- PCB Manufacturer
- PCB Assembly Service
- Flexible & Rigid Flex PCB
Flexible PCB Manufacturer Assembly Factory
Looking for a top-tier manufacturer for Flexible PCBs or Rigid-Flex PCBs? OurPCB delivers high-quality, custom-designed solutions with industry-leading specifications.





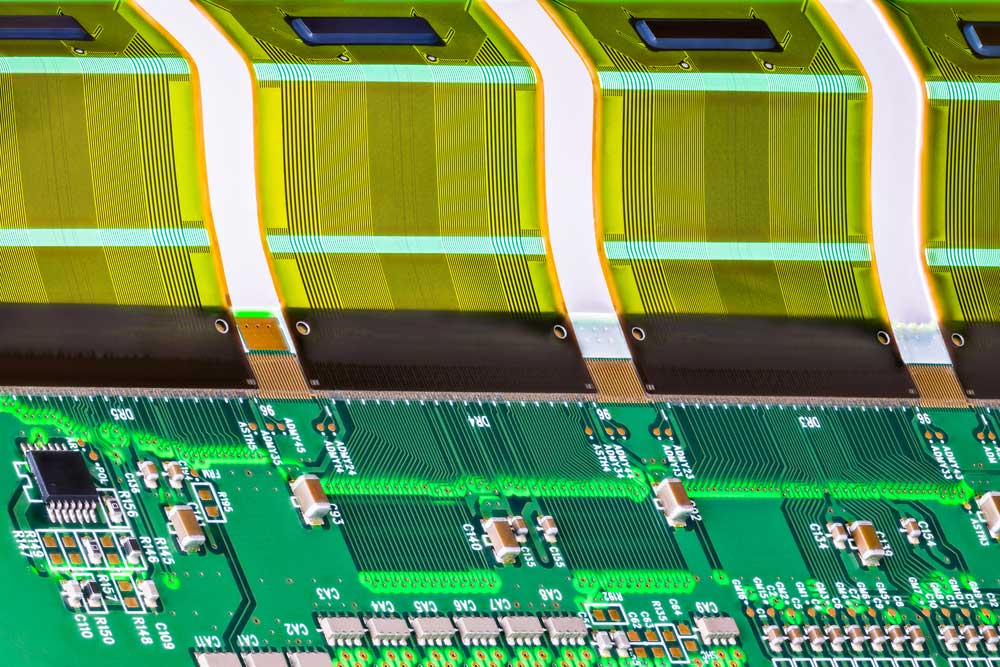





Our Flexible PCB Manufacturing Capability
Below is a detailed overview of our Flex & Rigid-Flex PCB capabilities, showcasing the key specifications and performance metrics that highlight our commitment to precision and quality in every project.
Project Item | Normal Capability |
---|---|
FPC Base Material (Adhesive) | ShengyiSF302:PI=0.5 mil,1 mil,2 mil;Cu=0.5 oz,1 oz ShengyiSF305:PI=0.5 mil,1 mil,2 mil;Cu=0.33 oz,0.5 oz,1 oz |
FPC Base Material (Adhesiveless) | SongxiaRF-775/777:PI=1 mil,2 mil,3 mil;Cu=0.5 oz, 1 oz (Ultimate:PI=1 mil,2 mil,3 mil;Cu=2 oz) Xinyang:PI=1 mil, 2 mil;Cu=0.33 oz, 0.5 oz, 1 oz Taihong PI=1 mil, 2 mil;Cu=0.33 oz, 0.5 oz, 1 oz Dubang AP:PI=1 mil, 2 mil, 3 mil, 4 mil;Cu=0.5 oz, 1 oz (Ultimate:PI=1 mil,2 mil,3 mil,4 mil;Cu=2 oz) |
Layer | 1-6 Layers (Ultimate:7-10 Layers) |
Thickness of Finished Product (Flex part,no stiffener) | 0.05-0.5 mm (Ultimate:0.5-0.8 mm) |
Size of Finished Products(Min) | 5 mm*10 mm (Bridgeless);10 mm*10 mm (Bridge) Ultimate:4 mm*8 mm (Bridgeless);8 mm*8 mm (Bridge) |
Size of Finished Products (Max) | 9 inch*14 inch Ultimate:9 inch*23 inch (PI≥1 mil) |
Impedance Tolerance | Single-Ended:±5Ω(≤50Ω),±10%(>50Ω) Ultimate:Single-Ended:±3Ω(≤50Ω),±8%(>50Ω) |
Impedance Tolerance | Differencial:±5Ω(≤50Ω),±10%(>50Ω) Ultimate:Differencial:±4Ω(≤50Ω),±8%(>50Ω) |
Tolerance of Finger Width | ±0.1 mm (Ultimate:±0.05 mm) |
Min Distance to the Edge of Finger | 8 mil (Ultimate:6 mil) |
Min Distance between Pads | 4 mil (Ultimate:3 mil) |
Minimum Laser Hole | 0.1mm |
Minimum PTH | 0.3mm |
Min NPTH Tolerance | ±2 mil (Ultimate +0,-2 mil or +2 mil,-0) |
Solder Bridge Min Width(bottom copper<2OZ) | 4 mil(Green),8 mil |
Solder Bridge Min Width(bottom copper 2-4OZ) | 6 mil,8 mil |
Overlay Colour | White、Yellow (printed character:White) |
Type of Surface Treatment | OSP HASL, Lead free HASL, Immersion gold, Hard gold, Immersion silver, OSP |
Selective Surface Treatment | ENIG+OSP,ENIG+G/F |
Our Rigid-Flex PCB Manufacturing Capability
Project Item | Normal Capability |
---|---|
FPC Base Material (Adhesive) | Shengyi SF302, Shengyi SF305 |
FPC Base Material(Adhesiveless) | Songxia RF-775/777, Xinyang, Dubang AP |
Low flow prepreg | Taiguang EM-37B; Ventec: VT-47N |
Common rigid board material | Refer to standard rigid board materials |
Special rigid board material | Arlon: 85N; Rogers: RO4000 series; Nelco: N4000-13 series; Ventec: VT-901 |
Layer | 2-30 Layers; review required: ≥20 layers |
Thickness of Finished Product | 0.3-4.0mm; review required: >3.0 mm |
Size of Finished Products(Min) | 10mm*15mm (no internal positioning designs, panel size <50mm*50mm) |
Size of Finished Products (Max) | 18inch*22inch; Ultimate:18inch*29inch |
PCB Manufacturing Process







What is the Cost of Flexible PCBs?
On average, flexible PCBs can range from $0.50 to $5.00 per square inch for standard designs and materials. However, this cost is not fixed and can vary based on several factors. The factors that influence the price include necessary assembly labor, prevailing labor rates, and the time required for assembly. Additionally, overhead manufacturing expenses and the design complexity of the board play significant roles in determining the final cost. To get a more accurate cost estimate, please use our free pcb quote form.
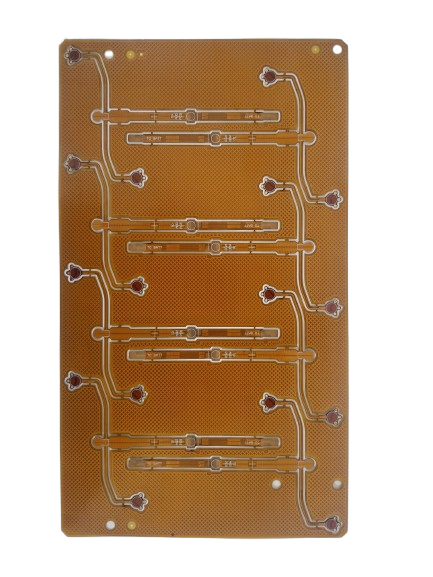



- Physical Size: Larger PCBs cost more, calculated per square inch.
- Circuit Construction: Costs depend on materials, layers, and pads. Extra layers or high-quality materials increase costs.
- Volume: Higher volumes result in higher costs.
- Layers: More layers mean higher assembly costs. Opt for single-sided FPCBs if possible.
- Finishing: Premium finishes guarantee longevity but come at a higher price.
- Holes: More or smaller holes drive up costs due to increased drilling complexity.
- Flex Board Types: Layer count influences price significantly.
- Custom Features: Specifications like solder mask clearance, side plating, or contoured edges add to the cost.
- Minimize flexible layers, as rigid laminates are more cost-effective.
- Reduce overall layers to lower the need for additional materials.
- Limit controlled impedance requirements to necessary values only.
- Opt for flexible copper thickness, approximately 1/3 oz.
- Purchase FPCBs in bulk to reduce unit cost.
Flexible & Rigid-Flex PCB Lead Times Overview
Service Type | Lead Time |
---|---|
Standard PCB Manufacturing | 5-6 days |
Expedited Manufacturing | 24-48 hours |
PCB Prototyping (Quick Turn) | 1-2 layers: 5 days |
4 layers: 6 days | |
6 layers: 7 days | |
8 layers: 8 days | |
10 layers: 9 days | |
PCB Assembly | 4-25 days, depending on complexity and order volume |



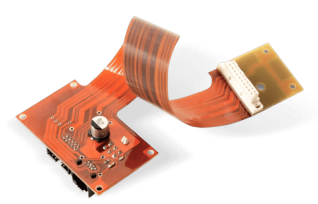



How are Flex & Rigid-Flex PCBs Manufactured?

- Step 1: Fabricate flexible laminates by bonding copper to PI film
- Step 2: Laminate coverlay and copper foil

- Step 3: Drill holes for vias and through holes
- Step 4: Electroplate holes to form conductive vias

- Step 5: Image and develop photoresist for circuit pattern
- Step 6: Etch away unwanted copper
- Step 7: Strip photoresist and apply solder mask over bare copper

- Step 8: Expose and develop a solder mask
- Step 9: Cure solder mask and apply surface finish

- Step 10: Punch or route PCB to final shape
- Step 11: Print silkscreen legends and conduct electrical tests

Step 12: Singulation and packaging
Millions of business and innovators use OurPCB
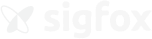
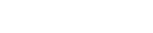
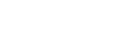


PCB Board Process
Order Received
- Component Procurement
- Preparation
- PCB Manufacture
- Make Process Flow
Soldering
- Solder Printing/Wave Soldering
- SMT/Plugging
- Inspection (repair if necessary)
- AOI (repair if necessary)
- Transfer
Parts Assembly
- Manual Assembly
- Cleaning
- Wire Screw
- Inspection
- Repair If Necessary
Finalization
- Final Confirmation
- Packing
- Shiping
Technical Capabilities
OurPCB offers flexible PCBs for innovative, space-saving designs. Starting at $172.50 for 5 units (1 layer, 100 mm x 100 mm), these PCBs are ideal for applications requiring flexibility and precision.
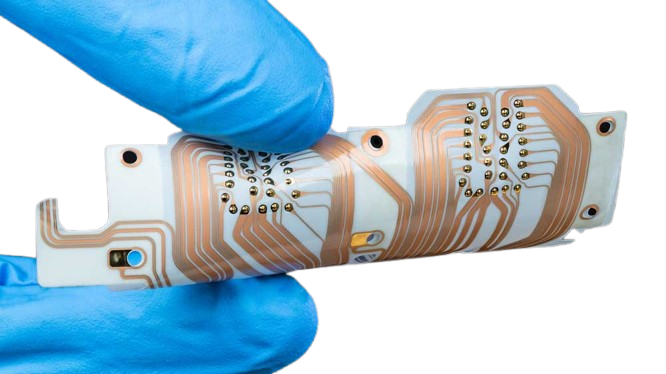



Capabilities & Services
- One-stop PCBA Services (PCB Manufacturing + Components Sourcing + Assembly)
- SMT Assembly + THT Assembly
- BGA Rework
- 60,000 Chips/Hour
- Down to 01005/0210 Size
- Accuracy<±40μm
- Min. QFN Pin Width/Space: 0.15mm/0.25mm
- Min. BGA Diameter/Space: 0.2mm/0.35mm
- Rigid, Flex, HDI, & High-speed Power Boards
- Up to 50 Layers
- 60GHz High Frequencies
- Min. Trace Width/Spacing: 2.5mil/2.5mil
- AOI, X-ray, ICT & FCT Testing
- Controlled Impedance
- ISO 9001, ISO 13485, ISO 14001, IATF 16949, IPC-A-610, UL Certified
- Automotive, Medical, & Military-grade PCBA Manufacturing


Mon-Fri: 24 hours,
Sat: 9am-6pm, GMT+8

Reach us at
[email protected]
24 hours online

+86-199-30589219
Mon-Fri: 24 hours,
Sat: 9am-6pm, GMT+8
FAQ's
What are Flexible PCBs?
Flexible PCBs can be bent, shaped, wrapped, or folded into any 2D or 3D shape. These features make flexible PCBs perfect for use in medical and surgical equipment, consumer electronics, automotive and space applications, and smart wearable devices.
What is the minimum order quantity for Flex & Rigid-Flex PCB manufacturing?
We have no minimum order quantity, allowing you to order anything from single prototypes to mass production runs.