Contents
- What is a PCB Controller?
- What are the Types of PCB Controller?
- What are the functions of a PCB controller?
- 1. PCB Control
- 2. Managing Pins and Other Connections
- 3. Controlling Data Flow
- 4. Signal Integrity Management
- 5. Thermal Management
- 6. Power Management
- 7. Timing Management
- 8. Configuration Management
- Dimensions of PCB Controllers
- Key Aspects of PCB Controller Dimensions:
- Key Factors for Choosing an Efficient PCB Controller
- PCB Controller Materials
- PCB Controller Installation
- Key Materials for Building and Assembling PCB Controllers:
- How To Design a PCB Controller
- Step 1: Define the Requirements
- Step 2: Choose the Right Components
- Step 3: Schematic Design
- Step 4: PCB Layout Design
- Step 5: Testing and Simulation
- Common Mistakes in PCB Controller Design and How to Avoid Them
- Tools for Designing Efficient PCB Controller Boards
- Applications of PCB Controller
- Embedded Systems
- Contact OurPCB
What is a PCB Controller?
A PCB controller manages signals and power across various components, ensuring smooth communication between hardware elements. PCB controllers are essential in industries like automotive, consumer electronics, and industrial applications. Efficiency in PCB controllers directly impacts overall device performance, reducing power consumption and ensuring reliable operation in complex systems.
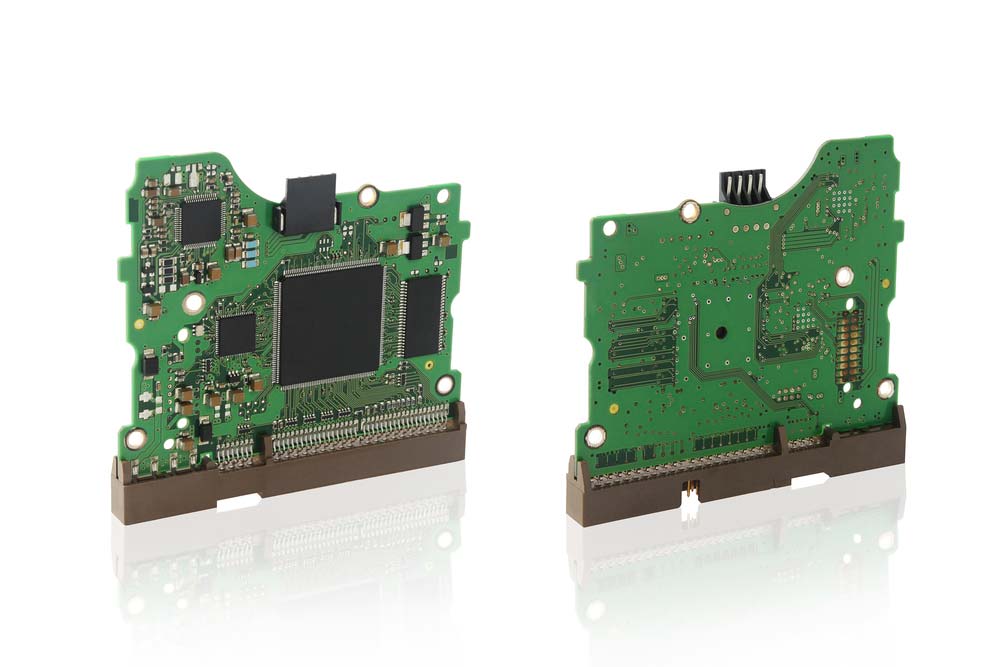
What are the Types of PCB Controller?
The types of PCB controllers include Microcontrollers (MCUs) for device control, Digital Signal Processors (DSPs) for high-speed computations, Programmable Logic Controllers (PLCs) for industrial automation, Field-Programmable Gate Arrays (FPGAs) for customizable digital designs, and Application-Specific Integrated Circuits (ASICs) for specialized, high-performance tasks.
Type | Description |
Microcontrollers (MCUs) | Compact integrated circuits designed for specific operations in embedded systems. Ideal for controlling devices like home appliances, automotive electronics, and machinery. |
Digital Signal Processors (DSPs) | Specialized microprocessors for high-speed numerical operations, suitable for audio signal processing, telecommunications, and digital image processing. |
Programmable Logic Controllers (PLCs) | Used in industrial environments for automating mechanical processes. They handle multiple input/output arrangements with high reliability and precision. |
Field-Programmable Gate Arrays (FPGAs) | Integrated circuits configured by the customer after manufacturing. Versatile and used in applications requiring specific, customized digital logic designs. |
Application-Specific Integrated Circuits (ASICs) | Custom-designed chips for specific applications, offering high performance and low power consumption. Commonly used in high-volume products. |
What are the functions of a PCB controller?
PCB Controller Functions involve managing and optimizing the operation of a printed circuit board (PCB). These functions include routing electrical signals, distributing power, and controlling data flow to ensure efficient communication between components. PCB controllers also maintain signal integrity, manage thermal conditions to prevent overheating and synchronize timing across components. Additionally, they manage initial configurations, detect errors, and handle system interfaces, playing a vital role in the PCB's functionality and performance.
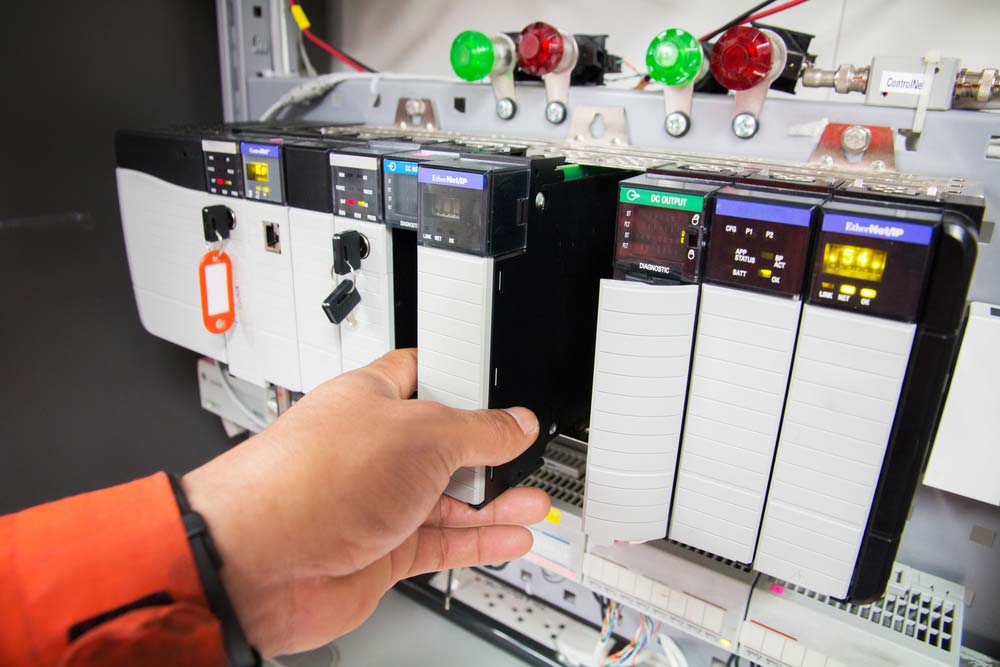
1. PCB Control
The primary function of a PCB controller is to ensure all the board functions run smoothly. It connects to the memory, logic, and power components to ensure all inputs and outputs are in order.
2. Managing Pins and Other Connections
PCB controllers also manage connection pins by setting & governing data exchange rules. This function means the board has the power to manage the host board interactions with other PCBs.
3. Controlling Data Flow
While managing pins and connections, the controller can regulate data flow across the board. For instance, it can decide when and which components should receive data. Controlling data flow is critical if the board has different sections that must exchange data.
4. Signal Integrity Management
Ensuring signal integrity is crucial in PCB design, especially for high-speed applications. The PCB controller can implement strategies to minimize signal degradation and interference, which includes controlling trace layout and impedance matching.
5. Thermal Management
The controller can also play a role in managing the thermal output of the PCB, ensuring that heat is distributed evenly and dissipated effectively to prevent overheating and potential damage.
6. Power Management
This includes not only distributing power across the PCB efficiently but also managing power integrity to ensure stable operation under various load conditions. The controller can adjust power distribution in response to changes in component activity and power requirements.
7. Timing Management
PCB controllers often need to manage timing issues, such as clock distribution and synchronization across various components, to ensure that the system operates coherently and efficiently.
8. Configuration Management
Creating and managing the board’s configuration involves setting up initial states and configurations of the PCB and its components. This may include firmware updates, setting operational modes, and configuring peripheral devices.
Dimensions of PCB Controllers
The “Dimensions of PCB Controllers“ refers to the physical size and layout considerations of a PCB controller within a printed circuit board (PCB). This includes factors such as the integration level, system requirements, available space, and package type, which collectively determine the overall size and configuration of the controller on the PCB.
Key Aspects of PCB Controller Dimensions:
Key Aspect | Description |
Integration Level | Controllers with more integrated components are larger and more complex, affecting the space they occupy on the PCB. |
System Requirements | Higher complexity and functionality require larger controllers to accommodate additional components and circuitry for more control functions and processing power. |
Available Space | Limited space on the PCB constrains the size of the controller; designers may need to choose compact designs or sacrifice functionality to fit within the available area. |
Design Considerations | Peripheral placement and space optimization by the designer can result in a more compact and efficient controller layout. |
A circuit board with slots left for soldering a microcontroller.
Special Offer: Get $100 off your order!
Email [email protected] to get started!
Key Factors for Choosing an Efficient PCB Controller
- Power Requirements: Ensure the controller matches the available power supply based on the specific application's demands, such as higher power for industrial use.
- Compatibility: Must be compatible with the board's software, hardware, and platform for proper control signal transmission.
- Memory Capacity: Higher internal memory improves performance, especially for complex systems that require batch processing.
- Reliability: Essential for critical applications (e.g., medical, military) and reduces costly downtimes.
- Cost: High-performance controllers are more expensive; choose one that fits the application to avoid underutilization or excess cost.
- Ease of Use: A powerful controller should also be user-friendly to ensure optimal performance and efficiency.
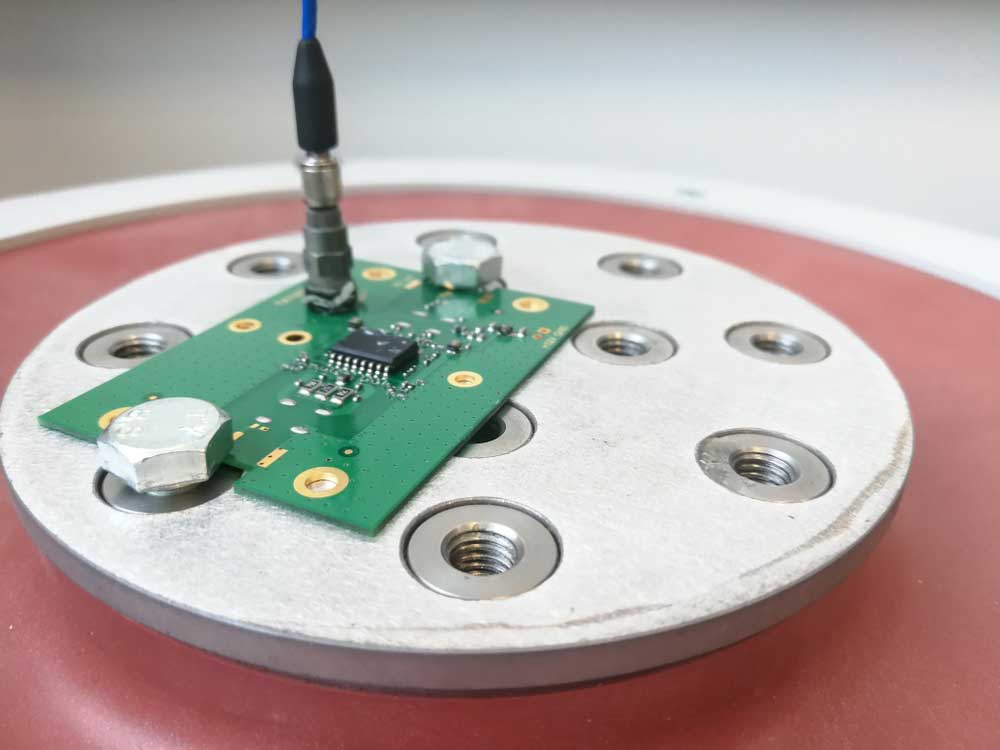
PCB Controller Materials
A PCB controller’s materials play a crucial role in its performance, especially in conductive tracks where traces can be made from aluminum alloys, copper, or gold.
- Copper: Highly conductive and ideal for high-speed signal operations.
- Gold: Conductive and highly resistant to corrosion, making it perfect for harsh outdoor conditions despite being more expensive.
- Aluminum Alloys: Cheaper than both copper and gold, offering excellent static electricity protection, though less durable.
Material Considerations Based on Controller Size:
- Small Controllers: Use thinner, less conductive materials.
- Large Controllers: Require thicker, more conductive metals.
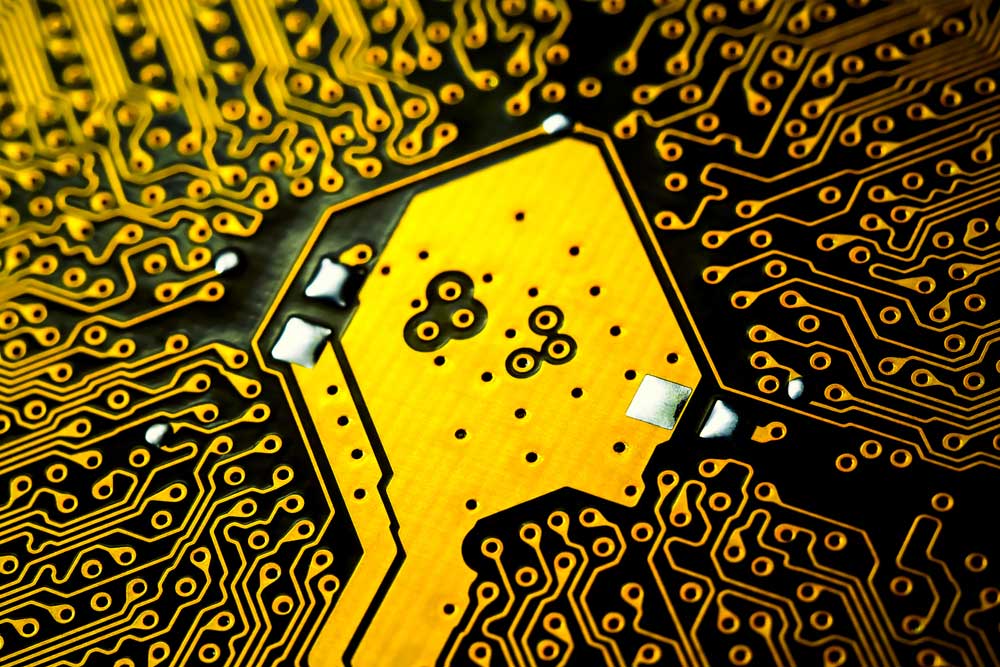
PCB Controller Installation
- Can be installed within the same circuit as the board it manages or on a separate PCB if space is limited.
Key Materials for Building and Assembling PCB Controllers:
- Substrate Material: The base material provides the frame to hold the circuit and components. Most rigid PCB controllers use FR4 substrate boards, while Rogers material is used for high-frequency circuits.
- Copper: Used for creating the laminated circuit and the exposed pads for attaching components.
- Solder Mask: Covers copper traces on the outer boundaries to insulate and protect them from oxidation.
- Silkscreen: Marks the PCB with labels, part numbers, and component placements to support the chip or microcontroller.
- Surface Finish: Protects exposed copper pads from oxidation using finishes like ENIG, which also provides excellent flatness and solderability.
- Solder Paste: Used to attach supporting components, including the controller, to the board.
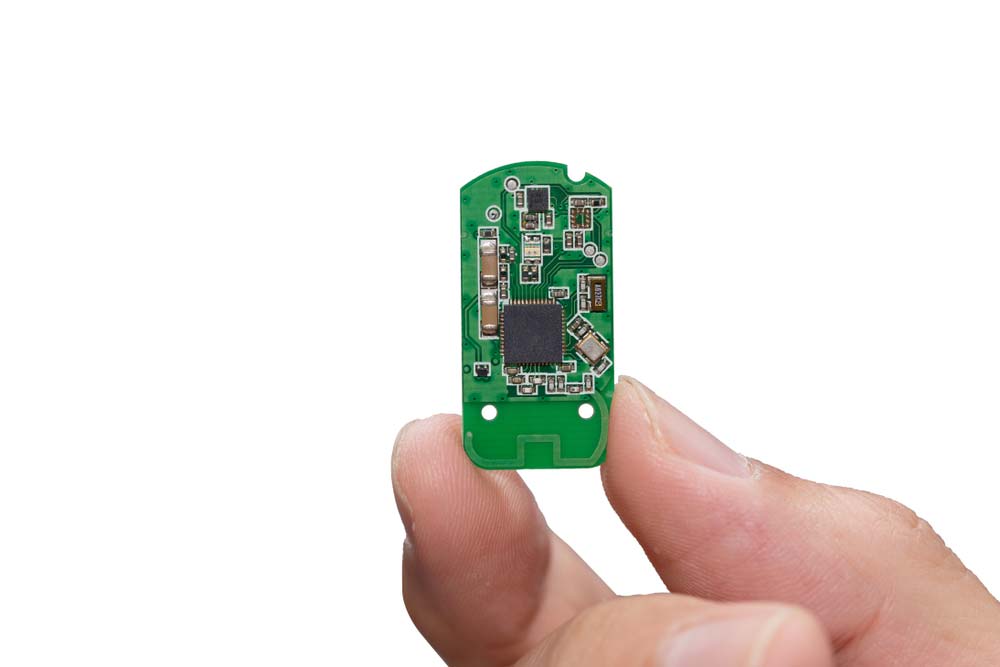
How To Design a PCB Controller
Designing a PCB controller involves several steps, each critical to ensuring efficiency and functionality:
Step 1: Define the Requirements
Begin by understanding the controller’s purpose. What components will it interact with? What are the input/output needs? Defining the board’s specifications from the start ensures that the design meets its intended function.
Step 2: Choose the Right Components
Selecting the right microcontrollers, power regulators, and connectors is vital. Ensure the components align with the design’s power, size, and performance requirements to avoid inefficiencies later in the process.
Step 3: Schematic Design
Develop a clear schematic that outlines the logical flow of the circuit. This includes designing the power distribution paths, signal routes, and data paths in a way that reduces clutter and improves functionality.
Step 4: PCB Layout Design
The physical placement of components is key. Place power-sensitive components closer to the power supply, while ensuring proper separation of noisy components to maintain signal integrity. The layout should prioritize compactness without sacrificing performance.
Step 5: Testing and Simulation
Before moving to production, simulate the design using software tools to verify functionality. Look for potential signal integrity issues, thermal problems, and other performance challenges that could arise during actual use.
Common Mistakes in PCB Controller Design and How to Avoid Them
Avoid these common pitfalls to ensure your PCB controller is efficient:
- Overcomplicated Layouts: While it may seem beneficial to add more components or features, overly complex layouts can introduce unnecessary interference and manufacturing issues. Simplifying the design often results in better performance.
- Insufficient Thermal Relief: Ensure your design has adequate heat dissipation paths. Without proper thermal relief, components can overheat, leading to failure.
- Inefficient Power Distribution: Poorly designed power and ground planes can lead to unstable performance. Ensure that power distribution is carefully planned to avoid voltage drops and noise.
- Incorrect Component Selection: Choosing incompatible or inefficient components can lead to poor performance. Always ensure your components match the design’s requirements for power, size, and operating conditions.
Tools for Designing Efficient PCB Controller Boards
To design a high-performance PCB controller, the right tools are essential:
- PCB Design Software: Tools like Altium Designer, Eagle, and KiCAD offer comprehensive design environments where you can create schematics, design layouts, and simulate performance before production.
- Simulation and Testing Tools: Using SPICE simulators or thermal analysis software helps catch potential performance issues during the design phase. These tools allow you to test signal integrity, heat distribution, and overall functionality.
- Prototyping Tools: Rapid prototyping ensures that your design performs as expected in real-world conditions. By testing physical prototypes, you can make adjustments before full-scale production, saving time and costs.
Applications of PCB Controller
You can find PCB controllers in these electronics.
- Consumer electronics devices
- Medical equipment (MRI, X-ray machines)
An MRI machine
- Industrial equipment
- Automotive equipment
A car headlight position control module
Embedded Systems
Embedded systems usually incorporate PCB controllers like Field Programmable Gate Arrays and microcontrollers internally.
These controllers communicate with I/O peripheral devices to receive input signals for controlling the board.
Contact OurPCB
At OurPCB, we specialize in designing and manufacturing custom PCB controller boards. Whether you need standard designs or advanced multilayer solutions, we offer expert services to help bring your project to life. Explore our services or contact us for a consultation today!
Special Offer: Get $100 off your order!
Email [email protected] to get started!