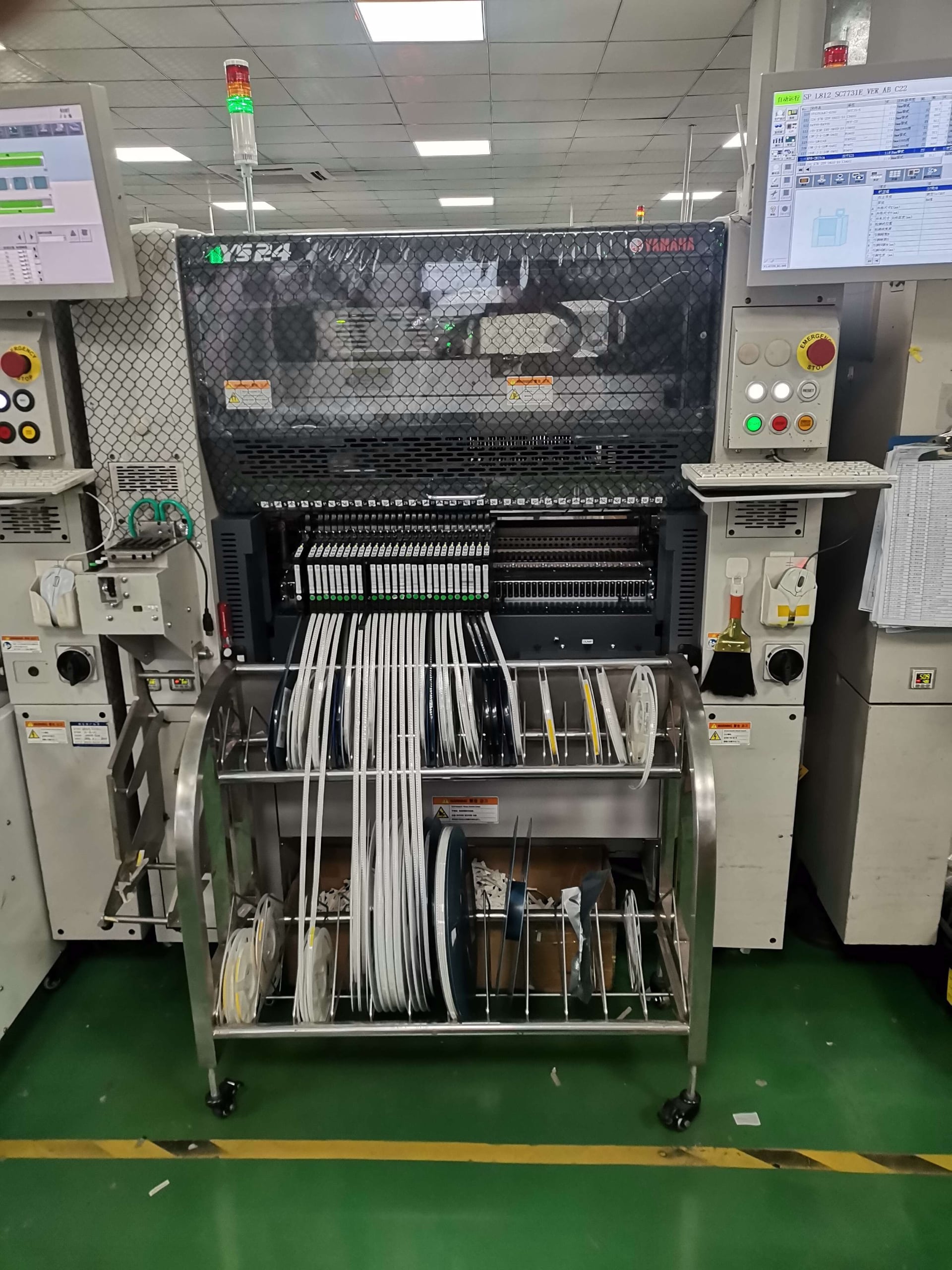
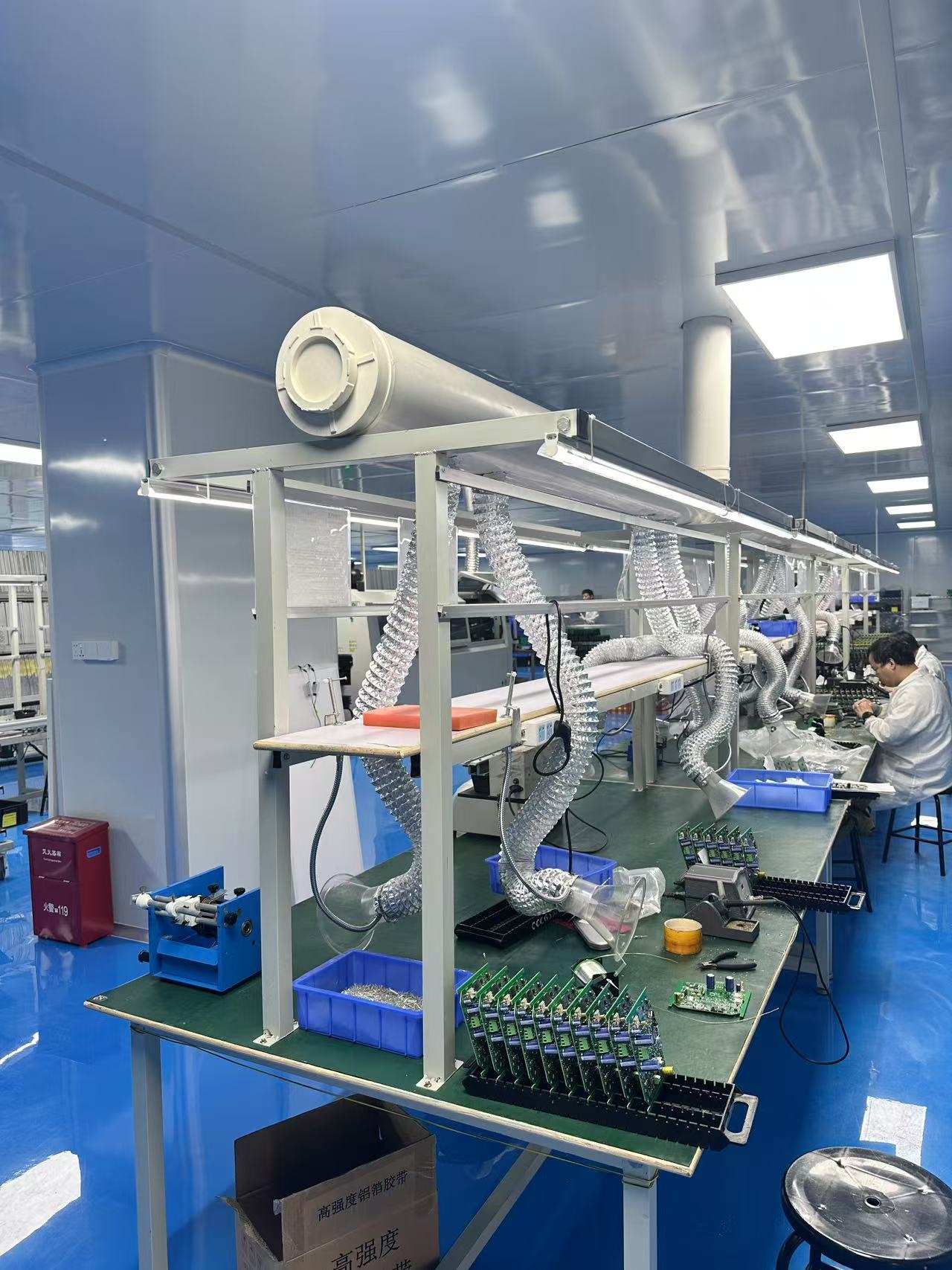
Take a Factory Tour!
OurPCB’s manufacturing journey began with our Shijiazhuang factory in 2007. This factory spans over 10,000 meters, 90% of which is dedicated to advanced PCB assembly services. Over 300 skilled technicians manage 5 SIEMENS SMT lines to produce top-notch PCBS for affordable prices.
As OurPCB grew, we needed to expand our facilities and production capacity. In 2017, we built our second factory in Shenzhen to increase our standard PCB assembly services. This factory is 5,000 square meters and has 8 YAMAHA SMT lines, including X-ray and AOI capabilities. The production line employs 110 dedicated staff to meet your PCB assembly needs.
We’ve expanded our services to English-speaking customers worldwide. In 2014, we opened OurPCB in Melbourne, Australia, to provide PCB assembly services to Australian and international clients. Join us in bringing your projects to life with OurPCB!

