Rigid Flex PCB Fabrication Supplier & Prototype Manufacturer
OurPCB provides high-quality rigid-flex PCB manufacturing and assembly services. Rigid-flex PCBs combine flexible and rigid layers, offering durability and space efficiency for complex electronic designs. We ensure precision engineering, strict quality control, and fast turnaround times to meet your requirements.





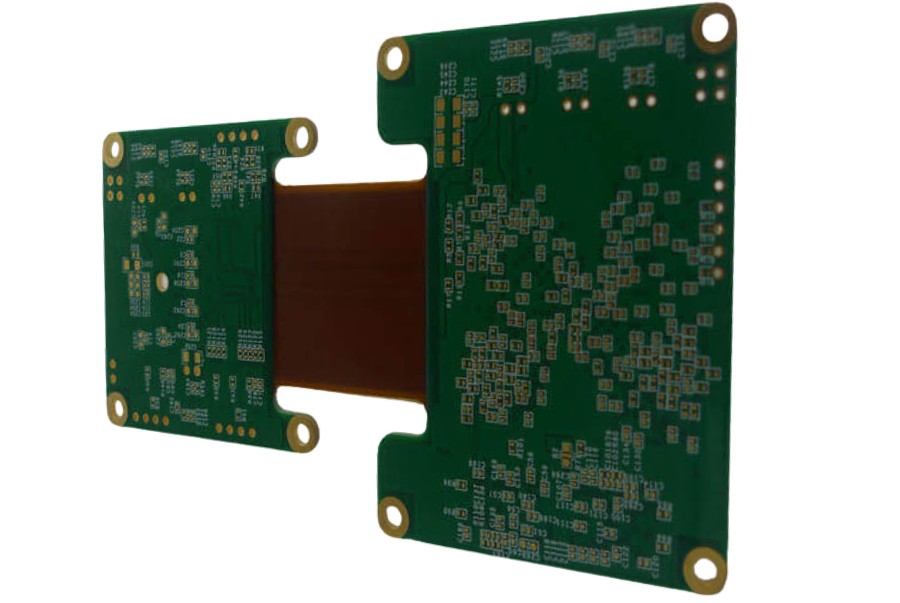





What are Rigid-Flex PCBs?
Rigid-flex PCBs are a hybrid circuit board combining components of rigid and flexible PCBs, and are used to connect electronic components in a variety of both consumer and non-consumer devices. This board type can be folded or flexed continuously on the flexible section, which usually joins two rigid parts.
PCB Manufacturing Process







What are the Advantages of Rigid-Flex PCBs?
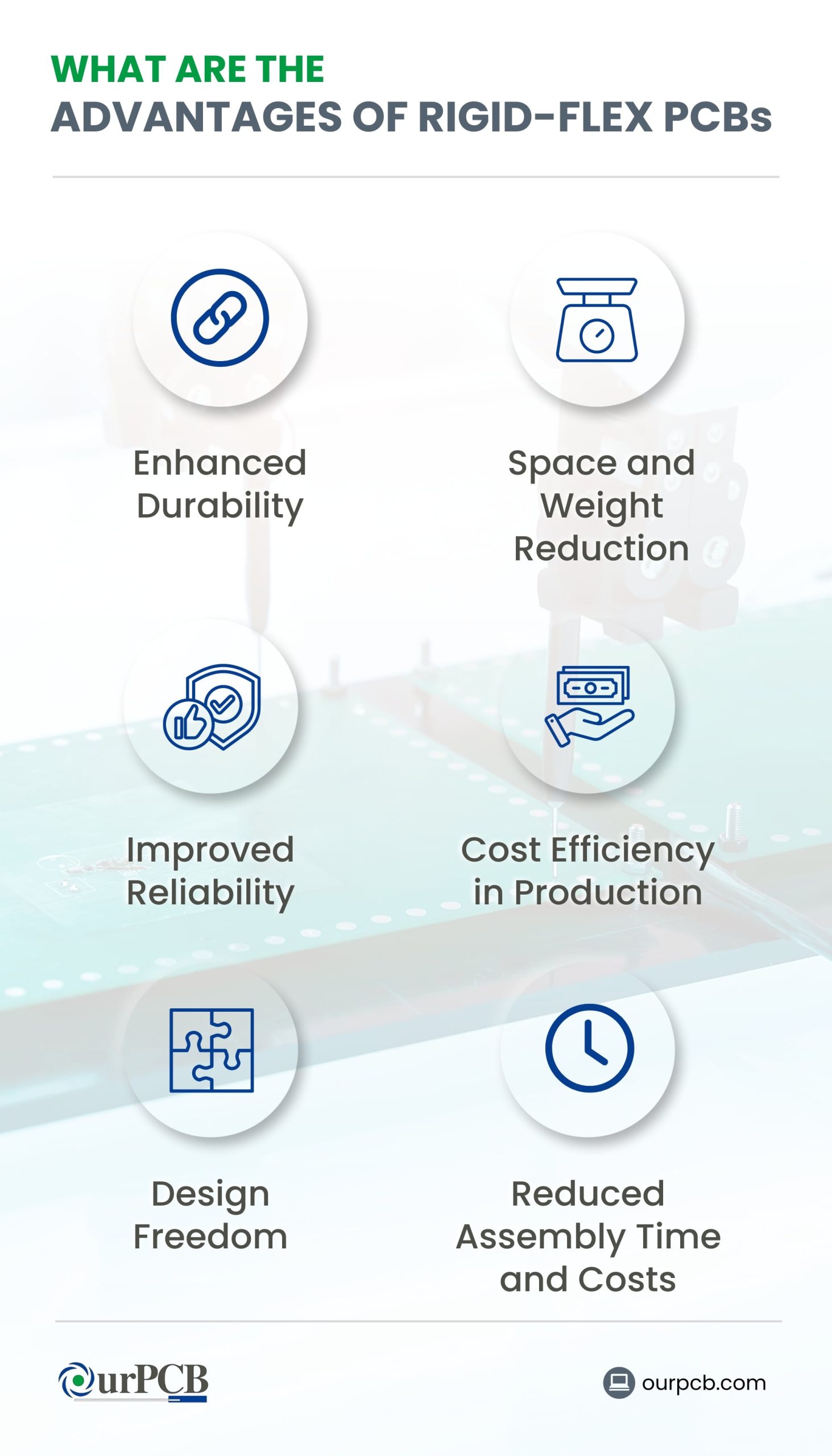



The flexible part of the circuit is vibration-and shock-resistant, meaning it can hold heavier components without cracking. These boards are also more resistant to high temperatures, radiation, and other harsh environments, making them suitable for rugged applications.
Rigid-flex PCB designs are more challenging to create because you have to use a 3D development space to have better spatial efficiency. But the result is a lightweight and space-optimized design that fits in compact electronics like wearables.
Compared to regular PCBs, the rigid-flex type has fewer connectors and interfacing materials. Interconnections are potential sources of failure, so this design makes the PCBs more reliable.
Manufacturing rigid-flex PCBs is more expensive than building their rigid counterparts, but the cost savings come during PCB assembly. Since they replace wired interconnects (harnesses and connectors) with conductive copper layers inside the board, the assembly costs and error risks are lower.
The ability of rigid-flex circuits to adopt complex shapes and compact sizes gives you the freedom to experiment with different device designs because the PCB will fit inside more easily.
With fewer interconnections and parts, assembling rigid-flex PCBs takes less time, minimizes wiring errors, and reduces costs because you won’t need manual labor to insert the connector wiring joints.
What is the Cost of Rigid-flex PCB?
The cost of rigid-flex PCBs varies widely depending on the complexity and number of layers. Here is a detailed cost comparison based on complexity and layers:
Rigid-Flex PCB | Low Complexity | Medium Complexity | High Complexity |
---|---|---|---|
4-Layer | $20 – $50 | $50 – $200 | $200 – $1,000+ |
6-Layer | $50 – $100 | $100 – $500 | $500 – $2,000+ |
These prices are influenced by factors such as the number of layers, the complexity of the design, the materials used, and the specific manufacturing processes required. For example, military and aerospace applications often use more advanced materials and designs, which can increase costs significantly.
Rigid-flex PCBs are generally more expensive than standard rigid or flexible PCBs due to their complex manufacturing process, which involves combining rigid and flexible materials to create a single integrated board. This integration helps in reducing the overall size and weight of the device while improving reliability and performance in demanding environments.
For precise pricing tailored to your specific project requirements, please request a free quote by filling out our form.



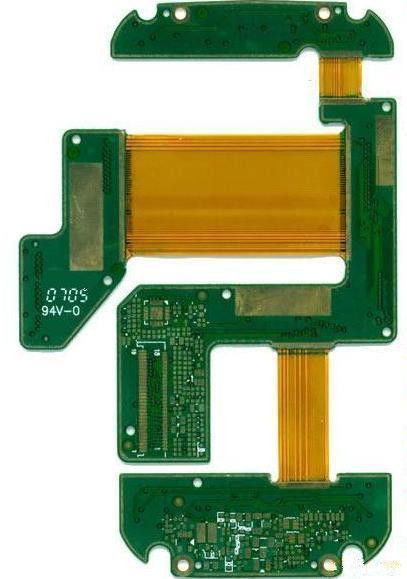
Our Rigid-Flex PCB Manufacturing Capabilities
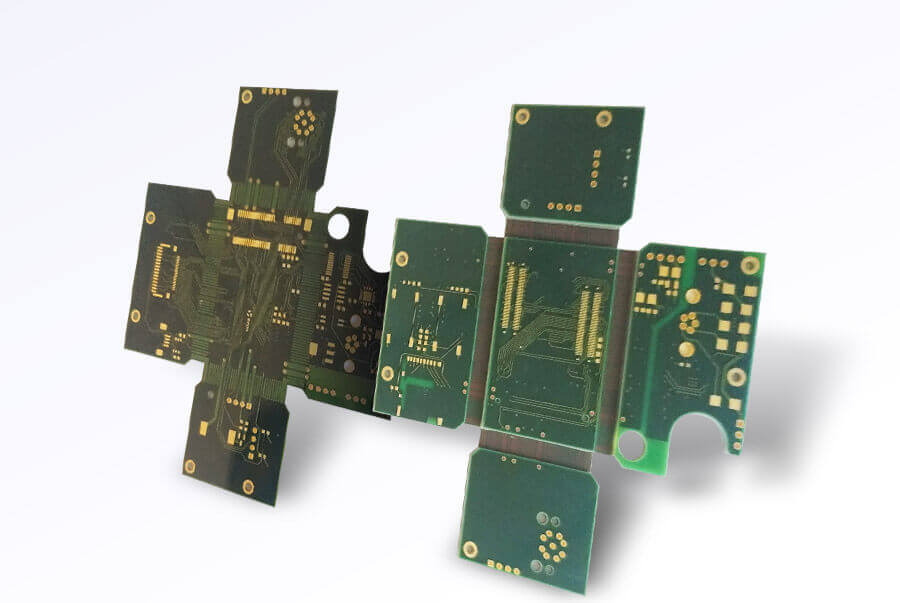



We manufacture 2 to 30-layer rigid-flex PCBs with a 2-week lead time. Solder mask, silkscreen, and surface finishes match rigid PCBs, customized to your requirements.
We use polyimide, Rogers, and FR4. FR4 suits rigid boards, polyimide is for flexible circuits, and Rogers is ideal for high-frequency applications.
We ensure tight tolerances and controlled impedances using advanced equipment. Our expertise guarantees precise circuit wiring for all rigid-flex PCB applications.
Our Shijiazhuang & Shenzhen factories assemble SMT and THT components, including BGA, QFN, SOP, leaded, and leadless carriers, even in mixed assemblies.
We manufacture buried vias, microvias, and high-density components. Our Shijiazhuang factory meets IPC 6012 Class 3/A standards for military, medical, and aerospace applications.
Quality control is a significant aspect of the rigid-flex PCB production process. It includes methods like ICT, FPT, AOI, automated X-ray, solderability, and burn-in testing.
Customize layers (2-30), materials (FR4, Polyimide, Rogers, Aluminum), dimensions, thickness, and finishes. Choose laminated or unlaminated designs.
PCB Assembly Services

We handle everything from parts sourcing to final assembly, providing a hassle-free experience that ensures top-quality boards every time.

Whether you need a few prototypes or large-volume batches, our flexible assembly services adapt to your project’s scope and timeline.

Stay environmentally responsible with our compliant assembly processes, offering RoHS and lead-free options for safe, reliable builds.

No matter the complexity, we can assemble boards of all configurations—single-layer, multi-layer, or a mix—to match your exact specifications.

From one-off prototypes to bulk orders, we accommodate projects of all sizes without compromising on quality or turnaround time.

Join our growing community of satisfied clients who rely on our dependable assembly expertise and dedicated customer support.
Millions of business and innovators use OurPCB
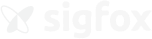
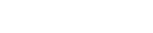
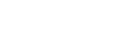


PCB Board Process
Order Received
- Component Procurement
- Preparation
- PCB Manufacture
- Make Process Flow
Soldering
- Solder Printing/Wave Soldering
- SMT/Plugging
- Inspection (repair if necessary)
- AOI (repair if necessary)
- Transfer
Parts Assembly
- Manual Assembly
- Cleaning
- Wire Screw
- Inspection
- Repair If Necessary
Finalization
- Final Confirmation
- Packing
- Shiping
Technical Capabilities
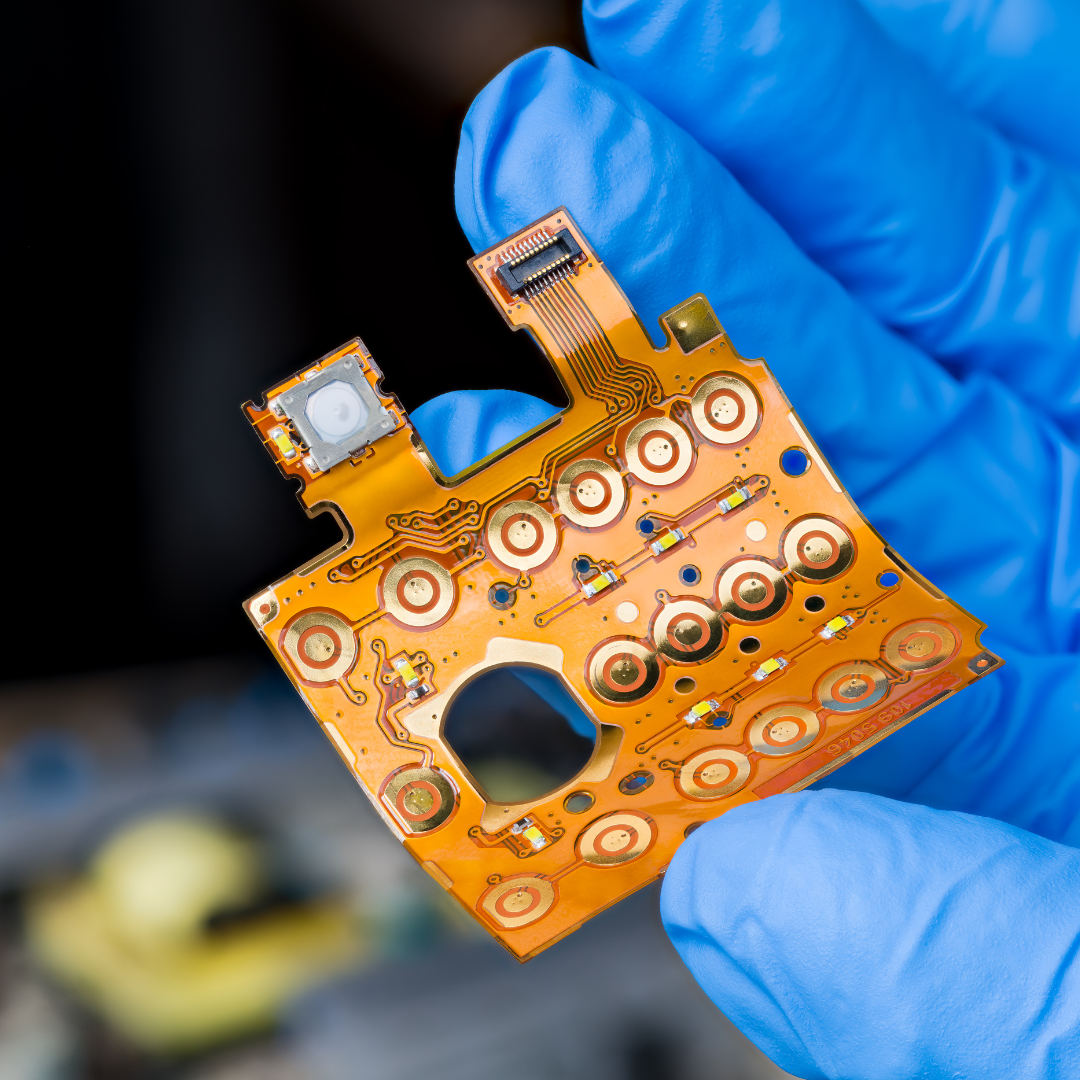



Capabilities & Services
- One-stop PCBA Services (PCB Manufacturing + Components Sourcing + Assembly)
- SMT Assembly + THT Assembly
- BGA Rework
- 60,000 Chips/Hour
- Down to 01005/0210 Size
- Accuracy<±40μm
- Min. QFN Pin Width/Space: 0.15mm/0.25mm
- Min. BGA Diameter/Space: 0.2mm/0.35mm
- Rigid, Flex, HDI, & High-speed Power Boards
- Up to 50 Layers
- 60GHz High Frequencies
- Min. Trace Width/Spacing: 2.5mil/2.5mil
- AOI, X-ray, ICT & FCT Testing
- Controlled Impedance
- ISO 9001, ISO 13485, ISO 14001, IATF 16949, IPC-A-610, UL Certified
- Automotive, Medical, & Military-grade PCBA Manufacturing


Mon-Fri: 24 hours,
Sat: 9am-6pm, GMT+8

Reach us at
[email protected]
24 hours online

+86-199-30589219
Mon-Fri: 24 hours,
Sat: 9am-6pm, GMT+8
Rigid-Flex PCB Supplier FAQs
What is the Difference Between Rigid-Flex PCBs and Standard PCBs?
Standard PCBs are rigid, but rigid-flex PCBs combine rigid and flexible PCB properties into a single, lightweight, space-saving structure. The flexible board is also less susceptible to mechanical stress because it can absorb vibrations.
Can you Manufacture Rigid-Flex PCBs with Blind and Buried Vias?
Yes. However, making these vias requires a different set of design rules because of the materials used and the manufacturing process.
Can you customize Rigid-Flex PCBs to Fit Specific Design Requirements?
The flexible component of the Rigid-Flex PCBs can be bent, shaped, wrapped, or folded into any 2D or 3D shape. These features make Rigid-Flex PCBs perfect for use in medical and surgical equipment, consumer electronics, automotive and space applications, and smart wearable devices, that needs both properties of durable rigid boards and the flexibility of flexible circuit boards.
Is it Possible to Order Small Quantities for Rigid-Flex PCB Prototype Development?
Yes. Our lead time for 1 to 2 layer prototypes is 5 days, which stretches up to 11 days for 12-layer PCBs (shipping time not included). Overall, we can prototype 1 to 32-layer PCBs within 2 weeks, and we’ll give you a formal quotation within 8 working hours after receiving your request.
What industries benefit from rigid-flex PCBs?
Rigid-flex PCBs are essential in industries requiring durability, space efficiency, and reliability:
- Medical: Used in handheld monitors, imaging equipment, cochlear implants, and pacemakers, where flexibility and miniaturization are critical.
- Military: Ideal for weapon guidance, surveillance, and secure communication systems, ensuring high performance in harsh environments.
- Aerospace: Found in radar, control tower equipment, and vibration testing systems, offering lightweight, high-reliability solutions.
- Automotive: Integrated into dashboard displays, transmission controls, AC systems, and ECUs, improving durability in extreme conditions.
- Telecommunications: Used in satellites, routers, base stations, and handheld devices, providing compact, high-speed connectivity solutions.
- Consumer Electronics: Applied in wearables, smart appliances, remote controls, and gaming devices, where space-saving designs are essential.
- Industrial & Manufacturing: Essential in control panels, robotic systems, and high-reliability test equipment, supporting rugged applications.
How do flex PCBs compare to rigid-flex PCBs?
The main difference lies in their structure and applications:
- Flex PCBs: Made entirely of bendable core materials, they withstand vibrations and repeated folding. An overlay process protects the flexible annealed copper circuits.
- Rigid-Flex PCBs: Combine rigid and flexible sections, each using different substrates and materials. The rigid part contains inflexible etched or electro-deposited copper for added durability.